In an effort to evaluate the salient points of the metalworking industry, the hope is that the potential for biodegradable products can be seen by the manufacturers of filter media. In order to assist companies to measure the potential, we will dive into and define the various aspects of the metalworking industry. At least it will hopefully serve as a guide for those companies who sell disposable nonwovens and aid in understanding the need for a transition to biodegradable fabrics. The transition will come because there is growing pressure for metalworking companies to move away from synthetic fabrics. Each major applicable point is outlined with the specific terminology to give an idea where the potential is within a plant.
Applications
Metalworking applications can be determined by operation.
- Machining of all types, including drilling, and reaming.
- Grinding: rough, intermediate, fine. Honing, polishing, surface finishing.
- Wire drawing: rod, intermediate, and fine. Rod rolling, continuous casting. Rolling mills roughing, tandem, and finishing, Continuous casting, extruding, forging, and shaping.
- Other metal working functions: quenching, heat treating, parts washing.
Fluids
The applications may use one of the following fluids:
- Plain water
- Water-base coolants at varying degrees of stability
- Straight oils with viscosities ranging from 30 SSU to 200 SSU
- Some installations may use a heavier oils up to 1000 SSU
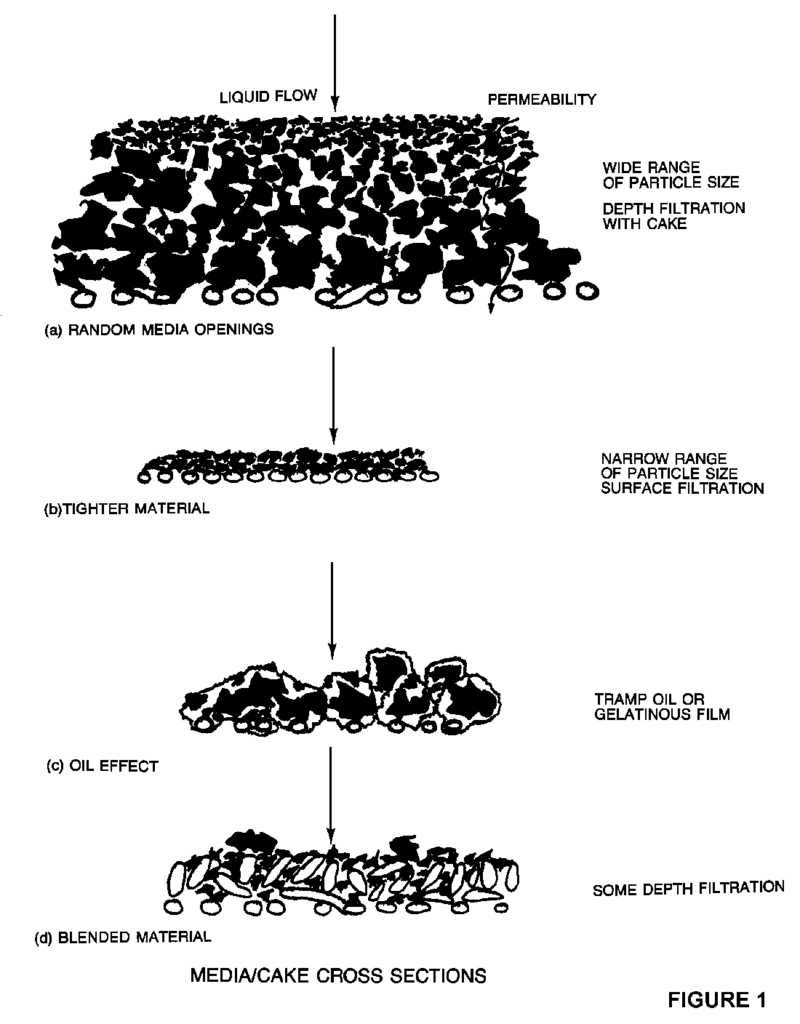
Filters
These applications use many type of filters (bags, cartridge, and sheets), but the design which has the largest potential are the flatbed open chamber filters with the driving force generated by either gravity, pressure or vacuum. These use roll media in widths ranging from 24 to 96 inches wide. The most popular is 51-inch wide fabrics.
Media
The fabrics used for disposable nonwoven media are:
- Polyester
- Polypropylene
- Cellulose
- Nylon
- Combinations of fabric in layers or embedded
Fabrics are manufactured with many processes. Terms such as spunbonded, pointbonded, melt blown, and lofted are just a few techniques. Each technique offers some characteristics which contribute to the performance of the media on a filter.
The weight of the fabrics ranges from 0.5 to 3.0 ounces per yard. Air permeability ranges from 25 to 900 CFM. Some applications may use media with higher air permeability ratings.
Wet strength is an important parameter since the media has to survive the rigors of going through the bed of the filter. Some filters carry the media on a carrier belt, so the media does not have to be as strong as when the filter’s design requires the media to be either pulled or pushed through the filter’s chamber. Other parameters of media, such as tensile strength, percent elongation, and mullen burst, should be checked.
Micron rating is a minor factor and there is a different reason to rate the fabric by microns for flatbed filter applications. The main reason is that most installations generate the solids as they operate. The solids form a cake on the fabric and the cake, itself, becomes the cleaning medium. The fabric usually serves as a “septum” (media support). Micron rating look at the largest particle instead of the smallest particle. This is different from the typical selection process of a cartridge filter.
Existing Problems Create the Potential for Biodegradable Media
The following are specific concerns:
Landfill – Disposal restrictions for landfill use are getting tighter. Waste dump areas do not want plant waste dumped with the solids intermingled with spent rolls of media.
It often is referred to as “old toilet paper.” It is awkward to handle and bury. Plus it does not decompose and adds to the waste volume.
Many filter companies add a spent media winder on a new filter or have an add-on unit to be retrofitted to an existing filter. The rewinder would wrap the spent media around a throw-away arbor. It yields a tight roll which is easier to handle. It still is messy, and any liquid squeezed out of the media is collected separately in a drip pan below the rewinder. A doctor blade is needed to scrape the cake before rewinding. Otherwise the roll would not wind evenly and be much more awkward to handle. The solids are dropped into a separate container.
Extra Cost – The extra handling to prepare the solids for waste disposal become a major expense item.
Permanent Media (reusable) – Many operators try to add reusable media to a filter designed for disposable media. There are basic problems:
- The application does not allow for self-cleaning of the reusable media with the same fluid it is filtering.
- The media slowly becomes blinded, and the reduction of effective filter area jeopardizes the clarity of the fluid.
- The cost becomes prohibited because the replacement of the reusable belt and labor become large maintenance items.
Biodegradable media should eliminate most of the problems. The goal is that it can filter the fluid and once it is discharged in the waste container, it will breakdown to a pulpable material which can be handled along with the solids.