Facemask materials, surface treatments, intelligent sensors & carbon nanotubes
That the COVID-19 pandemic has been a driver for filtration industry innovation is beyond dispute, and one of the commercial inventions of the year is undoubtedly the new bicomponent spunbond nonwoven material that can serve as an effective N95 facemask filter – without the need for the meltblown filtration layer.
This technology rightfully earned the Nonwovens Institute (NWI) at North Carolina State University the Innovation Award from INDA (publisher of International Filtration News) at its virtual 2020 RISE conference, held from September 30-October 1.
NWI executive director Benham Pourdeyhimi explained that the new media development arose from reactivated work on microfibrillation, which was initially undertaken for the filtration industry.
N95 efficiency can be achieved with just two layers of the new spunbond fabric. A combination of one spunbond layer and a meltblown layer can further achieve N99 efficiency.
The media also requires no electrostatic charging, which has been another bottleneck in the production of facemasks this year, and, because the materials are strong – unlike traditional meltblown materials – they can also be cut and sewn by traditional techniques. Further, they have the potential to be reused a number of times after cleaning.
In terms of productivity, spunbonding is also much faster than meltblowing. On the latest state-of-the-art Reifenhäuser Reicofil 5 lines, for example, throughput for spunbond fabrics is now up to 270 kg per meter of beam width, compared to 70 kg per meter width for meltblown.
At the beginning of November, Fortune 500 company HanesBrands announced that it had obtained FDA Emergency Use Authorization for a new surgical mask based on the NWI fabric.
“It is a testament to the ingenuity and collaboration of our university partners and our R&D team to quickly develop a much-needed mask that is high quality, affordable and comfortable for health care professionals,” said Mike Abbott, HanesBrands’ director of research and development.
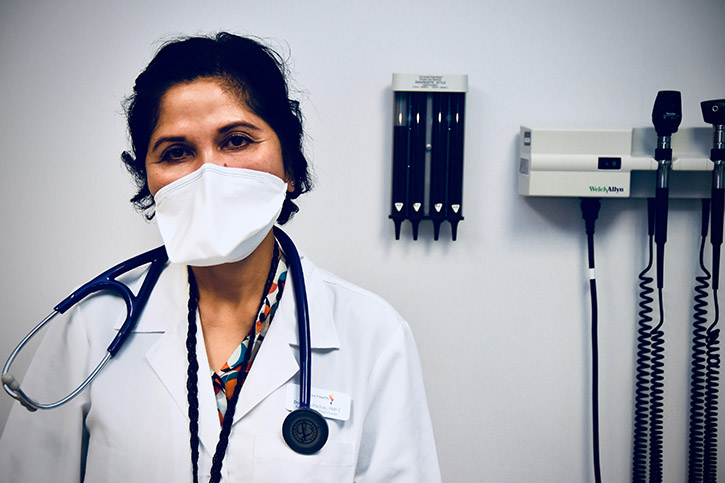
Livinguard
Around 56 million people in India are meanwhile said to be using the self-disinfecting treated filter materials of Livinguard, headquartered in Zug, Switzerland, for purifying their water.
A million Indian women who would otherwise resort to unhygienic and harmful alternatives in rural areas have been issued with Saafkins, reusable and affordable sanitary pads made from the material, as part of the GiveHer5 social initiative.
During the recent Innovate Textiles & Apparel (ITA) online textile machinery exhibition, which ran from October 15-30, Livinguard founder and CEO Sanjeev Swamy explained how this year Livinguard’s technology has also been found to destroy 99.9% of coronavirus in tests at both the Free University of Berlin, working in tandem with RWTH Aachen in Germany, and the University of Arizona in the U.S.
Inevitably, the technology is now being used in face masks, and Livinguard’s five-layer masks have been adopted by law enforcement and frontline workers around the world, with mask manufacturing currently taking place in China, India, Israel, Jordan, Portugal, Sri Lanka and UAE.
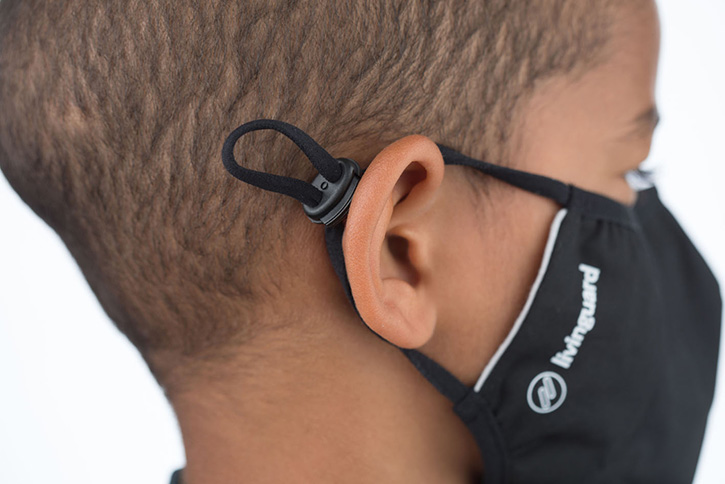
Positive charge
The principle underlying the Livinguard technology is to apply a positive charge at the molecular level to textile surfaces. When microbes come into contact with these positive charges, the microbial cell, which is negatively charged, is destroyed, leading to permanent destruction of the microorganism.
Unlike alternative metal-based solutions such as silver, zinc or copper that can be harmful to the environment and could cause health risks when used in a facemask, Livinguard technology has been found to be safe for both skin and lungs, and the technology destroys continuously, while allowing users to reuse the masks up to 210 times with no compromise on safety or efficacy.
“The chance of one virus passing through these masks is one in a billion,” said Swamy. “The technology works as a physical disruption of the virus cell membrane and is applicable not just for COVID-19, but also MRSA, hospital acquired infections and much more. Our first non-biocidal technology is also already developed because the world has to move to completely organic and biodegradable technologies in the next five years.”
Track and trace for masks
In another innovation, three Finnish companies – Suominen, Screentec and TrueMed – have come together to produce high-quality respirator facemasks with verifiable authenticity.
With no domestic facemask production at the time, Finland had difficulties sourcing high-quality masks at the beginning of the COVID-19 pandemic.
In an ultra-fast-tracked innovation process Suominen developed Fibrella Shield, a nonwoven suitable for use in the manufacturing of respirators.
At the same time, Screentec – a producer of medical electrodes and human-machine interfaces for demanding environments – started the production of facemasks at its Oulu works. After an exceptionally fast installation phase, the new production line was ready by late summer.
“A cooperation with Suominen was a natural starting point for us in seeking to establish a full domestic supply chain for high-quality face mask production,” said Screentec CEO Antti Tauriainen. “The plan is that in the future we will mainly use Suominen’s Fibrella Shield in our face masks.”
TrueMed has developed an AI and machine vision-based non-additive solution that is used to detect original and counterfeit medicines and medical products.
The aim of the cooperation between the three companies is to be able to confirm the authenticity of the masks and the nonwoven used in them – in this case, Fibrella Shield – to guarantee end-user safety. The cooperation also aims to produce important inventory information for the customer.
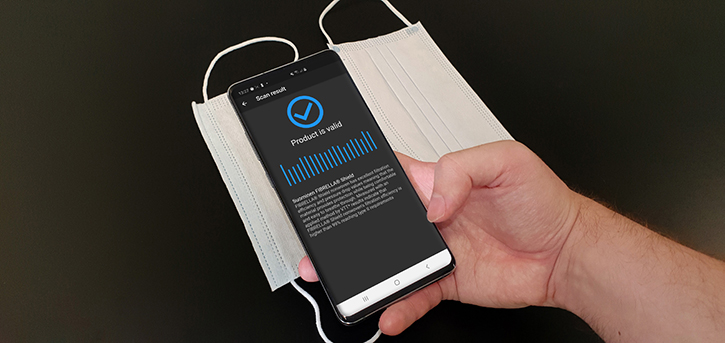
VOC sensing added to Myant Skiin products
Myant Inc., based in Toronto, has unveiled concept designs for connected facemasks that employ volatile organic compound (VOC) sensing, providing a new way to assess health and performance for the user.
The three patent-pending mask concepts will be commercialized later this year under the Skiin brand.
The connected mask concepts are modular by design, featuring an N95-level filtration layer positioned on top of a nose-bridge that separates airflow coming from the nose and the mouth, and a flexible silicon seal.
The components are held in place by a knitted textile cover that includes heated and electrostatic yarns that enhance protection against infectious agents, as well as temperature sensing yarns that enable the sensing of respiration rate. These yarns draw power through conductive yarns that connect to a module, which sends data via Bluetooth to a mobile device.
Sensing is enabled through the integrated sensors for VOCs, sweat and saliva, and carbon dioxide. The modular design also allows for rapid disassembly and cleaning via hand washing, the use of disinfecting sprays or autoclaving. Data captured by the mask is sent to the Myant Platform where, along with other data captured by garments powered by Skiin, it can be holistically assessed to generate meaningful insights to improve health and performance.
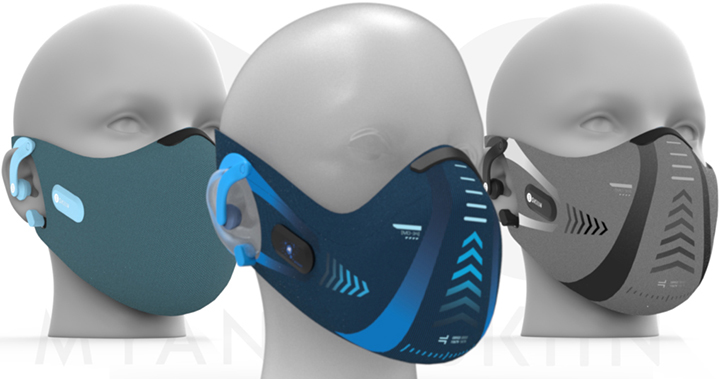
Oil refining
There have, however, been some R&D achievements in filtration fields away from PPE during 2020.
Scientists from ExxonMobil, the Georgia Institute of Technology, and Imperial College of London, for example, have developed a new membrane technology that could reduce the emissions and energy intensity associated with refining crude oil.
Laboratory tests indicate the patent-pending membrane could be used to replace some heat-intensive distillation processes at refineries in the years ahead.
“Inspired by reverse osmosis technology that has reduced energy intensity tenfold for water purification, we decided to look into ways to use new materials for liquids separation, which if brought to industrial scale, could significantly reduce associated greenhouse gas emissions,” said Vijay Swarup, vice president of research and development at ExxonMobil Research. “This is one of many new materials ExxonMobil is researching to reduce energy intensity and CO2 in our operations.”
The research successfully demonstrated that naphtha and kerosene – the primary components of gasoline and jet fuel – can be separated from light crude oil using pressure instead of heat, reducing emissions and energy consumption significantly compared to traditional, heat-based distillation methods.
The membrane technology employed is produced via an organic solvent nanofiltration process that is now widely used in the pharmaceuticals and chemicals industries.
Desalination
Researchers at Lawrence Livermore National Laboratory (LLNL) have created carbon nanotube (CNT) pores which – at just 0.8nm – are so efficient at removing salt from water that they are comparable to commercial desalination membranes.
As the dominant technology for removing salt from water, reverse osmosis uses thin-film composite (TFC) membranes to separate water from the ions present in saline feed streams, but some fundamental performance issues remain.
TFC membranes, however, are constrained by permeability-selectivity trade-offs and often have insufficient rejection of some ions and trace micropollutants, requiring additional purification stages that increase energy usage and cost.
Biological water channels, also known as aquaporins, provide a blueprint for the structures that could offer increased performance. They have an extremely narrow inner pore that squeezes water down to a single-file configuration that enables extremely high water permeability, with transport rates exceeding a billion water molecules per second through each pore.
“Carbon nanotubes represent some of the most promising scaffold structures for artificial water channels because of the low friction of water on their smooth inner surfaces, which mimic the biological water channels,” said LLNL chemist Alex Noy.