Bio-based Considerations for Filtration are Making Their Mark on Sustainability All Along the Supply Chain and Product Offerings
Plants not only help in providing natural filtration to the air we breathe, they also are now considered in all aspects of consumer choice as a desired ingredient, as the world strives to make healthier and sustainable choices. Everywhere you turn, “plant-based” marketing sells products. In the materials world, the use of living organism biomass is gaining traction to indicate a carbon-neutral eco-friendly product solution. With environmental, social and governance (ESG) strategies increasingly linked to corporate profitability, there is incentive to provide options consumers and corporations can feel good about.
It seems a steep climb to achieve any sort of fully sustainable filter media options to satisfy appetites for better options. Reimagining the production process for eco-friendly alternatives is not easy, cheap or quick. Yet – it can be done. International Filtration News caught up with three companies who are providing eco-friendly solutions to respond to the demand for health, wellness, and sustainability in filtration. Here is what they have to say about their work.
Roswell Textiles core value is a commitment to support health, wellness and quality of life, while being eco-conscious and reducing environmental impacts. Their new ECOFUSE™ materials are the nonwoven textile solution to meet this mandate of using plant-based materials that can be composted and allow for substantial reduction in carbon emissions. It is manufactured from biopolymers, intended to replace conventional high carbon footprint synthetic plastics.
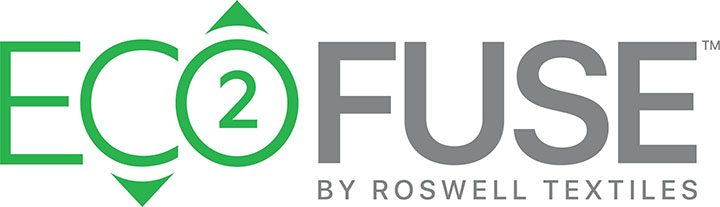
Formed in 2020, Roswell Textiles developed, commercialized, and scaled Canada’s first domestic supply of synthetic meltblown during the COVID-19 pandemic in response to a call to action from the Canadian Federal Government. At that time, the pandemic made it obvious for the need to create a supply of Canadian-produced melt blown filter media for PPE manufacturing, non-existent in the country. To pursue this, the company received some funding from the National Research Council Canada (NRC) for their efforts.
The Journey
Then known as Roswell Downhole Technologies – a manufacturer of tubing encapsulated cable for downhole sensor systems for oil and gas – the new Roswell Textiles transitioned away from that sector and put their expertise in manufacturing and machinery to work to develop sustainable materials for melt blown media. The team of mechanical engineers were able to move quickly from concept to application, scaling production quickly and efficiently by engineering and manufacturing its own nonwoven production equipment in-house and making its first commercial sale of Canadian produced melt blown material in just two months.
Roswell Textiles’ President Kyle Fiolka says, “We’re a smaller producer. We are focused on technology innovation and more niche, higher performing areas. Filtration is obviously very challenging, especially in the PPE space when you’re dealing with low DPs and medically certified devices. We have partnered with the PADM Group of Companies in Winnipeg to move it forward faster by providing converter capabilities, and they are now our parent company and strategic partner.”
Roswell Textiles has now positioned itself as an innovative nonwoven manufacturer and OEM of biopolymer nonwoven equipment. They recently announced the next generation of high performance and technical nonwoven materials under the brand name of ECOFUSE™. These highly engineered materials possess similar technical specifications as synthetic, polypropylene materials but with a 65% net carbon reduction. As a result of their plant-based start of life, they contribute to a more sustainable and circular economy.
Product Expansion
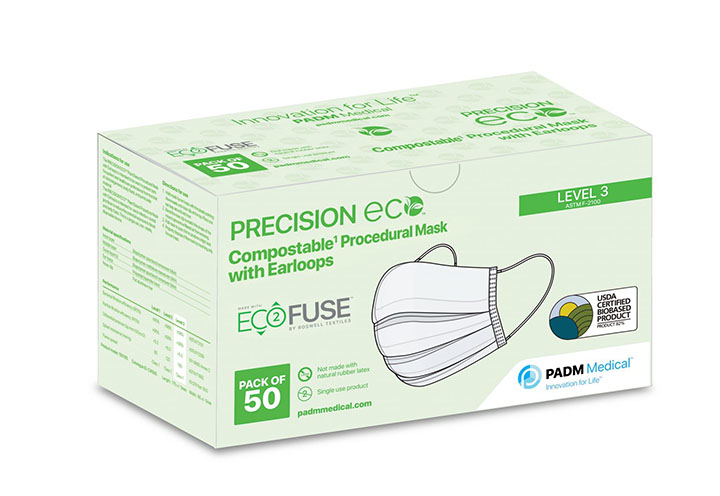
ECOFUSE™ materials are already commercial in medical, water and residential filtration applications with additional commercialization processes underway in hygiene, food and beverage packaging and construction materials.
“We’ve been working through the certifications of our PPE device (ECOFUSE™ is 82% of the raw material in PADM Medical’s PRECISION ECO™ procedural mask) and our big news is that as of March 8th, we received an FDA 510(k) Clearance on the product,” says Fiolka. (Kyle also serves as PADM Group’s Chief Innovation Officer). “That is extremely difficult. To our knowledge, we are the first PPE that the FDA has approved as a non-synthetic based procedural mask, so it is a big achievement.” The ECOFUSE™ biopolymer material is also a USDA Certified Biobased Product (100%) and tested to conform with ASTM D6400 and ASTM F2100 for finished product certification.
The Bio-Story
ECOFUSE™ is derived from crop feedstocks which offer a carbon footprint reduction when compared to hydrocarbon derived polymers. The product breaks down at end of life in an industrial composting process. “The feedstock used in ECOFUSE™ technology are regionally specific. Crops like corn, sugar cane, sugar beets are used to produce the biopolymers” says Fiolka. “Since we developed the proprietary machinery and process conditions to suit, it is a modified nonwoven process.”
The product does not leave residuals or toxins in the soil as it decomposes. “We validate that with life cycle analysis,” says Fiolka. “We also encourage our clients to know the total impact of their finished product to the end of life. Even in incineration, biobased materials have a better footprint when it comes to emissions compared to polypropylene, for example. Users of ECOFUSE™ can pursue an ISO accreditation or apply for carbon offset or carbon credit programs. We’re familiar with analyzing materials in that way because it’s how we’ve ensured that we’re doing something that’s truly better from an environmental impact perspective.”
The company’s focus is on commercializing biopolymer and low carbon footprint materials that can replace conventional nonwovens for use in filtration applications and other industrial products. “We have a vision of leading mass adoption of plant-derived nonwovens to help the world transition to more sustainable products. We feel that ECOFUSE™ can help drive this adoption by breaking down technical barriers for regulated products requiring high performance filtration properties. We came at this challenge from purely an engineering and theoretical perspective, and maybe that’s why we were able to do what we did. We didn’t have limitations in the possibilities and outcomes,” says Fiolka.
The challenges to overcome in PPE development included using nonconventional materials to produce microfibers that can effectively filter particles while maintaining high breathability. Also, the requirement to have a suitable shelf life for the product was critical. The requirement to provide a fluid jet barrier for the product had to be overcome to achieve the appropriate ASTM performance, as well.
Current applications for ECOFUSE™ are procedural/surgical masks and respirators, industrial and commercial air handling filters, and liquid filtration (water).
“In hindsight, we began in a very challenging nonwoven sector, looking at it from a regulatory perspective,” says Fiolka. “Yet, we were able to achieve success, so now other commercial applications are much simpler to adopt. We are receiving more inquiries for different applications. As equipment manufacturers, we have the ability and advantage to work with clients and deliver complete solutions at scale quickly and economically.” Innovations like ECOFUSE™ help close technological gaps to allow consumers and producers the option to choose sustainable materials.
Avgol Nonwovens has been in the Spunlaid fabric market since the 1980s, then joining the Indorama Ventures family of companies in 2018.
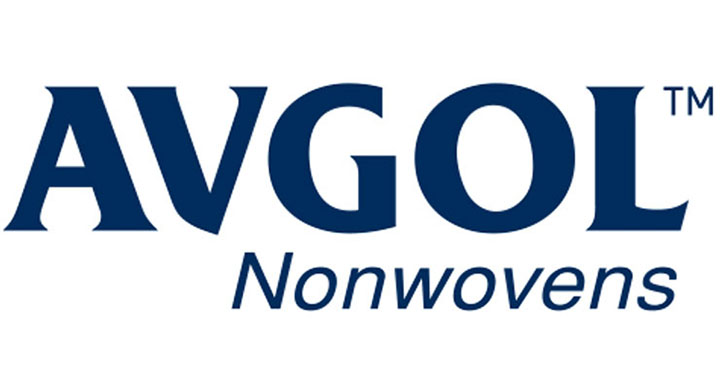
“Our focus had been on the hygiene market, supplying many of the components used in baby care, menstruation management, and incontinence markets,” says Nick Carter, Vice President, Marketing. “The COVID pandemic was a catalytic moment in company history, as we were approached by non-hygiene industries to bring large volumes of high-quality products to other markets, including filtration. COVID also seems to be a catalytic moment in the filtration industry, as consumer concerns over healthy, purified indoor environments became a priority.”
Whether for automotive, public transportation, home or office/work environments, the consumer became much more interested in “upping their game” by spending more for higher qualities of filtration. Avgol Nonwovens has found that many of the product performance triggers for hygiene and filtration overlap, when designed to selectively separate or filter a “contaminant.” Since, Avgol has brought a product portfolio of technologies to the filtration market and will continue to develop new products in this area.
Seaweed Is Believing
Jumping into a plant-based solution came as a collaboration, working closely with Algaeing™ – a small company that has worked to produce non-toxic, biodegradable, and natural fibers and dyes for textile using algae since 2016. “The Algaeing™ team helped to create conceptual products that advance the sustainability factor of our portfolios,” says Carter. These sample products illustrate how Algaeing™ colorants can be used in various fiber applications, like coloration of PPE and thread. Avgol Nonwovens showcased them at the FILTECH show in Germany.
“This technology is applicable as both topical and integral color in our component materials. As one would imagine, thermal stability, color stability, and odor can be a challenge when using bio-sourced components. Very interesting solutions have been, and continue to be, identified as we continue to mesh technologies like Algaeing™ with our spunlaid technologies capabilities,” he says.
The use of bio-colorants is one of many solutions in Avgol’s overarching strategy of creating biodegradable and recycle materials for use in various applications. They are looking for performance modifiers that are readily separated through advanced or chemical recycling means, while also supporting release back into the environment when the “encapsulating” or “framework” polymer structure is removed through biodegradation. “Avoiding SOI’s and SIN listed chemistries is critical as we have to adjust our perspective of what was once safely sequestered away in the media now has the potential to be released much more quickly in a different form to the environment,” notes Carter.
These new sustainable technologies have a higher cost today and are quite often impacted by economy scale. Yet, that is where doing the best thing, not the most economical, comes into consideration for companies who want to be eco-friendly. “For Avgol, to consider using a compound that is known to be harmful if released in higher-than-normal concentrations through aggressive biodegradation is simply not a viable path to be taken in the design process,” affirms Carter.
Testing the Marketplace
As a provider to the nonwoven product production process, Avgol’s component materials are wound, spooled and/or laminated together by the manufacturers as part of the subsequent article of sale. Their manufacturing partners have helped them test their product for quality and performance. “We test the materials through a combination of nonwoven performance protocols, such as ISO standards and well-known cytotoxicity/skin contact methods, combined with specialized in-house testing and, where applicable, testing protocols defined by our customers to meet any unique aspects of the specification. The end-use performance is then confirmed by the manufacturer of the complete article.”
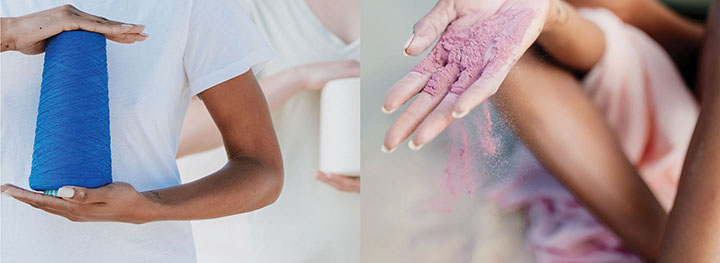
Specifically for the algae-based colorants, Avgol is evaluating the application where aesthetic enhancements are desired, including when there is a desire for uniform coloration as well as a rather unique heathering effect that they can produce. For now, the face mask facing layers, semi-durable bags/packaging and various components of absorbent hygiene products are some of the most immediate applications.
The most significant consumer benefit is the wellness-factor for the user when utilizing bio-based solutions. “When we consider that the algae-based colorants also exhibit skin wellness characteristics, anytime a fabric may be in prolonged contact with the user is also a potential value for aspects of the market,” emphasizes Carter.
Plant-Based Solutions Must Start Somewhere
“The value of multiple plant-based product lines extends from the resins we begin with to the performance and aesthetic modifiers we use in producing the final component materials. This is an important aspect of not only Avgol’s positioning, but truly is an aspect that should extend through the filtration industry. We are committed to enhancing the sustainability factor in our offerings” says Carter.
Bringing a fully bio-degradable solution may not be achievable at this time, it all starts somewhere, even with sustainable coloration that won’t hurt the environment in degradation. “We have various ways and means to achieve enhanced sustainability; it is not a ‘silver bullet’ solution or a magical-cure-all that I doubt any one company will bring forth,” says Carter. “Rather, the ‘best solution’ will most likely come through the collaboration of every link in the supply chain. I would not be at all surprised that the end-of-life situation of what to do with used filters will ultimately result in a ripple all the way back through the chain where input from resin producer to convertor to manufacturer to recycler will contribute insight and overall advancement in the future that we can only guess at today.”
“I see many parallels between the hygiene and filtration markets, as grander trends will be seen in both industries. For example, products that have more reusable content and less disposable content, such as HVAC filter designs that have increased proportion of reusable filter frames and supports, with a corresponding lower use of the filtration media itself, wherein that filtration media is bought off bulk rolls at home improvement stores. We can see the same in the form of reusable diaper chassis that have just the pad area replaced instead of the entire diaper. Migration away from fossil fuel derived components in the nonwoven media is a given, whether it be the resin itself or the modifiers used, and I only included it here for the sake of completeness,” Carter speculates.
Sustainability, regardless of how it is defined, is becoming more of a qualifier and less of a winner when it comes to being selected by the end consumer. If one does not actively participate now and work across the industry, it will be left to only react in the future.
Filter Factor for Plant-Based Beverages
The global demand for plant-based food and beverages is exploding. For the consumer, product decisions are based on texture, taste and mouthfeel. For manufacturers, it hinges on starting with the right base. SPX FLOW, Inc., is upping the quality factor for plant-based beverage manufacturers with its new technology for plant-based concentration using APV membrane filtration. This innovation provides clean label products of higher nutritional value. Benefits include a greater yield, higher single-source protein content and a more sustainable process compared to traditional methods using evaporation and chemicals. The end result is a win-win: a cleaner, better product for the customer, and a more sustainable, versatile and higher-yielding result for producers.

SPX FLOW, a process solution provider for the industrial, nutrition and health markets for over a decade, developed the APV membrane filtration technology. The solutions, designed based on processing needs, include process filtration like microfiltration and ultrafiltration for fractionation, concentration, and standardization of plant protein. Additionally, nanofiltration and reverse osmosis systems are available for solids concentration, valorization of subproduct, and water recovery.
“Our history of supporting membrane filtration solutions for the industry comes from our decades-long record with the dairy industry,” says Allan Vangsgaard, Global Product Manager for Nutrition & Health. “More recently, we’ve seen the movement and increase in plant-based products. Keeping in line with our efforts for constant innovation, our team has worked to develop our knowledge and expertise in the plant-based sector. That’s where this new development for membrane technology has come from — our vast work for improvement and optimization to benefit our customers.”
The basics of the technology itself stem from membrane filtration techniques used in dairy and translate well for a wide range of solutions designed to fit various plant sources, including soy, oat, nut, rice, pea and more that are used in plant-based beverages. “Every dairy plant is different, so we’ve grown accustomed to working with customers to develop a tailored processing system that fits their needs based on their unique situation,” says Vangsgaard.
Plant-based processing has similar challenges due to the highly variable raw products and the various end-product demands. The big challenge is there are so many content variables that need to be understood, from process flow, protein and fiber content, product temperature and much more. Many moving parts come together, and one must understand each area, from pumps to valves to filters, to create the right end-product.
“That’s where this technology comes into play — the components aren’t new per se, but how we use and implement them is new and innovative,” says Vangsgaard. “I like to think of it as if it’s like an orchestra. All the musicians and instruments work together to produce a singular song. The conductor understands the timing and elements needed to meld together seamlessly. Our experts are the conductors when it comes to designing end-to-end solutions for processing equipment.”
Higher Protein-Producing Technology
“It comes down to the setup and the process of the system overall,” says Vangsgaard explaining how it all works. “There are different particles and variables in plant-based sources than there are in milk. The protein content in nuts, grains and legumes varies much more than in milk. This changes the process, such as flow rate, membrane type, pressure, cycle loops and more. Compared to traditional plant-based concentration, which involves chemicals or evaporation, there’s no need for additives with the membrane filtration process. By using a membrane instead, processors can stick with a single-source ingredient filtered to a higher concentration of nutrients.”
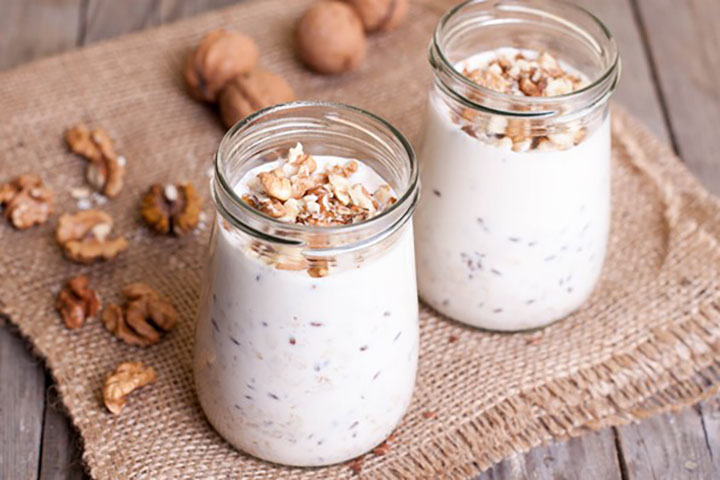
SPX FLOW has state-of-the-art, collaborative Innovation Centers throughout the world to work with customers to test, develop and perfect their critical manufacturing processes. The Silkeborg Innovation Facility in Denmark has a complete membrane filtration setup to test all parameters for nuts, grains and legumes, such as flow, temperature, concentration, etc., and document how they impact the entire process. These tests provide a holistic view of the quality and result, and of the equipment and process itself.
“We continue to add new sources as the markets develop to support our customers so they can stay innovative,” says Vangsgaard. “It’s a benefit to not only emerging producers in the market but those established companies looking to innovate their existing products, as well. Plant-based processors have faced a challenge – their products are usually lower in protein compared to dairy, and this solution can help with that, as it improves the nutritional value for the consumers.”
Specializing in end-to-end solutions, from design to operations to maintenance, SPX FLOW fully understands the components and systems for processing plants, but also all the parameters to make successful products. “As we see more and more of our customers entering the plant-based sector,” notes Vangsgaard, “we are working with them to help position them as leaders in the field whenever possible.”