Compared to Traditional E-beam Processes, Laser Drilling Produces High-quality Filter Parts
Far More Cost Effectively Than Traditional Manufacturing Methods
Fiber lasers are the tool of choice for precision metal work. For metal cutting applications, fiber lasers dominate due to their combination of speed, flexibility and precision. The advent of handheld welding solutions promises to quickly grow laser’s share over traditional techniques due to similar advantages. Years ago, the aerospace industry adopted laser drilling for perforating high performance metal parts to improve thermal performance. Now, advances in the productivity and precision of fiber laser drilling have
begun to disrupt the industrial filter industry (Figure 1).
Filters are porous devices which remove impurities as material passes through. The quality of the filtered product relies on the uniformity and cleanliness of the filter holes. Lasers are a non-contact drilling technique which has no mechanical wear associated with tooling, so excellent hole uniformity is maintained over a lengthy fabrication process covering a large surface. In many cases, the smaller the holes, the better the filtering. Lasers are particularly suited to drilling holes < 100 µm diameter, which are challenging dimensions for traditional alternatives like chemical etching or mechanical punching (Figure 2).
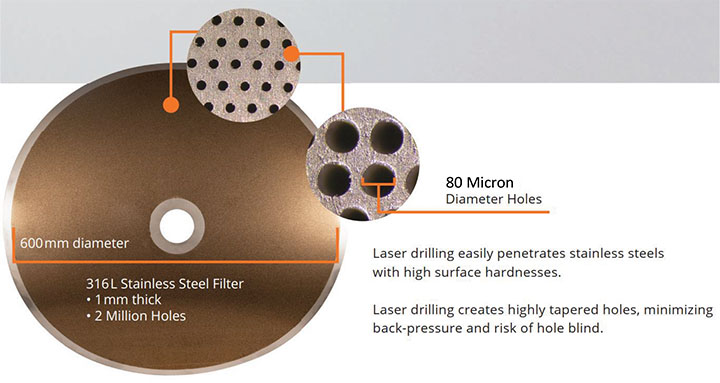
Sustainability policies create new, demanding applications for high performance filters which laser drilling is uniquely able to fulfil. Plastic recycling plants melt incoming garbage, then pass the liquid through a sequence of filters, before re-solidifying the filtered material into recycled plastic pellet feedstock. Products made of recycled plastic, for example PET water bottles, must meet the high standards of the food and beverage industry. Laser-drilled filters featuring hole diameters in the 60-80 µm range are a field proven solution meeting these high standards.
Laser Drilling Materials
Drilling of common materials like stainless steel is accomplished by focusing an intense fiber laser beam to a spot diameter as small as 40µm. The intense laser melts and vaporizes the metal at a high rate with excellent consistency. High pressure nozzles direct gas which efficiently remove liquid and gaseous metal enabling the laser to drill deeper. In a short amount of time, usually just a few tens of microseconds, the laser punctures the backside, and the hole is complete. The laser is turned off, quickly repositioned, and the process repeats. In this manner, filters numbering millions of holes are fabricated at great speed with outstanding precision and uniformity. An excellent feature of laser drilled holes is the natural taper, meaning the exit diameter on the backside is smaller than the input side. This creates a useful funneling effect, while resisting harmful backflow through the filter.
Laser drilling is a flexible technique able to employ multiple methods to optimize hole quality and throughput. The simplest is single shot drilling in which a single burst of energy penetrates the entire sample thickness. Single shot is the highest throughput technique, enabling a modulated laser to produce hundreds of holes per second.
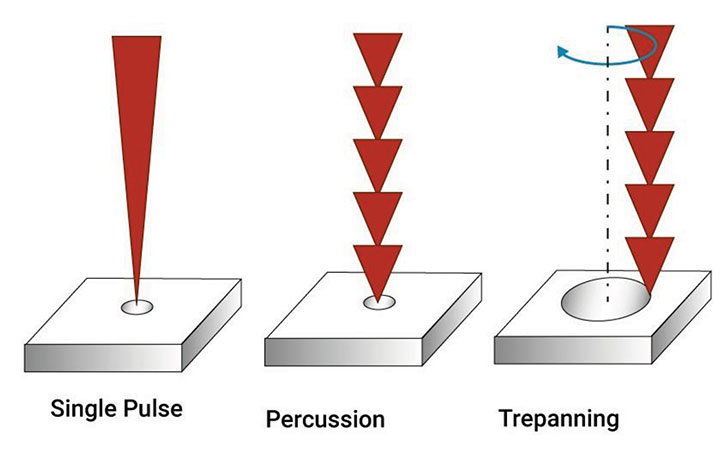
Multi-shot, or percussion drilling, utilizes multiple laser bursts to minimize the overall thermal impact of the energy required to puncture the substrate. Percussion drilling is often accomplished in concert with a galvanometric scanner and pulsed lasers which provide tens or hundreds of thousands of shots per second. This technique is most popular for microfabrication, where precision and quality requirements trump throughput. By repeatedly scanning the laser over multiple spots, high quality holes are created with minimal heat affected zone. The throughput challenges of multi-shot drilling are somewhat offset by its ability to create many holes in parallel (Figure 3).
Three Laser Drilling Techniques
A third technique called trepanning moves the laser energy in a spiral trajectory around the perimeter, resulting in a hole which is cut, rather than drilled. Trepanning is desirable for larger holes, because no energy needs to be expended to remove center material from the cut-out area. When trepanning, the laser spot may be moved either using mechanical or optical means. Large diameter holes of excellent quality are realized, but generally at a slower rate than is achieved by single shot or percussion drilling methods.
Throughput is maximized when “on the fly” techniques are employed, but precise timing is required (Figure 4). On the fly continuously moves the drilling head optic over the sample, without stopping to drill each position. By avoiding the inertia loss of stops and starts, on the fly maximizes laser utilization and drilling rate.
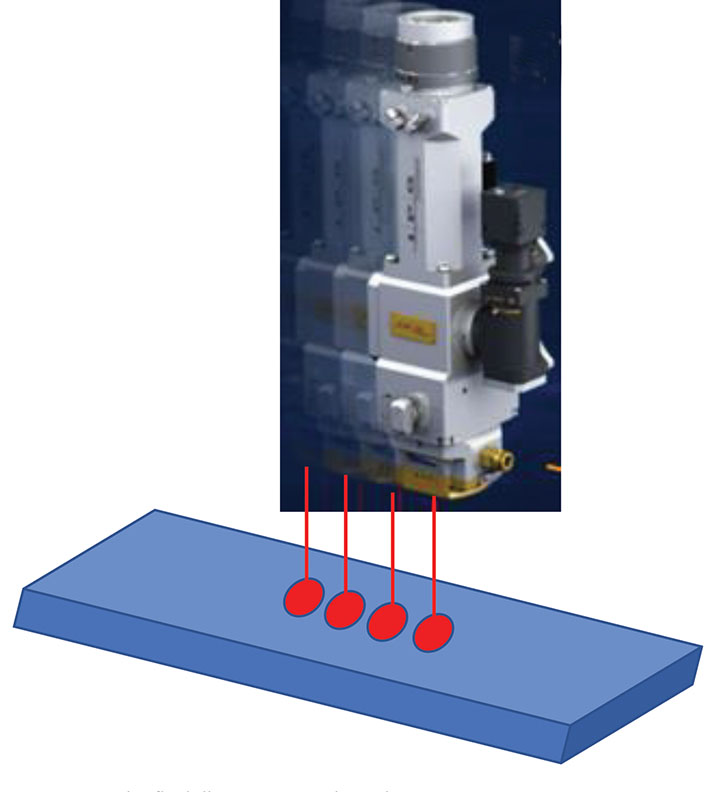
Filter fabrication is normally accomplished using parallel rows drilled by rastering the laser beam across the substrate in continuous motion. To ensure precision spacing and hole quality across the entire filter, heat input from the laser must be managed, else the substrate’s thermal expansion may bow upwards. The outer regions of the substrate are clamped to ensure the substrate does not shift laterally. Striking a delicate but repeatable balance between precision, quality and throughput is the filter driller’s art.
Selecting the correct laser, machine and perforation technique depends on substrate material type, thickness, hole diameter requirements. Powerful laser sources capable of single shot drilling are preferred for throughput sensitive tasks, especially in the case of thicker substrates and larger hole diameters which better resist the thermal load placed by the laser energy. The LaserCube driller is able to cover the full range of single shot, multishot and trepanning techniques by providing a single, flexible platform. On the fly drilling of small (<100µm diameter) holes in substrates up to 1mm thick can manufacture filters having 500,000+ holes on a tight pitch at speeds of 300-500 holes per second. When set up for thicker (up to 1.5mm) material, larger (e.g. 200µm diameter) holes may be created at a rate up to 75 holes per second.
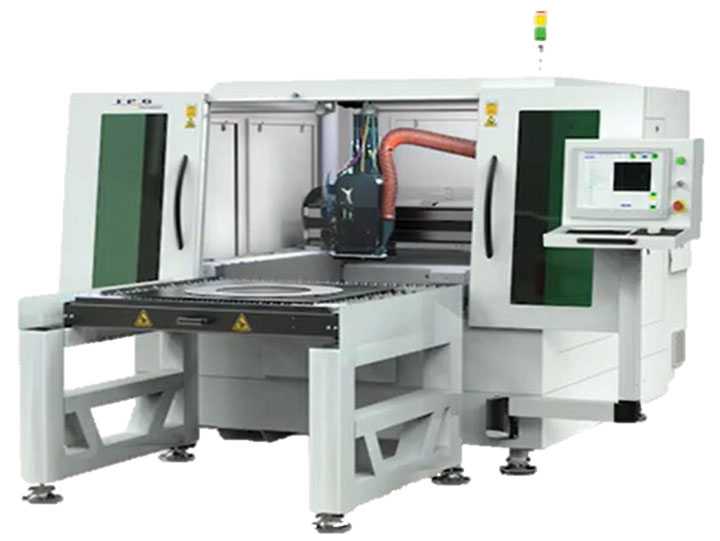
The fiber laser is a flexible source. Important features like hole diameter, taper and pitch are easily altered by adjusting laser and machine parameters. Unlike traditional methods, laser drilled hole features may be changed on the fly enabling a tool to drill multiple hole types on a single substrate without a tool change. Machines, such as the LaserCube provide this complete functionality over a 1 m2 metal working area. Fiber laser drilling of high quality holes is possible on stainless steel or Hastelloy sheet with thicknesses up to 10 millimeters while maintaining throughput up to 300 holes per second. The laser drilling machine incorporates cutting capability such that at the end of the process the filter outline is separated from the substrate, enabling the operator to unload a completed filter (Figure 5).
Filters fabricated using fiber lasers are increasingly adopted due to their numerous advantages. No alternative technique can realize tiny holes with excellent uniformity at extremely high throughput. For either sustainable manufacturing, or simply better manufacturing, filters fabricated using fiber lasers are an increasingly attractive solution.