July/August 2014 | Volume 33, No. 4
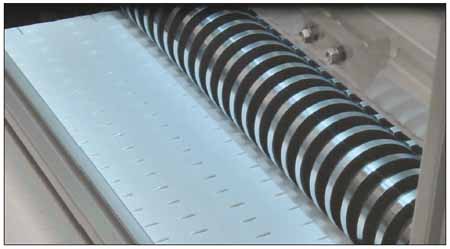
Environmental and regulatory requirements for indoor air quality have led to an increase in the requirement of air filtration products, which has lead to an increase in sales of air filters. One of the effects of the increase is the use of mini pleat pack filters to improve indoor air quality. Historically the mini pleat packs use glass fiber media, but due to regulatory and performance requirements, the use of synthetic materials is growing in this segment.
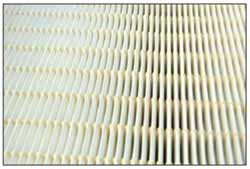
Working with filter manufacturers and understanding the needs of the filtration industry, three important needs were identified by A2Z engineers: the ability to pleat a variety of media, harnessing enhanced performance of the media and reduction in cost of production.
With these needs in mind, A2Z introduced the “Mini Pleat Blade Pleater” as a cost effective, fit to purpose production line, that allows for quick change over between synthetic and glass fiber media, with the ability to produce various hot melt bead patterns on mini pleat packs to optimize the filter performance and cost (Photo 1).
A2Z’S Intelligent Servo driven Blade Pleater along with the mini pleat production modules, allows the user to work with a variety of media including glass fiber as well as synthetic, with change overs for pleat depth/pleat pitch, and hot melt patterns on the fly (Photos 2 & 3). The operator can save and access up to 2,500 stored product variations, thus allowing multiple combinations/part numbers to be produced. The machine’s unique flexible design helps filter manufacturers widen their product range and meet the market’s ever changing needs.
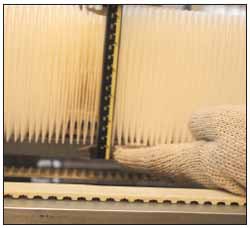
The A2Z Mini Pleat production module can be added to any existing blade pleater to produce mini pleat packs with a wide array of media thus further reducing the filter manufacturer’s capital expenditure and providing a very flexible production line. This also makes the equipment future-proof with the unique ability to mini pleat a very wide range of media.
A2Z continues to play a key role in the development of new products for the filtration market as a supplier of special purpose filter manufacturing and testing equipment.
A2Z Filtration Specialities is a designer and manufacturer of filter production lines, filter testing equipment and filter components with a client base in over 65 countries across six continents. The company has evolved from an equipment and components supplier to developing turnkey solutions in the field of filter manufacturing lines. The company has a dynamic work force comprising of over 50 engineering professionals offering installation, implementation and specialized training for filtration equipment, and complete turnkey projects around the globe.
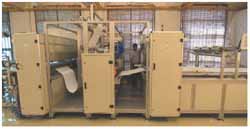
A2Z excels in providing superior value, and durable, globally serviceable product lines. Components are sourced from leading global suppliers to ensure ease of availability and trouble free maintenance. Features such as remote access for servicing and upgrading equipment software along with pictorial manuals make their products easy to use, efficient and great value for the money. A2Z’s customer base includes leading internationally recognized filter manufacturers.
In addition to the above-mentioned equipment, A2Z Filtration also provides filter-manufacturing lines for the following requirements:
- Cabin Filter Lines
- Air Filter Production Lines
- Blade Pleating Lines
- Rotary Pleating Lines
- Oil Filter Lines
- Coil Filter Lines
- Expanded Metal Lines