In an industry using high power inputs, even small capacity increases can mean big savings for customers. The introduction of layering techniques is a game changer for the industry.
Liquid filter manufacturers face constant pressure to produce longer lasting, more efficient filters, as end-users typically want the most effective filtration technology that also minimizes change out costs.
Nonwoven materials commonly used to produce liquid filters — meltblown, wet laid, spunbond, glass and synthetic media — have not changed in decades and thus offer limited opportunity for step change performance in filter life. Liquid filters typically utilize only a single nonwoven media, limiting the overall effectiveness of the filter. Each media type has its own strengths and weaknesses, depending on the application, but none are able to provide equal filtration efficiency while also increasing filter longevity. Recognizing the need to advance filter technology, SWM International has collaborated with filtration industry leaders to develop a new solution to this global demand.
Ideation to Innovation
Through decades of experience and partnerships with filter manufactures around the world, SWM recognized the need for a filtration media that improves dirt holding capacity without sacrificing the life and performance of the filter. As a producer of many different high performance materials from films to nettings to nonwovens, SWM’s product development team came up with the idea of creating a composite materials solution incorporating the strengths of several different nonwoven media into one product, specifically designed for use in liquid filters.
The evaluation stage began with baseline testing of all existing nonwoven media, with particular focus on particle size, efficiency, and dirt-holding capacity. SWM acquired a single pass test rig to accurately model the lifespan of various nonwoven media in liquid filter applications. By incorporating multiple nonwoven technologies into a single engineered nonwoven composite, SWM uncovered a high-capacity media of highly specialized, engineered layers designed and tested to maximize filter life while maintaining high levels of efficiency.
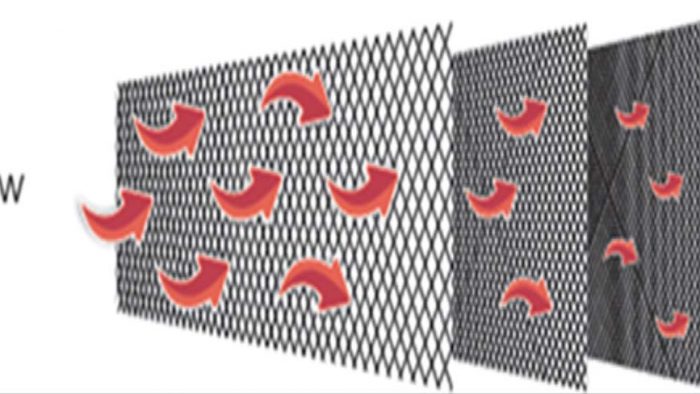
“Following a recent development in filtration for gasoline, SWM realized it could significantly improve the dust holding capacity of a filter by utilizing a unique composite structure,” said Andy Platt, director of research and development for SWM. “Using the recent investment in test equipment we were able to develop individual layers, which when combined together with drainage and support layers, significantly increased filter life.”
Independent third-party test results validated up to three-times higher dust-holding capacity, compared to leading nonwoven materials used in liquid filters. This means that in some cases, multiple filtration stages can be eliminated by using a filter with SWM’s new single high-capacity composite. The increase in dust-holding capacity extends filter life and reduces filter replacement costs. The density gradient properties show even dirt loading throughout the media and efficiencies are maintained at targeted particle sizes.
A Trusted Partner
In an industry using high power inputs, even small capacity increases can mean big savings for customers. The introduction of layering techniques is a game changer for the industry, and Delstar™ High-Capacity Composite is just one of the solutions SWM provides to its global customers.
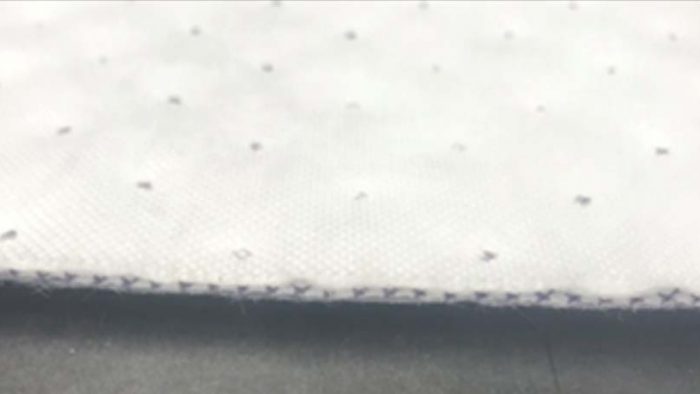
SWM is not only a leader in liquid and process filtration, but has been supporting air filter manufacturers for years. SWM nonwovens are known for high performance, quality and reliability and provide material solutions for both mechanical and triboelectric-based HVAC applications where low pressure drop, high efficiency, and high dust holding are important. SWM is also a leading producer of feed spacers and center tubes for reverse osmosis membrane manufacturers.
SWM embraces customer collaboration with a focus on engineering solutions for customer needs today and tomorrow. Contact SWM International to learn more about films, nettings, and nonwovens for the filtration industry.