As the COVID-19 pandemic took hold in early 2020, facemasks and other forms of personal protective equipment (PPE) quickly became top of mind – and in some cases hotly debated. To ensure proper performance, facemasks and PPE must meet the requirements of leading global standards and regulations.
Facemasks, as well as PPE items like gowns, coveralls, and shoe coverings, require strong, fully sealed barrier seams and bonds that meet standard requirements. There are several methods of PPE assembly, most notably ultrasonic bonding and adhesives.
Ultrasonics
Ultrasonic technology is among the preferred assembly methods for facemasks and other forms of PPE. The technology utilizes high-frequency sound waves that cause heating and plasticization of the nonwoven materials employed for PPE, creating high-quality, regulatory-compliant bonds that eliminate leaking issues.
Sonobond, a West Chester, Pennsylvania-based provider of ultrasonic bonding technology, offers SeamMaster ultrasonic sewing machines for assembling facemasks and PPE. The SeamMaster’s rotary operation – similar to a conventional sewing machine – channels the ultrasonic vibrations to soften and fuse synthetic materials. This creates smooth, soft-to-the-touch seams that are also sealed, secure and highly reliable.
“While ultrasonic ‘plunge bonding’ equipment also produces regulatory-compliant bonds, they cannot provide the rotary soft seam assembly that is gaining increased popularity as PPE and facemasks are being used more frequently and for longer periods of time,” says Melissa Alleman, vice president of Sonobond Ultrasonics.
Beckmann Converting, an Amsterdam, New York-based provider of ultrasonic laminating systems, is also servicing the PPE market, among others.
“A multitude of innovative and novel materials are flowing out of R&D units in companies globally targeting specific PPE and facemask applications,” says Ray Piascik, director of marketing for Beckmann. “In many cases, traditional manufacturing processes typical for PPE and facemask materials cannot be used with these new materials while maintaining desired performance of the final product. Ultrasonic bonding technology has the capability to achieve bond strengths with minimal impact on the performance of individual layers of textiles, nonwovens and films.”
Ultrasonic lamination uses the conversion of acoustic energy to heat to form spot welds of specific size in exact locations. This technique is an ideal method to join layers of different or similar materials (nonwovens, films, composites, or fabrics) into a single composite or laminate. Beckmann’s production lines for PPE and facemasks can handle raw materials up to 126” wide and deliver rolls of finished product slit accurately to desired widths with inline slitting, wound to lengths optimal for assembly equipment.
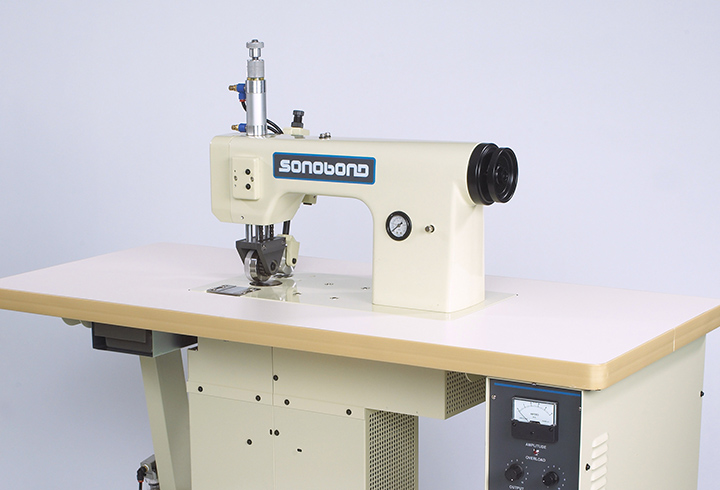
Adhesives
Adhesives are another method for bonding and sealing facemasks and PPE without puncturing the substrates.
H.B. Fuller, a St. Paul, Minnesota-based provider of adhesives, offers hot-melt solutions for the assembly of disposable PPE items. The company’s technology is based on a pressure-sensitive adhesive (PSA), which offers excellent adhesion to a wide variety of substrates.
Disposable surgical gowns, for example, are assembled by laminating two nonwoven pieces to both sides of a barrier film. Adhesives can be used, for example, on surgical facemasks for strap attachment, mask forming and fabric lamination. Surgical drapes are assembled by attaching typical components, such as nonwoven anesthesia screen, poly arm covers, and nonwoven main panels using adhesives. Disposable surgical gowns are assembled by laminating two nonwoven pieces to both sides of a barrier film (nonwoven, barrier film, nonwoven).
Hot-melt adhesives are comprised of three key elements: polymers, resins and plasticizer and can bond similar and dissimilar materials. They are applied to an initial material when in a liquid or molten state. After a short open time, the second material is brought into contact. At this point, the adhesives cool down and set quickly, bonding the two together.
With over 500 field and lab-based technical experts around the world, H.B. Fuller works with customers to identify the right adhesive solution for specific PPE applications.
Web adhesives, such as those offered by Colombes, France-based Bostik, offer excellent adhesion to a variety of nonwoven materials. As a result, they provide process and performance advantages, including ease of use for bonding or laminating nonwovens in medical facemask assemblies. Web adhesives are formed through a process in which hot-melt adhesives are formed into a web-like nonwoven material that handles like fabric. Web adhesives offer an optimized weight to performance ratio, meaning that though they are lightweight, they still offer sufficient bond strength.
Bostik’s web adhesives possess low basis weight, which means that manufacturers can choose the ideal level of porosity to meet their specific medical facemask application needs. Each medical facemask is then able to offer the needed performance level for its required usage.
Bostik’s web adhesives undergo strict quality-control processes before being sent to manufacturers. These processes are designed to reduce scrap waste and potential plant variations, delivering a consistent, high-quality product that’s ready for assembly.
The appropriate bonding method for the application depends on a number of variables. A strong understanding of the materials in use, standard performance expectations and the capabilities of the bonding technology will ensure that the chosen method fits the requirements of the application.
For more information, visit:
beckmannconverting.com
bostik.com
hbfuller.com
sonobondultrasonics.com