Among the specifications used to describe wire mesh are the terms “nominal” and “absolute.” Initially there seemed to be a bit of confusion about their meaning and the distinction between the two. After looking into it a bit, that turns out to be an understatement. There is a LOT of confusion.
Filtration mesh and filter assemblies are listed with a variety of specifications: wire diameter, openings per inch, weave type, percent open area, porosity, and one specification called micron retention sometimes listed under the terms “nominal” and “absolute.” These two terms, nominal and absolute, can be the source of much confusion among those seeking answers about what they can expect from a filter cloth’s performance.
In order to clear up this confusion, first consider the variety of conceptions, misconceptions, unwarranted statements, and “definitions,” swirling about the internet. Searching “nominal vs. absolute mesh ratings” yielded the following variety of explanations.
First, not all of us are as fresh out of statistics class as others, so it is forgivable that some of us read right past these words, assuming a more colloquial meaning of the words is all that is intended. Some explanations are relying on colloquial understanding of the words, while others are using strictly statistics definitions.
- Some interpret it to mean the difference between measured openings vs. effective opening.
- Some descriptions of nominal vs. absolute seem to be just copy/pasted from other web sites without much understanding.
- Some state that nominal rating is a calculated opening size, while the absolute rating is the opening size as measured by glass bead testing or bubble testing.
- Some sites got absolute aperture testing done once, who knows how long ago, for one sample of a nominal mesh, and have been publishing that absolute value since then — possibly for samples from different looms, different mills, or woven with different materials.
- Some mesh suppliers publish the absolute and nominal values of mesh with very complicated flow paths that can vary drastically after manufacture into filters.
- Some state the distinction between nominal and absolute as 60% vs. 95% filtration at a listed size.
- Customers will sometimes reject a mesh recommended by an expert based on data they found on some other source, against the recommendation of the expert, and when they send in the sample of the mesh they would prefer that the expert supply for them, it turns out that it was the very same mesh the expert had suggested in the first place, but labeled with unwarranted or unsupported absolute ratings.
- One source states that “Absolute filtration: Indicates that 99.9% of the particles larger than the specified micron rating will be removed by the filter. Nominal filtration: Indicates approximately 80% of the particles larger than the specified micron rating will be removed by the filter.”
- Whatever performance someone needs from a filter, nominal is just whatever a supplier wants to name it, and absolute is a certification earned for a specific sample. Once you’re into complicated weaves, nominal might not even be easy to determine.
- Some sources say the nominal listing is reliable and the absolute rating is not. Other sources say the opposite.
- For some applications, filter performance changes after having accumulated a bit of stuff on the filter and the first cut is tossed or recycled. Some nominal ratings take this into account, others do not.
So what can be said definitively about nominal and absolute filter ratings?
Clearly, the definitions found online are all over the map. How can all these disparate understandings of the terms be reconciled?
Since an internet search only served to further cloud the issue, it was decided to go right to an industry-respected, independent source. An interview was held with Mr. Jon Miles and Mr. Keith Brocklehurst, the lab manager and the senior scientist at Whitehouse Scientific Ltd (Chester, UK), one of the industry’s recommended testing laboratories for independent verification of wire mesh. They explained their glass bead challenge testing, what it can tell us, and what it cannot, about mesh aperture.
Challenge testing is a method of measuring a mesh’s pore sizes by a real-world test of what size particles actually pass through the mesh. It is often called glass bead testing as it is most often done using finely calibrated glass beads of a known size range and distribution.
Keith had just recently presented a paper at the 2022 World Filtration Congress, WFC13 in San Diego, which aimed to define a more statistically robust method of measuring the “maximum pore size,” i.e., the absolute opening, than the existing challenge testing standard set by ANSI/API and ISO for evaluating “down-hole” sand screens used in oil extraction. If a maximum pore size standard already existed, why are they reexamining it and what do they mean by “more robust”? It was a perfect opportunity to pick their brains a bit.
Challenge testing is a method of measuring a mesh’s pore sizes by real world test of what size particles actually pass through the mesh. It is often called glass bead testing as it is most often done using finely calibrated glass beads of a known size range and distribution.
Simplified Example
When evaluating a sample of wire mesh for its potential as a filter cloth, one of the first characteristics to be evaluated is the size of the pores in the mesh. For square weave meshes this is fairly easy. The openings in the mesh are simply the wire spacing, minus the diameter of the wire. A square mesh with wires spaced at 100 wires per meter woven with 1.0mm diameter wires means that, if the weave were perfect, all the mesh openings would be expected to be 9.0mm. However, on occasions, minor imperfections in the quality of a weaving process may occur where a number of mesh apertures are less than perfect. In this case, a 9.0mm marble may fall through some of the apertures and others get trapped in the distorted apertures. In this simplified example, by Whitehouse Labs’ definition, the ‘Cut-Point’ or 97th percentile (d97) rating of that screen, as determined by either direct observation by image analysis or by challenging the screen with a narrow range of calibrated particles, may differ from the expected, 9.0mm value. The ‘Cut Point’ or ‘d97’ are both terms used by the world’s filtration industry to describe the aperture size of a mesh that retains 97% of a specified range of particles challenged.
The absolute retention rating is an attempt to quantify the Maximum Penetrating Particle (MPP) that could pass through a screen. In other words, the largest hole in a screen. In the simplified example, the absolute rating cannot be determined by calculation because the largest hole is a function of the tolerances in the wire spacing and wire diameter. However, it is still possible to directly observe and measure the largest opening by measuring every hole in the screen, all ten-thousand (or more!) of them. The MPP could also be determined by challenge testing the screen with successively larger marbles, eventually finding the marble that only fits through the very largest of those ten-thousand holes. If that MPP were 12.3mm, one could say that the absolute retention rating of that screen is 12.3mm. But that is only verified for one small area of mesh, cut from one particular roll of mesh. Cut another small area of mesh off that roll and the MPP for that sample might 12.5mm. For a third sample it might be 11.9mm. For each sample, the absolute largest hole could be identified, but none of them would be the same.
Measuring each hole or challenging each hole with a test marble – either way, in a mesh sample with ten thousand holes it is quite tedious. It probably is not even very representative of what to expect from the rest of that roll of mesh, so how “absolute” can confidence in those numbers be?
MPP, or the 100th percentile (d100), is not helpful if you are not challenging every square inch off the roll, or if each sample challenged has a different MPP. Instead, what about finding another point close to the MPP that can be proven to be more accurate and, more importantly, meaningful? How about the d99.5? After all, in a sample of mesh with ten-thousand holes, 0.5% is 50 holes. That tells way less about the size of the true single maximum hole, but it tells way more about what can be expected from the rest of the roll of mesh. That is what is meant by robustness of the statistic; once established from one sample, it will reliably predict characteristics of the whole. The MPP is both very accurate and precise for that one sample of mesh, but it has very little predictive value about the MPP of another sample. The size above which the maximum 0.5% of holes fall, though, distributes the uncertainty among all 50 holes. Who cares what the MPP among them is, the median of the top 50 holes will be a very repeatable, predictable number, slightly smaller than the true MPP of any given sample, but consistent from sample to sample.
The best thing this example mesh has going for it, however, is that it makes for a convenient example. It makes the mental math easy, and it illustrates the point, but it would make for a terrible filtration mesh. Real filtration meshes must be woven to catch particles much smaller than 9mm marbles.
Lab Experiment
So, now imagine a complicated weave, where even the nominal rating is only theoretical. They are usually woven with some variation of a Dutch and/or twill (link blog on weaves) weave, often with practically no spacing between the wires. Instead of simple square openings, the openings in filter mesh require filtrate to pass through twists and turns, what is called a “tortuous path.” Such meshes will have a nominal rating, but the nominal rating cannot be easily calculated by counting wires and subtracting wire diameters, and it cannot be directly observed and measured like square mesh. It can only be inferred from challenge testing. For consistency and practicality, the nominal rating for these weaves is still the average pore size, just like with the simpler square weaves.
For assessing absolute micron ratings of filter weaves, calculations or direct observation are insufficient. Only challenge testing works. But which challenge test percentile to use? The single 100th percentile MPP still, or the 99.5 percentile maximum 0.5%, or perhaps the 97th percentile, called the cut point, which would be the maximum 3%?
Returning to the paper presented by Whitehouse at the filtration conference, they were considering methods to get more robust data than a petroleum industry standard. The original standard sought to quantify the MPP using 90mm diameter samples of the filter mesh. The filtration standard 19S, published by ANSI/API, is to prevent sand grains above a certain size from being pumped out of an oil well, accelerating wear and tear on pumps.
In reality, measuring every pore is quite impractical. Actual challenge testing seeks to shortcut some of the counting and, instead, deduce pore sizes by extrapolation.
Moving on from the simplified example, much of the counting can be avoided by using a narrow range of beads at the same time. Whitehouse used a range of mesh aperture sizes to demonstrate their results but only those from a series of 250 micron meshes are referred to here. They produce, and use, narrow ranges of calibrated bead standards each designed to span ± one nominal aperture of the respective aperture target size. In effect, for a 250-micron mesh, this would be from approximately 212 to 300 microns. To do this, they mount the mesh sample in an instrument that holds it flat and vibrates it for a predetermined amount of time while containing all the glass calibration beads. After vibration, they analyze the spheres that penetrated the mesh, looking for the largest ones.
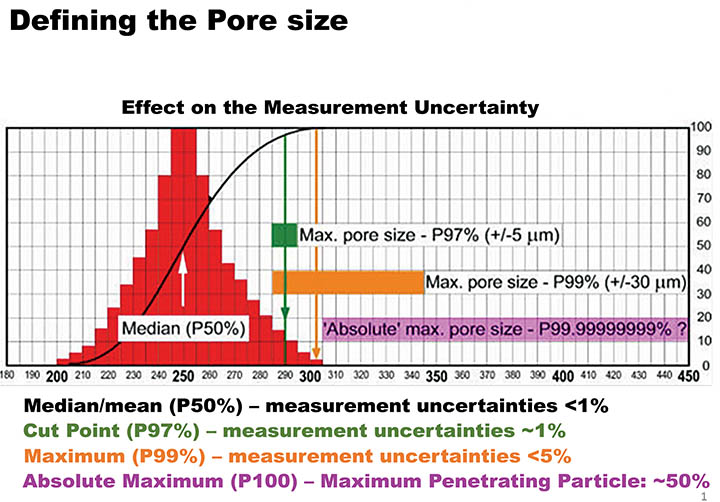
As discussed in the simplified example from earlier, the maximum penetrating particle is only so useful. To reduce the uncertainty, they assess the largest 0.5% of the microspheres that pass through the mesh and measure the smallest of that set. This represents the 99.5 percentile of potential absolute openings (see figure 3). For the particular mesh samples they were examining, that worked out to be a median pore size of 250 micron, and a 99.5 percentile of 302 microns. In other words, the Nominal rating for the mesh is 250 microns, and the Absolute rating for the mesh is 302 microns at 99.5 percentile.
Whitehouse confirms their data in several ways. They create their range of calibration beads using highly precise electroformed sieves and certify sizes according to the National Institute of Standards and Technology (NIST). They also use optical scanners to independently test and verify this data.
They have determined a robust “minimum” number of challenged particles that need to be counted (analyzed) and what they discovered here is that by using the 99.5 percentile rather than the single maximum penetrating particle at the 100th percentile, they were able to reduce variability in the results from up to 47% down to just 3% variability between test trials.
Conclusions
Looking back at the variety of conceptions and misconceptions of how to define nominal and absolute mesh ratings, it is understandable why some mesh suppliers may be hesitant to offer absolute ratings of the mesh they sell, or why the absolute ratings that are offered without further description of methodology are not very useful. This is why some of the internet definitions above have potential to be “good data,” but for a lack of any qualifying percentile or further description.
Interest in absolute retention ratings often seems rooted in a desire for some kind of guarantee that even glass bead testing cannot offer. Even the best testing and certification can only tell us so much about how a filter will perform in real-world conditions. Rarely do the particles in a filtrate actually behave like spherical glass beads, and with enough differential pressure, any particle can become a maximum penetrating particle.
Nominal retention ratings are generally based on the average pore size, which means half the pores skew larger and half skew smaller. The nominal might not offer the best idea of the maximum penetrating particle, but it is the most robust, repeatable statistic with the most predictive value for what to expect from any given sample of that mesh.
Absolute particle retention ratings are based on the largest pores in the mesh. They must include both a size and a percentile. Absolute retention ratings are less robust than nominal ratings, but far more robust than true MPP size. Published tables of absolute retention ratings can be a useful starting point for mesh selection but require a healthy dose of skepticism about their origins and their predictive value.
In the end, testing labs like Whitehouse Scientific are the only way to certify the retention rating of a filtration product, and even then, they are only certifying a probability. If you want more absolute verification than that, get out your microscope and start counting.
Talk to a wire mesh expert about your filtration needs. They can help make sense of retention ratings and all the other variables that go into selecting the right mesh for your application.
Gerard Daniel Expertise
At Gerard Daniel, we’ve been sourcing, weaving, and distributing wire mesh for 70 years and stock the largest range of inventory in North America. Our application engineers use their deep expertise in woven mesh and components to develop the most effective solution, collaborating with your design, development, and production teams to ensure the lowest cost to manufacture. Please reach out if you would like to learn more about our capabilities or visit www.gerarddaniel.com.
Special thanks to Keith Brocklehurst and Jon Miles of Whitehouse Scientific Ltd, Chester, UK. To understand more about glass bead and challenge testing, including learning more about the new 99.5 test, please visit www.whitehousescientific.com, or contact them directly.