Gas turbines have substantially enriched societies’ living standards, whether by generating shaft power or thrust to enhance our daily lives and activities. We take electrical sockets for granted, relying heavily on power to operate our cities and appliances. Today, gas turbines still dominate a significant role in the global energy mix as far as fossil fuel combustion is concerned. However, to meet the 2 degree C target, efficient and affordable power generation among other alignments must be in place to move humanity toward sustainable, equitable, and prosperous economies.
The Critical Importance of Gas Turbine Performance
Gas turbines are widely used in power generation, where quick startup, high availability and reliability are needed to meet the increasing power demand under all steady-state and transient conditions. Globally, sources indicated that power generated from land-based gas turbine amounts to one-quarter of global generation [1]. The International Energy Agency highlighted in their recent report that the demand is forecasted to grow by 3.3% in 2024 due to a prosperous economic outlook, although it has had a slow growth recently[1]. Ultimately, gas turbine performance emerges as the most critical operational parameter to assess their power generation success and minimize the economic impact of outages. The rising cooling demand, population growth, and the scale, speed, and scope of urbanization emphasize the importance of enhanced gas turbine performance while adhering to environmental regulations. Gas turbines operating in environments sustaining high dust concentration and extreme temperatures suffer from performance degradation. Power plants and grids are strained to meet the rising cooling capacity to avoid load-shedding and, eventually, power outages. Air conditioning systems use about one-fifth of the global power generation[2]. That would emphasize better building design, stricter building codes, and efficient air conditioning installation, which would help counter the growth in cooling-related electricity demand. Ultimately, sourcing responsible power generation and embracing sustainable living standards harness the opportunity for a decarbonized economy and recognize our environmental limits.
The Working Principles
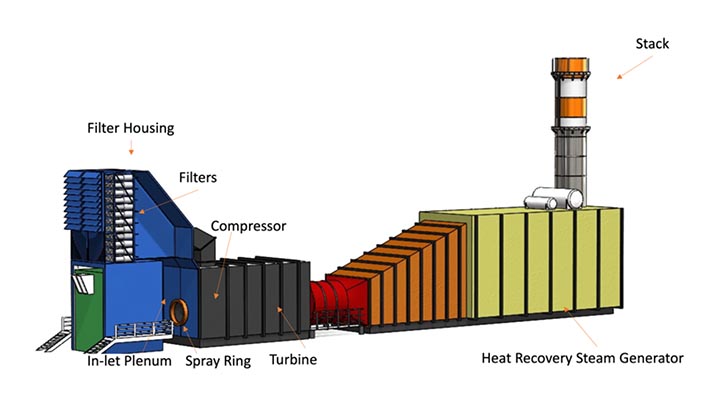
The essence of the gas turbine operation lies in accelerating a gas to high velocities by increasing its specific enthalpy and converting it to kinetic energy. Atmospheric air is drawn through a filter house installed at an evaluated level. Air is then passed through the filtration stages before entering the compressor via the bell mouth. The cleaned air is then compressed to a high pressure and temperature to enter the combustion chamber, where fuel is added, and combustion occurs. Energy is then extracted from the hot pressurized exhaust gas, thus reducing pressure and temperature. The energy is converted to work in the turbine, 50 to 60% of which drives the compressor, and the rest drives the generator to produce power or operate mechanical equipment (gas compressors and pumps). An example of a combined cycle power plant is shown in Figure 1.
Gas Turbine Performance Degradation
Gas turbines operate in different climates and confront multiple atmospheric contaminants with various concentrations that can lead to performance degradation and component deterioration[3].
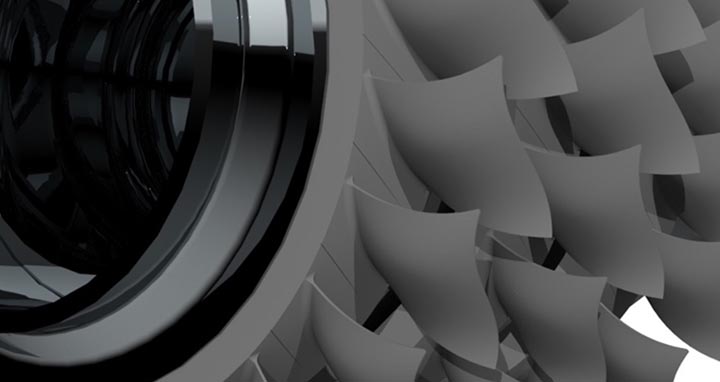
A standing challenge of all gas turbine engines is compressor fouling. It occurs when various contaminants deposit on the compressor assembly, reducing the throat area between the blades, as shown in Figure 2. Such deposition (Figure 3) reduces the mass flow rate, pressure ratio, compressor efficiency, and surge line leading to performance degradation and more fuel has to be burnt to maintain the designed power output[4,5]. Consequently, turbine blades will experience higher firing temperatures producing high thermal and mechanical stresses due to centrifugal force, vibratory and flexural stresses which negatively impact the turbine blades’ creep life[6,7].
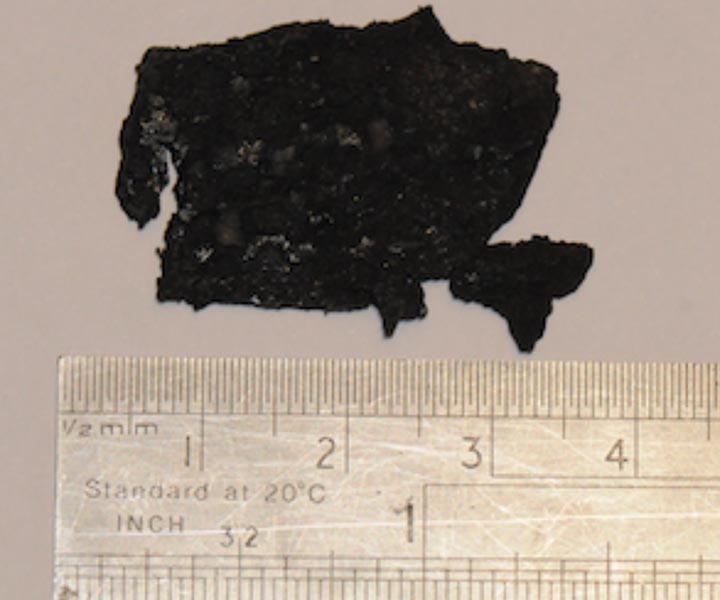
Various air filters as shown in Figure 4 are sought in land-based gas turbines to separate and retain particles through depth and surface deposition (Figure 5). On the other hand, surface filtration facilitates the filtration action through dust-cake formation on the surface of filter media. The regeneration of the media is done by means of a pulse system to prepare it for an additional filtration cycle as shown in Figure 6. While two techniques have their own and common benefits and challenges, providing the required mass flow rate of air is essential to operate the gas turbine engine – starving the compressor of air cannot be an option. On the other hand, a fouled compressor degrades the engine performance, reducing power output and gas turbine availability. Research has suggested that 70% of the performance degradation comes from compressor fouling[8,9], highlighting the importance of air quality feeding the engine and the compressor washing solutions required to restore compressor assembly to its design point and performance[10,11]. Therefore, appropriate air filter selection is essential to strike a balance between particle capture and air permeability. Ultimately, the main objective at this stage is to feed the compressor assembly with the required mass flow rate of air that is fit for purpose.
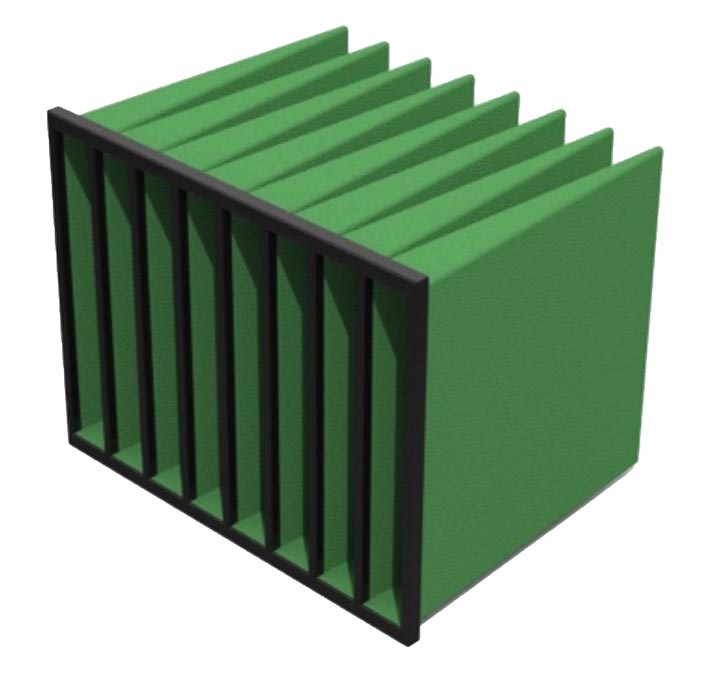
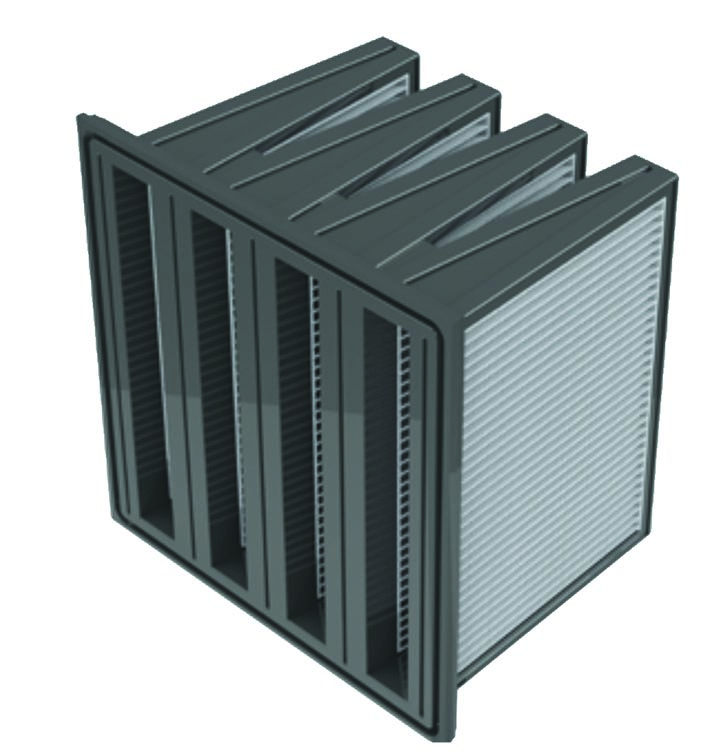

Figure 4: Various examples of static [A,B] and pulse filters [C] used in land-based gas turbine applications.
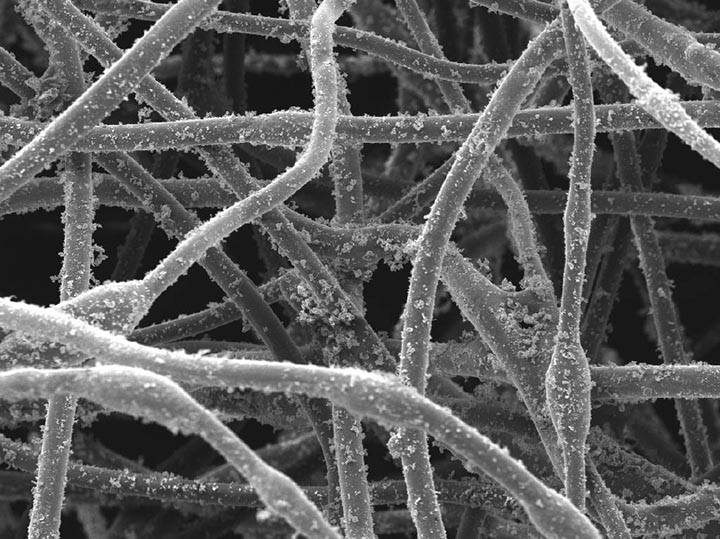

Figure 5: Typical examples of depth [Left] and surface [Right] particle depositions.
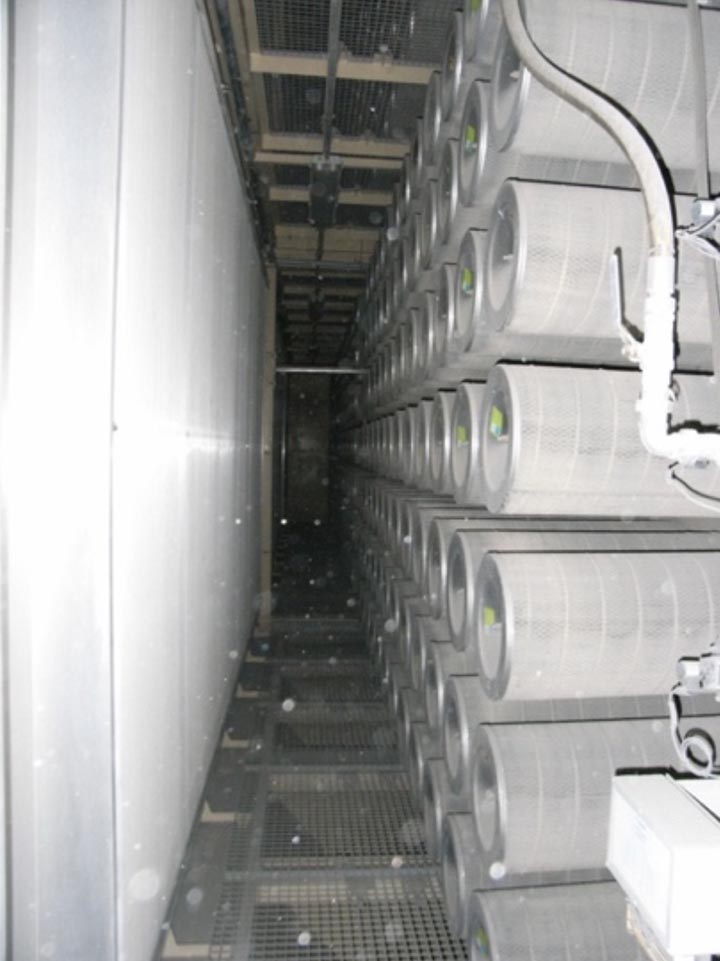
Geographic Location Sensitivity
The physical and chemical characterization of outdoor air is sensitive to a given geographic location and can influence the selection of air filters. While the role of efficient and permeable air filters cannot be overstated, one must be mindful of the specific requirements of gas turbines which can be dynamic, different, and challenging, relevant to the surrounding microclimate conditions. The real-time performance of installed air filters in gas turbine applications deviates from that predicted by laboratory results [12]. Such performance deviation could be attributed to variations in particle physical characteristics, loading conditions through filtration stages, operational, and environmental conditions.
Design Aspect for Gas Turbine Air Filtration
Several parameters influencing air filter performance include particle characteristics (size, shape), loading mechanisms during different operational conditions, and design parameters (pleat count and effective surface area). Figure 7 illustrates different particle shapes and size ranges found in loaded filters. The size and shape of particles play a role in determining the dominant capture mechanism and, eventually, their depth or surface deposition on the filter medium. On the other hand, suspended particles and their loading characteristics are size and shape dependent. Furthermore, filter medium pore structure characteristics can also influence filter loading and clogging.
Given the tremendous mass flow rate required, any low concentration of particles will amount to great particle loading, leading to a higher pressure drop, which is inversely proportional to permeability. At such higher mass flow rates, and subject to the structural stability and characteristics of the filter media used, pleats and pleated panels can deform, causing surface area losses leading to permeability reduction. This highlights the importance of the media’s physical characteristics and structural integrity to sufficiently support the induced forces by the mass flow rate. From an efficiency perspective, reduced air permeability due to increased particle loading and/or inappropriate filter media selection can compromise the overall filter efficiency.
The Effective Surface Area Concept
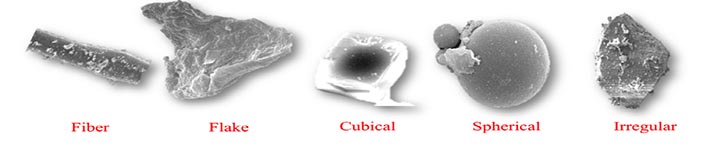
Adding surface area to a filter cartridge by means of increasing the pleat density is not the point; the point is introducing effective surface area that participates in the separation and retention process. In addition to the media characteristics and operational and climate conditions, filter design can play a role in engineering the flow dynamics through a pleated filter cartridge for optimum filter performance. The filter’s permeability and particle capture should be a major consideration of gas turbine operation to enhance its performance. Therefore, optimized filter design, appropriate media selection, and aerodynamic filter performance can help achieve the desired efficiency without impeding the flow. Filter deformation and eventual failure and/or prematurely clogging lead to unscheduled maintenance and disruption in the gas turbine operation. For this reason, air filters cannot fail in land-based gas turbines.
The Order of the Day
Operating a gas turbine close to the design point is essential to utilize the installed engines’ maximum performance. Embracing sustainability as we aim to decarbonize our economy requires that all sectors contribute at an incredible speed. Given that we have ambitious dreams to chase when it comes to a sustainable planet and digital future, the role of efficient processes becomes well-pronounced.
Our reliance on fossil fuels cannot be overlooked. However, their use has contributed to climate change over the last 100 years, and it is time to re-engineer our minds and gears toward enhanced performance and responsible consumption of our fossil fuels. Planet Earth needs responsible habitants that allow it to regenerate itself if we aim to fulfill the promise to our grandchildren of a healthier planet than the one we inherited.
To support more environmentally friendly energy policies and embrace sustainable living, the order of the day must be to grant renewables a greater role in the global energy mix and accompany them with responsible combustion.
Refernces:
- IEA. “Electricity Market Report Update”, Outlook for 2023 and 2024. International Energy Agency.
- IEA (2018), The Future of Cooling: Opportunities for energy-efficient air conditioning, International Energy Agency, Paris.
- Goldberg C, Nalianda D, Laskaridis P & Pilidis P (2018). Installed performance assessment of an array of distributed propulsors ingesting boundary layer flow, Journal of Engineering for Gas Turbines and Power, 140 (7) Article No. 071203: GTP-17-1588.
- Kurz, R. and Brun, K. (2012), “Fouling mechanisms in axial compressors,” Journal of Engineering for Gas Turbines and Power, vol. 134, no. 3, pp. 032401.
- Meher-Homji CB. Gas turbine axial compressor fouling – a unified treatment of its effects, detection and control. Int J Turbo Jet Engines 1992;9(4):99–111.
- Patil A.A., Shirsat U.M., (2012). Study of Failure Analysis of Gas Turbine Blade. IOSR Journal of Engineering (IOSRJEN), ISSN: 2250-3021 ISBN: 2878-8719 PP 37-43 National Symposium on engineering and Research.
- Jordal, K., Assadi, M. & Genrup, M. (2002). Variations in Gas-Turbine Blade Life and Cost due to Compressor Fouling – A Thermoeconomic Approach. International Journal of Thermodynamics, 5 (1) , 37-47
- Saravanamuttoo, H.I. H., Cohen, H., Rogers, G.F. C. and Straznicky, P.V. (2009), Gas Turbine Theory, Sixth ed, Pearson Prentice Hall, Harlow Essex England.
- A. Kermanpur (2008), “Failure analysis of Gas turbine compressor blade;” Engineering failure analysis; 15 pp 1052-1064.
- R. Agbadede, P. Pilidis, U.L. Igie, I. Allison, Experimental and theoretical investigation of the influence of liquid droplet size on effectiveness of online compressor cleaning for industrial gas turbines, Journal of the Energy Institute, Volume 88, Issue 4, November 2015, Pages 414-424, ISSN 1743-9671, http://dx.doi.org/10.1016/j.joei.2014.11.002.
- U.Igie, P. Pilidis, D.Fouflias, K.Ramsden, and P. Lambart, “Online
compressor cascade washing for gas turbine performance investigation,” ASME2011 Turbo Expo: Turbine Technical Conference
and Exposition, American Society of Mechanical Engineers,
pp.221 2011. - Al-Attar I.S., 2011. “The effect of pleating density and dust type on performance of absolute fibrous filters,” doctoral diss., Loughborough University Institutional Repository.