GHT5000F Domino Is Capable of Approximately Three Times the Throughput of the Largest Filter Press Currently in Operation
It’s been a busy few months for Diemme Filtration, part of the multinational Aqseptence Group.
In a pilot project with supplier Mann+Hummel, the automaker has developed a filter for electric cars that collects particulate matter from its surrounding area. Both while driving and charging, its aim is to help improve air quality in cities.
Just before Christmas, the company started up the world’s largest filter press for dry stacked tailings, the GHT5000F Domino – capable of approximately three times the throughput of the largest filter presses currently in operation – at the Toquepala copper mine in Peru.
In January of this year, Diemme subsequently began an expansion project at its plant in Lugo, Italy, to meet rising demand for its technology, especially in the field of metals mining.
Technology of Choice
Diemme was formed in the early 1970s at a time when the use of filter presses was expanding from traditional applications in the food industry to other industrial sectors as a process technology for the separation of solids and liquids.
Subsequently, the filter press has become the technology of choice for the treatment of industrial and municipal sewage sludge across the mining and chemical industries, power plants and the oil and gas sector, where high dewatering performance, low operational expense and reliability are key drivers.
In the mining industry, as a result of dwindling ore grades, metal extraction companies are now dealing with huge volumes which results in a significant waste slurry – known as ‘tailings’ – requiring material handling management on a challenging scale.
The full filtration and dry-stacking of tailings is becoming an increasingly popular management technology and requires equipment specifically designed to suit the scale of such mining operations.
Optimization
The Toquepala copper mine is operated by Southern Copper Corporation (SCC), a majority owned subsidiary of Grupo Mexico and received the first Diemme GHT5000F Domino press during summer 2022.
Parts of the frame were pre-assembled as modules in Italy, to reduce assembly time at the site, with quick-connect cables them minimizing wiring.
“The machine was rapidly assembled along with a tailings delivery conveyor at the site and after start up, a specialized Diemme team has been fully testing performance and optimizing the cycle to bring operation up to a steady level before production ramp up,” said Diemme’s head of R&D Davide Collini at the recent Filtech exhibition in Cologne.
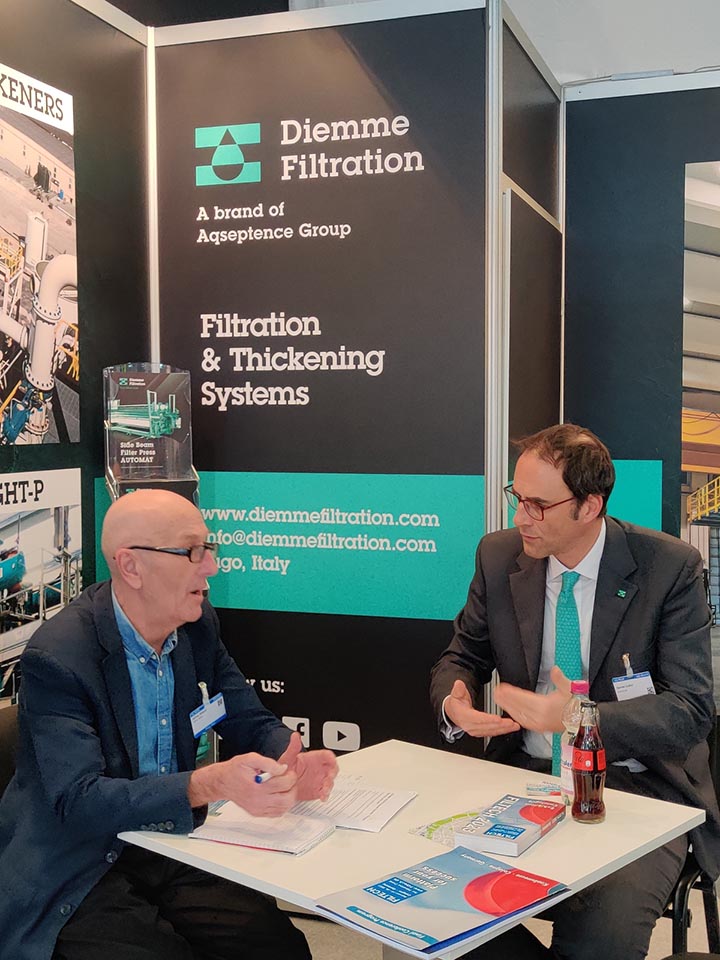
The Toquepala installation is a good example of the growth the company is experiencing across Latin
America, not just in copper projects in Chile and Peru, but also iron ore and bauxite operations in Brazil, where it now has a major new service and spare parts facility in Belo Horizonte, capital of the country’s Minas Gerais state. Similar facilities are being set up in other countries in Latin and South America, as well as in North America and Australia.
Heavy Duty
With a daily capacity of 8,000 tons, the GHT5000F Domino press machine at the Peru plant has a membrane plate size of five square meters and is equipped with a total of 141 of them, with heavy duty woven filter media at each side of the plates.
As a result, its maximum total filtration volume is 71 cubic meters, with a maximum total filtration area of 2,850 square meters.
The press carries out between 60-80 full cycles per day and benefits from an integrated work platform for easy maintenance. It also incorporates a new rinsing system with six points of washing for a homogeneous rinse of the filter media after each cycle, in addition to an automatic high-pressure fabric washing system with a double wash-bar to simultaneously clean the fabrics of two chambers and cut downtime in half.
Another innovation is a patented device for fully monitoring filter media and parts wear in order to schedule-in replacement times.
The GHT5000F Domino can significantly improve the capital cost of a tailings filtration plant compared with installing many smaller filter presses for the same operation.
Davide Collini
AIDA
“Not only is it the biggest filter press available, it’s also the most intelligent and benefits from our intensive R&D work on intelligent processing and complementary AI,” said Collini. “The Toquepala plant is equipped with our AIDA IIoT system for remote control, management and optimization. This means that while we can be close to our clients physically from our regional offices, we can also assist remotely and help them optimize their machines and troubleshoot any problems.”
Naturally, the Domino machine in Peru is creating a lot of interest from other mine operators in the region and a second is already being manufactured in Lugo for a copper mining customer in Chile, with delivery planned for the third quarter of 2023.
“The GHT5000F Domino can significantly improve the capital cost of a tailings filtration plant compared with installing many smaller filter presses for the same operation,” said Collini. “On a case-by-case basis, it is possible to evaluate the total cost of ownership. This is the Formula 1 of filtration technology.”
Meanwhile, work is continuing on the new plant in Lugo, which will allow Diemme to more effectively handle numerous challenging filtration projects which are currently in the pipeline. The plant will be equipped with the latest cranes, paint shop and other facilities to allow the company to produce the latest and largest models in its range highly efficiently, including the Domino. It will effectively double the company’s filter press production capacity and will also be energy efficient, powered by an extensive array of solar panels.
The plant is on schedule to be completed by mid-2023.