Nonwovens are commonly used as filtration media. Nonwoven filter media is an engineered fabric comprised of a random arrangement of filaments or fibers. The media has the specific function of filtering or separating components of a fluid (air/gas or liquid) or to act in combination as a prefilter or support for other materials in the filtration and separation process. There are a broad array of other filter medias and modes of filtration; nonwovens are, by no means, the only materials utilized for filtration. Alternative materials include granular beds, strings, screens, membranes and other porous structures. Filtration medias are almost as comprehensive as the applications they serve.
Variability in nonwoven filter media
Classifying variables in nonwoven filtration media can be somewhat contentious. “Standard filtration” is a misnomer as there are many different variables associated with such a broad set of uses and nonwoven forms. As an example, a meltblown filter media is well suited for high-efficiency air filtration, but it can also be utilized as a prefilter in liquid applications. Meanwhile, a similar weight of spunbond filter media is significantly less efficient than meltblown in air and liquids, but it offers more strength and durability, assuming similar polymers are employed. Needle felt filter medias, of similar polymers, would be much thicker and stronger than both meltblown and spunbond nonwoven filter medias. While these three examples are based off of a single polymer fiber, their form and function would be significantly different and would not easily be substituted between applications and yield the same results.
Applications
From an application perspective, nonwoven materials are well suited in many areas of filtration. Overarching nonwovens are particularly suited to applications involving low pressures, and they are particularly strong in the microfiltration spectrum of particle separation. More broadly, nonwovens can also be deployed in a broad range of temperatures and chemistries.
Alignment of core circularity principles in the filtration industry will also drive recycled content – either through biological or technical cycles after use. Investments in innovative and scalable technologies that support the circular transition are happening now.
There are also many applications where nonwovens are challenged to provide the level of performance required. High-pressure applications generally utilize other porous materials, such as metal or ceramics. Course particle filter medias often utilize more open structures like netting, mesh and even sand. While there can be some overlap, generally nonwovens are best suited for microfiltration particle separation in the range 0.1-10 μm.
Nonwoven filter media treatments
Filtration medias can have several treatments that can change the filtration performance of the media. One common treatment is filter media charging, which attracts oppositely charged particles. This enhancement generally improves collection efficiency of smaller particles. This type of filter media will decline and discharge during loading and the filter media will revert to mechanical filtration.
Other treatments include hydrophilic and hydrophobic treatments. Hydrophilic filter media is easily wet with water and due to the difference in surface tension, oil can quickly pass through the filter media layer. The water in this treatment moves much slower and is adsorbed on the surface of the filter media, causing the water droplets to coalesce. Hydrophobic treatment, on the other hand, can facilitate dust cake release and promote longer life of the filter media in applications where such functionality is appropriate.
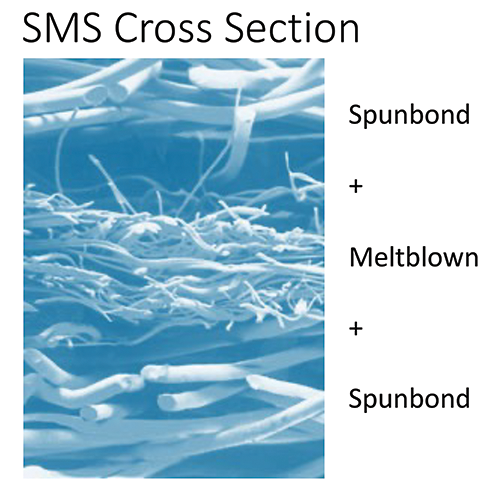
Technology innovations
There are many innovations in polymers, and these are magnified when they are converted into nanofibers and added to nonwoven filter media. Nanofiber technologies can dramatically enhance filtration efficiency and can be employed, for example, to selectively remove gas molecules or specific biomolecules and macromolecule proteins to provide high purity in filtration applications where this effect may be required.
Bonus ’Tech Talk’ Video
Learn More @ inda.org/education!
The future
Looking 5-10 years into the future, nonwoven filter media will certainly continue to evolve. The potential for engineering the raw materials, the building blocks of the structure, will continue to enhance efficiency and lower pressure drop in filter medias. Alignment of core circularity principles in the filtration industry will also drive recycled content – either through biological or technical cycles after use. Investments in innovative and scalable technologies that support the circular transition are happening now. Their strategies are clear – development of innovations that integrate and compete with conventional materials both in terms of cost and quality and provide positive sustainability impacts across the entire nonwovens value chain.
As director of education and technical affairs, Chris presents regular training related to nonwovens and filter media from INDA’s headquarters in Cary, NC. For more information about upcoming training opportunities, visit inda.org/education.
International Filtration News is owned by INDA, Association of the Nonwoven Fabrics Industry (inda.org).