May/June 2014 | Volume 33, No. 3
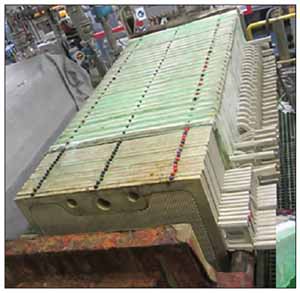
Sometimes it’s worth looking beyond existing, established processes, visible at the example of Lenzing Technik GmbH, an internationally operating engineering company with headquarters in Salzkammergut, Austria.
As a subsidiary of the Lenzing AG the market leader in the production of cellulosic fibers with wood as a raw material the Lenzing Technik GmbH has been focusing on the value chain from cellulose to the finished viscose fiber. The company’s portfolio ranges from engineering services to development and manufacturing of processing equipment as well as turnkey facilities. Even whole viscose production plants have been engineered and built.
A small team of experts at the Solid-Liquid Separation Division of Lenzing Technik has been engaged in the filtration of viscose, a homogenous, but contaminated high-viscosity fluid with honey-like appearance. Until the first filtration systems with automatic sludge discharge were developed, viscose was filtered with filter presses. In a typical viscose plant up to 100 such presses were installed, frequently taking up several thousand square meters of filter area.
The filter presses were equipped with filter cloths made of cotton, needle felt or pulp sheets. Filtration was usually targeted at a fineness of 20m. Similar to bag filters, which are still in use for smaller filtration tasks; the cloths were perfused by viscose. After their dirt holding capacity had been reached, they needed to be removed manually and replaced with new cloths.
The first automatic systems were introduced in the 1970s, but did not reach market penetration. Especially worth mentioning are horizontal disc filters, which use filter aid to build/precoat a cake on a package of horizontally placed, round filter plates. After finishing the filtration cycle, the disc package was put into rotation and thereby discharged the filter cake. Although still in operation in the beverage industry, this system could not establish itself widely for several reasons such as the high complexity and costs for apparatus and installation, the discontinuous filtration as well as filter aids consumption and its regeneration.
At about the same time, the first backwash filters (mainly using metal fiber fleece as filter media) were introduced to the market. Generally considered a suitable technology, the first systems failed due to several significant disadvantages. Some used extremely complex and expensive filter elements, which needed periodic thermic regeneration, as they were not efficiently back washable. Other unfavorable ones needed up to 20% of the filtrate flow to clean the filter from impurities (referred to as “reject”). Hence, further complex filtration facilities for processing of the reject were necessary.
The development of the “Kolben-Korb-Filter” (KKF) filter by Lenzing Technik GmbH allowed inexpensive, automated filtration of high amounts of viscose at a fineness of 20m and minimum backwash quantities. The “Kolben-Korb Filter” has been a market leader in the global viscose industry ever since, and soon achieved success in other fiber-producing industries as well.
In viscose filtration several requirements need to be strictly met, which are also reflected in sugar processing.
RELIABILITY
Perhaps more in viscose plants than in sugar processing, the reliability of apparatuses is essential.
If the production process of viscose as a fluid is interrupted for several hours, it hardens and coagulation takes place. Devices and tanks that are filled with coagulated viscose need to be cleaned in a miner’s fashion, as there is no way to dissolve coagulated viscose.
A similar thing happens in sugar processing where unintended crystallization of sugar at least involves efforts for re-starting the production process. Due to the timely limited manufacturing cycles, additional production downtimes are especially critical. Furthermore, the continuous downstream process of evaporation, crystallization and separation should not be discontinued due to a still stand in the filtration step.
LOWEST REJECT QUANTITIES
Not only in viscose production, but also in sugar manufacturing, the fluid (thick juice or standard liquor) represents the valuable substance. Minimum losses (=”reject” amounts) were the key success factors of the “Kolben-Korb-filter” in the viscose industry.
FILTER FINENESS
Being considered a spinning solution, viscose is pressed through extremely small holes of the so-called “spinning jets” (usually at a fineness of approx. 50m) after filtration. Downstream from the spinneret there is a chemical precipitation bath leading to a coagulation of the viscose fiber, which is then drawn through the spinning bath by peeling rolls and frequently drawn down to a fiber diameter of only 20m.
In sugar processing, an efficient filtration has positive effects on the downstream vaporization process as well as helping to improve product quality of refined sugar. Details on the reached filter fineness in thick juice and standard liquor are described in the course of this report.
EFFICIENT BACKWASH
A good viscose/sugar filter runs continuously, while filtration is not interrupted during the backwash procedure.
It is not uncommon, that 100,000 backwashes and more can be executed, before the filter material needs to be changed for the first time.
The increased viscosity of thick juice and standard-liquor, which forced other systems to backwash with external media, did not represent a challenge for the engineers of Lenzing Technik. Quite contrary to this, the KKF filter concept even needed to be adapted to the lower viscosity of the sugar solution. The result of this adaption is meanwhile patented and established in a variety of different applications and processes under the name “Lenzing OptiFil├é┬«.”
LOW OPERATING COSTS
Both, viscose (apart from specialty types) and sugar have become mass-produced goods. In today’s globalized markets, cost leadership also defines the market position of a company applying not only to investment but also especially to operating expenses.
Mostly, the investment costs for the integration of processing plants are multiplied by the costs for installation (e.g., set-up, control system, piping, valves, installation area, etc.). In this respect, the OptiFil has the advantage of an easy system construction with only one automatic valve per filter. While the filter is able to manage relatively high flow rates, it does not require more installation area than a parking motor scooter.
The patented Lenzing OptiFil is a fully automatic, continuous system that works according to the principle of depth, surface or cake filtration, depending on the selected type of filter material. A metal or synthetic fiber fabric or fleece (see Figures 2 and 3) is used as filter media, retaining particles of different sizes either inside or on its surface.
After the pre-determined degree of contamination has been reached, the filter material is cleaned by backwashing a small quantity of filtered medium, with continuous filtration during backwashing.
In detail, the filter material of the Lenzing OptiFil is installed outside a perforated supporting structure (“perforated drum”). In case of cake filtration, a very thin filter cake (of typically 0.5 2mm) is formed inside the holes of the perforated drum during the filtration from the inside (Room P1) to the outside (Room P2). During the partial backwash from “Room P2” (Filtrate) to “Room P3” (Reject), the cake is completely discharged within a few seconds, using a small amount of filtrate to force it out of the filter. New cake formation already starts during backwash and is typically finished resulting in clear filtrate within less than 10 seconds.
TRADITIONAL FILTRATION METHODS
To date, two different systems for filtration of Standard Liquor have been in use in the sugar manufacturing process, where both, candle precoat filters as well as disposable bag filter elements show significant disadvantages in comparison to the Lenzing OptiFil.
CANDLE PRECOAT FILTRATION
In order to achieve an economic flow rate, the candle precoat filters have to be operated with precoat (= first conditioning of the filter material with a thin layer of filter aid) as well as body-feed (= continuous dosing of filter aid). This required a consumption of 15 kg high quality filter aid per hour in the specific process. As a result, tremendous operating costs as well as significant expenses for handling and logistics incurred.
At a specific flow rate of only 2,9 m³/m²*h, an enormous filter area was needed to handle the total flow rate. So the 8 required candle precoat filters (each taking up 125 m²) caused considerable investment costs as well as a huge space requirement.
CLEANING BY ROTATING NOZZLES
Backwash filters with rotating nozzle cleaning systems were installed in several cases of thick juice filtration. These types of filter systems have been developed in Israel, originally intended for separation of coarse particles from water in agricultural irrigation. Due to their construction design, which is known to have a gap between the backwash nozzles and the sieve basket, they were not able to handle backwashing of the high viscosity thick juice and therefore needed to add external medium (thin juice or water) to execute the backwash. This, in turn, led to an increased number of valves and pipework. Furthermore, the equal space between the different nozzles resulted in high losses during backwash. As a countermeasure, the filters are equipped with very coarse (50m) sieve baskets. These indeed reach large intervals between the backwashes, but operate at the expense of filtrate quality.
DISPOSABLE BAG FILTRATION
A seemingly feasible process, because a non-expensive alternative to candle precoat filters has been realized in another case of thick juice filtration. Needle felt bags, which featured a nominal separation rate of 1m, showed on closer examination that nearly no analytically verifiable separation happened (see Figure 5).
Despite the insufficient filtrate quality, the differential pressure built quickly, so that an average of 24 bags of the two used multi-bag filter housings had to be changed during every shift. Therefore, bag filtration is no real alternative for the filtration of thick juice, although the level of investment costs would be lower.
PROCESS PARAMETERS
The Standard Liquor (originating from a mixture of thick juice and return flows of crystallization) has a temperature of approx. 95°C and a sugar content of about 70%. The solid content prior to the filtration inlet fluctuates between 8 and 14 mg/L. By using a 10-micron stainless steel filter fabric at a flow rate of 50 m³/h per filter unit OptiFil-250-0720, the solid content was averagely reduced to 3 mg/L or even below.
EFFICIENCY
Despite the high unit flow rates at a filter fineness of 10m, the medium loss is extremely low with 2,5 liters every 5 minutes due to the efficient backwash system. These minimum reject amounts of less than 1% of the filtrate flow differentiate the Lenzing OptiFil significantly from other filtration systems. Originating from filtration of high viscosity fluids, the OptiFil easily cleans the filter material using internal medium. Due to the production capacity, the customer decided on a larger system (OptiFil-350-1080) after the pilot trials. This one unit now filters 100 m³/h of Standard Liquor at a fineness of 10m and requires only one automatic valve. This allows vast savings in complexity and space, as well as investment costs in comparison to traditional filtration systems.
COSTS FOR FILTRATION
While the operating costs for candle precoat filters are enormous only because of the filter aid consumption, and bag filtration requires several manual bag changes every work shift, the Lenzing OptiFil is characterized by nearly no running costs for operation. The filter material can be backwashed several thousand times without changing. Even if it is blocked once (mostly after finishing a production cycle) it can be changed easily. As it is made out of untailored flatware, the filter material used is inexpensive and each change does not take more than 30 minutes.