Ensuring Pure Polymers Through Continuous Filtration
It is only within the past two decades that the critical role played by the filtration of molten polymers employed in the production of plastics and synthetic fibers has been fully acknowledged.
For a long time, the assumption by many manufacturers was that since they were dealing with “pure” raw materials – already filtered for impurities prior to polymerization – a filtration system at the melt extrusion stage represented an unnecessary expense, not only in terms of the initial investment, but also in the additional costs of spare parts and maintenance. Operators also often lacked the knowledge of the influencing variables on the final product to appreciate the full benefits that tailor-made melt filtration brings.
Contamination
In a comprehensive paper on the subject, Thomas Grimm-Bosbach, portfolio director for John Crane, a provider of a wide range of engineered products and services including filtration systems, head-quartered in Morton Grove, Illinois, has outlined the sources of contamination that needs to be eliminated by the melt filter.
A polymerization line firstly contains a large number of moving mechanical components which are subject to natural wear and tear, and particles can be released regularly as a result of the abrasion or wear of line components.
Most polymer melts also react very sensitively to strong changes in velocity gradients and can pool and degenerate at certain points in a line. Due to friction with fresh melt flowing past these dead spots, further particles can be repeatedly detached, leading to contamination.
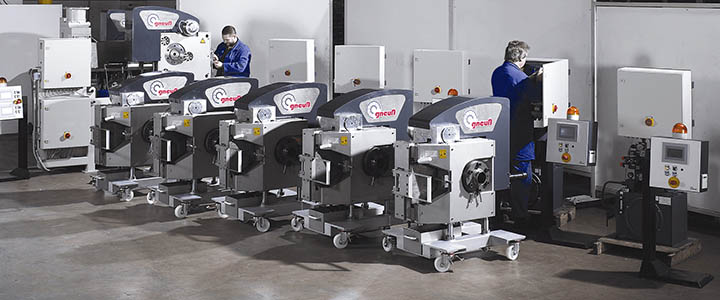
Equilibrium Reactions
Like almost all chemical reactions, Grimm-Bosbach explains, polymerizations are equilibrium reactions – the starting materials and the end products are present in a certain ratio, depending on the energy balance of the reaction, the states of aggregation of the ingredients involved and the system parameters.
Depending on the polymer, a varied mixture of monomers and oligomers (or products of side reactions) can be found in the polymer melt. These organic compounds cause the greatest problems in filtration. Such compounds are often activated by interactions with solid particles and then form slightly colored, flexible particles.
“Contaminated raw material is always a problem in further processing and in the past decade, the pressure from customers on manufacturers has ensured that poor quality raw material is becoming increasingly rare,” says Grimm-Bosbach. “However, even modern, well-maintained production lines sometimes produce polymers that fluctuate in quality, which is made readily apparent from the filter service life. Modern polymer processing equipment needs filters that can remove solid particles, degenerated material and flexible particles in order to ensure superior product quality.”
Filter Media
The porous filter media employed in melt filtration has to withstand temperatures of up to 400°C in continuous operation and provide pore sizes ranging from 1-100 microns. It needs to provide as little resistance against fluid flow as possible, demanding the highest number of pores per unit area.
These requirements limit the filter media that can be employed, since operational conditions are above the melting point of common polypropylene or polyester materials. As a result, the majority of filter media for polymer melt filtration are based on stainless steels, in the forms of either metal wire mesh, wire mesh laminates or nonwovens. These are supplied to the market by specialist companies including Bekaert, Spörl KG, Pall and Porvair.
Rotary Screens
An important development in making polymer melt filtration more efficient by ensuring continuous production of the extrusion system, has been the introduction of the rotary screen changer, as pioneered by Gneuss Kunststofftechnik, headquartered in Bad Oeynhausen, Germany.
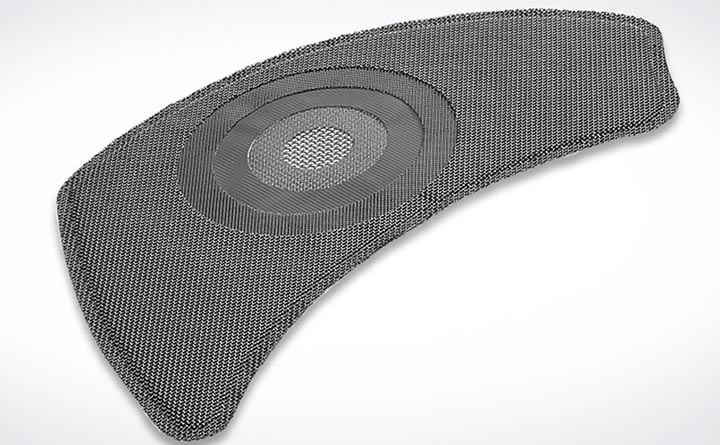
The well-known Gneuss RSFgenius is a fully automatic and pressure-constant rotary filtration system that incorporates a high-pressure segmental backflushing system. This purges the screen packs to ensure they are fully clean shortly before their re-entry into the melt channel.
Continuous Cleaning and Filtration
Small, measured portions of filtered polymer are continuously taken from the filtered side of the screen changer and injected with an adjustable pressure of between 30-80 bar backwards across the screen pack. The backflush is then ejected through the screen changer inlet block to the outside. Only a small segment of the screen area is being cleaned at any one time.
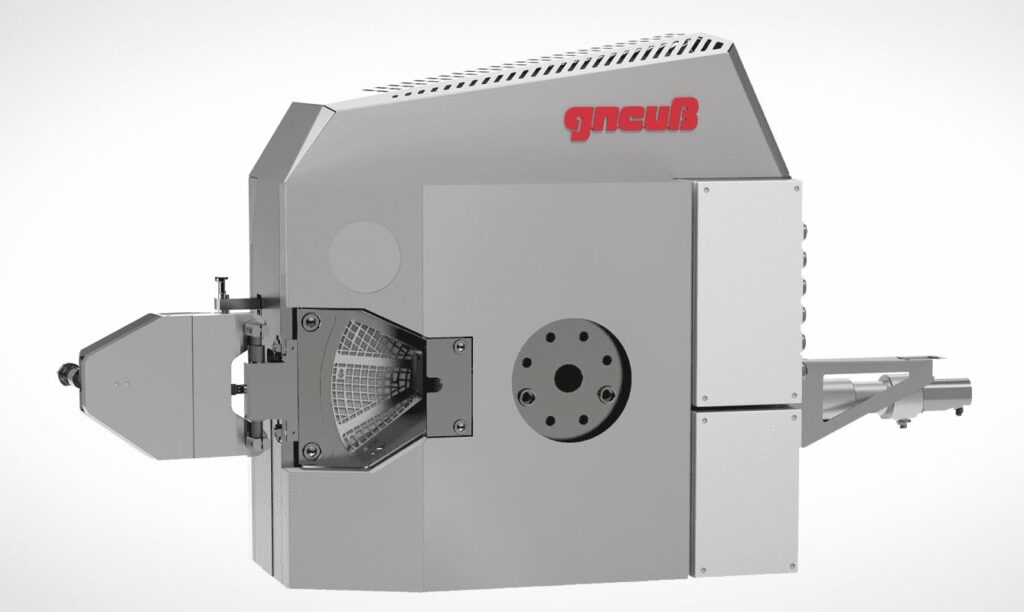
The filter disk, on which the screen cavities are located in a ring pattern, is completely encapsulated by the two filter blocks. Screens can be inserted into the cavities by opening a small hatch door giving access to them. As a result, the production process is not disturbed by the screen change procedure and thanks to the modular design of the filtration system, it is possible to replace the few wearing parts such as heater elements and bearing bushings during operation. Depending on the contamination level, a full screen change – which takes approximately 20-30 minutes – only needs to be carried out on a weekly or even monthly basis, with no influence on the production process or product quality.
The filter media combines square meshes and an optimized Dutch weave to ensure sufficient stability and optimum permeability enabling the back-flushing properties.
Constant Quality
By always keeping the size of the active filter screen area constant, the pressure, temperature, viscosity and throughput of the melt also remain constant, to guarantee the highest end product quality.
The short dwell time of the melt in the filtration system of less than a minute also enables rapid material or color changes to be carried out and filtration finenesses down to 1 micron are possible.
Gneuss supplies various RSFgenius models including versions with a very high filter surface exchange rate for highly contaminated materials and those with continuous back-flushing for extremely sensitive processes and polymers.
The small and compact design of the RSFgenius makes simple and cost-efficient integration possible even in very confined spaces while also ensuring extremely low energy consumption.
Industrial Waste
The purity of polymer melt becomes even more critical when recycling polymers and alongside the K Show in Düsseldorf in October 2022, Gneuss demonstrated its complete new OMNIboost recycling system for processing PET industrial fiber waste (POY) at its technical center in Westphalia, Germany.
Successful demonstrations of the system were carried out using fiber waste with a residual moisture level of 6% and an intrinsic viscosity of 0.64 dl/g.
The OMNIboost system is designed for recycling both post-industrial and post-consumer PET waste with a low bulk density, such as waste fibers or thin films. Without the need for any thermal pre-treatment, the material is fed into the 3C rotary feeder, which cuts and compacts the material as well as feeding it directly into the MRS extruder screw.
The Gneuss MRS extruder is based on a simple and rugged single screw extruder but is also equipped with a multiple screw section for optimized degassing. The patented multiple screw design has a section of extruder screw with a number of satellite screws, which rotate in the opposite direction to the main screw, creating a huge surface area and ensuring an extremely rapid surface area exchange rate. This ensures unparalleled degassing performance in the melt phase, with minimal stress on the material. It can
decontaminate post-consumer PET to food contact standard requirements without the need for thermal pre-treatment of the material prior to extrusion.
After passing through the extruder, the polymer melt is filtered with an RSF-genius which ensures that even with high contamination loads, fine filtration is possible without pressure or flow disturbances and with minimized polymer loss.
Controlled Viscosity
Still in the melt phase, the polymer flows into the Jump Liquid Phase IV booster reactor. The viscosity of the melt is measured both at the inlet and outlet of the reactor. The viscosity is boosted to the required level by regulating the vacuum level, residence time and surface area exchange rate in the reactor vessel. With an assured, constant output viscosity the material can be fed to the production process while still in the melt phase. By ensuring the polymer remains in the melt phase from the extruder to the final processing stage, the OMNIboost recycling process represents a fast and efficient way for reprocessing PET where a viscosity boost is required.
Extraction Under Vacuum
Gneuss reports that in 2011 that the Belarussian fiber producer Mogilev Khimvolokno pioneered the processing of agglomerated wet and spin finish oil-treated PET industrial fiber waste with its MRS extruder. This very successful application of the MRS extruder showed how both the moisture and the spin finish oils could be efficiently and reliably extracted under vacuum in the extruder.
It was this and successive installations that led to the latest PET recycling system being delivered by Gneuss to the Korea Textile Development Institute (KTDI), based near to Daegu, in South Korea, during 2023.
The emphasis at KTDI will be on manufacturing pellet/chip for high quality fibers, which require fine filtration and naturally, an RSFgenius was specified.
Big Bags
Another producer of extrusion and recycling systems for polymers and plastics is Starlinger, headquartered in Vienna, Austria, which reports that Prof Sentetik, a manufacturer of big bags (FIBCs) from recycled polypropylene, based in Gaziantep, Turkey, is now employing its eqoCLEAN melt filter on a tape extrusion line to ensure the purity of the melt in the production of heavy-duty tape fabrics.
FIBCs – flexible intermediate bulk containers – are omnipresent in logistics as a lightweight and economical type of packaging for free-flowing bulk goods. Made predominantly from polypropylene (PP), they show a CO2 balance per 1,000 liters of transported goods that is far below that of rigid containers such as drums or octabins.
Prof Sentetik is making them even more sustainable by adding post-industrial and post-consumer PP waste in the production of various types of big bags. The company has recently installed Starlinger equipment for woven PP FIBC production, including the PP tape production line equipped with the eqoCLEAN filter system.
As a result, Prof Sentetik’s PP tapes for FIBC fabric with recycled polypropylene meet all the specifications required for heavy-duty packaging applications.
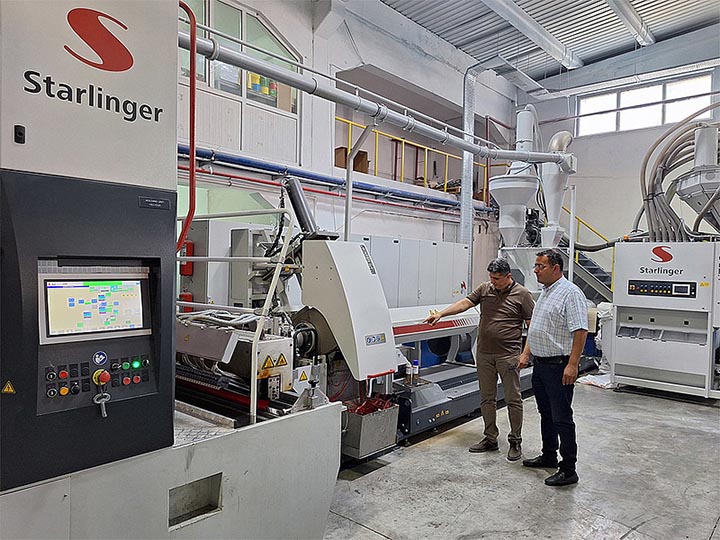
Waste Streams
The company currently processes in-house production waste and additionally buys recycled PP granulate from post-consumer plastic packaging waste. The share of recycled PP materials which can be processed depends on various factors such as which waste stream the material comes from or how it was handled during collection and storage.
Fine filtration tape extrusion during the recycling process is also crucial. Solid contaminants which can occur in post-consumer recycled materials, as well as foreign polymer particles in the melt – e.g., from polyester sewing yarn – compromise tape quality and cause problems in the tape production process.
The eqoCLEAN filter module developed by Starlinger takes into account all of the requirements for producing high-quality PP tapes with post-consumer recycled PP.
It consists of a SPB single-piston power-backflush filter, a melt pump, and a second HS 2.0 filter unit. The SPB filter has one piston and four cavities for filter screens. During the hydraulic power-backflush procedure the line operates at full production speed without interruption of the production process.
The regular automatic high-pressure backflushing procedure cleans the filter screens thoroughly, increasing their lifetime and reducing machine downtime significantly. The melt pump in combination with the additional HS 2.0 filter – which is positioned directly before the extrusion die – ensure stable production and high operational reliability.
“Plastic waste is a valuable resource, and instead of depositing it in landfills or incinerating it, it should be used in the best possible way,” says Fahri Sengül, general manager of Prof Sentetik. “The Starlinger tape extrusion line with the eqoCLEAN filter module ensures that the tapes we produce meet all specifications in respect of the tensile strength and elongation required for big bags in heavy-duty applications.”