Chase Machine and Engineering, founded in 1954, designs and builds custom machinery with a primary focus on the integration of various technologies into continuous and intermittent web converting applications. Technologies such as ultrasonics, thermal bonding, impulse welding, band sealing, hot air and RF welding, CO2 lasers and adhesive dispensing, along with a variety of printing and inspection systems are examples that Chase incorporates into the design and fabrication of equipment, providing customers the ability to convert woven or nonwoven materials into end-use products.
Working with the industry’s leading suppliers of these technologies, Chase provides custom coaters, laminators, embossers, slitters and splicing equipment, as well custom automated assembly equipment to manufacturers of products for the filtration, hygiene, textile, packaging, medical, and personal care industries. Chase’s reputation for being one of the “go-to companies” for continuous ultrasonic machinery is a direct result of the creative solutions it has provided over the last 67 years.
Chase is a vertically integrated company with in-house engineering capabilities utilizing state-of-the-art 3D solid modeling software to design its equipment. Chase’s electrical engineers design all the machine controls and write all the PLC programs. And finally, the electrical panel building, machining, welding fabrication, and machine assembly are all performed on site.
Chase’s facility, located in West Warwick, Rhode Island, has a dedicated lab for continuous ultrasonic and impulse testing. This month we interview Guy Gil, president of Chase Machine to gain some perspective on his company and the broader trends in automation technology specifically for the filtration industry.
Ed Gregor: Can you tell us a bit about the history of Chase Machine and the technology it offers today?
Guy Gil: Sixty-seven years ago, Chase Machine opened for business as a custom machine builder, primarily servicing the New England textile industry providing winders and slitters for companies that manufactured woven webs and lace. In the late 1970s and 1980s much of this work migrated south, requiring Chase to search for new opportunities.
In 1978, we built our first ultrasonic slitter. It was at this moment we knew that ultrasonic technology for use in lamination and slitting applications was the way of the future. Other technologies such as mechanical slitting leave cut edges that can unravel and fray while ultrasonic slitting seals the edge. Sewing, as another example, produces holes which create leak paths while also requiring the use of consumables such as needle and thread. Glue also requires the purchase of consumables, adding cost to the final product. In addition, glue adds weight and reduces breathability (or filtration quality). For these reasons, ultrasonics for joining or slitting synthetic materials is a better option.
Sixty-seven years ago, Chase Machine opened for business as a custom machine builder, primarily servicing the New England textile industry providing winders and slitters for companies that manufactured woven webs and lace. In the late 1970s and 1980s much of this work migrated south, requiring Chase to search for new opportunities.
The ultrasonic process does not require consumables to join materials together. Ultrasonic energy melts the fibers in specific areas which creates molecular bonds that penetrate thru the fabric unlike adhesives that sit upon the surface of the materials being laminated.
The decades of experience Chase has gained since building that first ultrasonic slitter in 1978 is invaluable in helping our customers determine the best technology available for their particular application.
Ed Gregor: Tell us about the range of filtration equipment.
Guy Gil: Chase Machine designs and builds custom web handling and automation assembly equipment. We offer a wide range of products that can produce a plethora of filtration products. For example, our standard FS product line, which are manually operated ultrasonic “sewing” machines that utilize Branson Ultrasonic equipment, are available for customers that want to manually make a variety of filter products such as liquid filter bags, pocket filters or even facemasks.
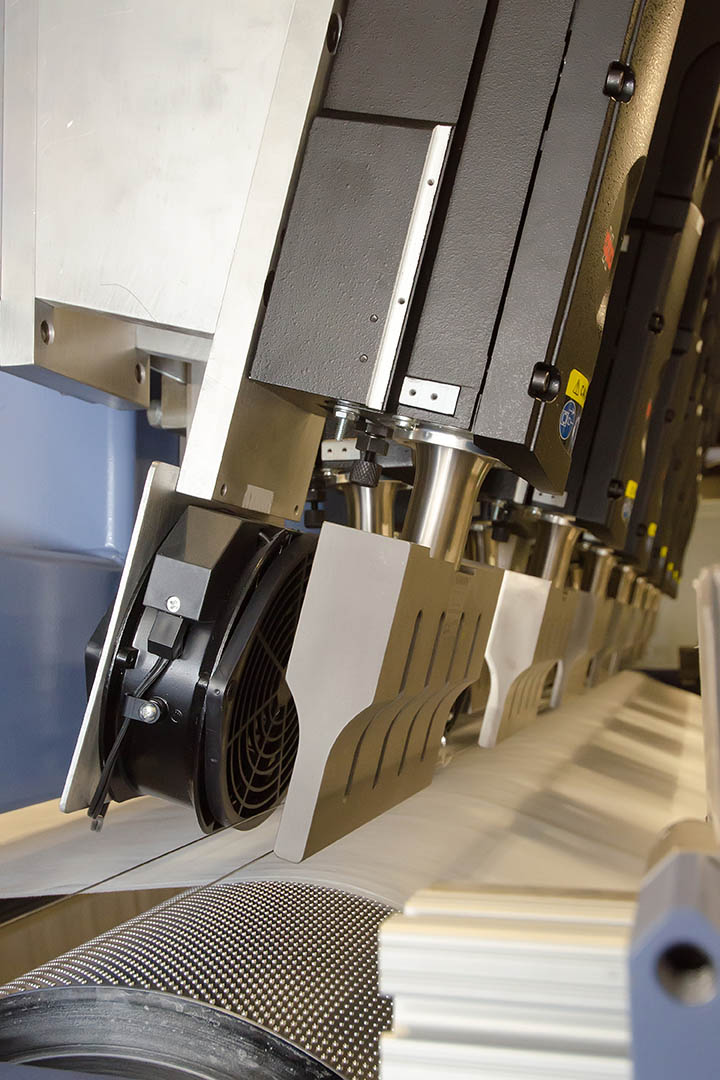
For those customers looking for a more automated solution, Chase manufactures surgical facemask machines, ultrasonic laminators and slitters utilized to bond and slit multiple layers of material together to create a variety of filtration media, hot-air tube forming equipment for liquid filter bags, ultrasonic tube formers, HVAC pocket filter machines, ultrasonic sealers for pleated filters, hollow fiber lines and membrane casting machines as well as custom machines designed specifically for our customer’s needs.
Ed Gregor: What about internal engineering capabilities in filtration?
Guy Gil: Chase’s engineering team, consisting of five mechanical and two electrical engineers, each do an excellent job listening to customers and then finding the technology and process solution that can be implemented successfully and cost-effectively.
Ed Gregor: Does Chase make filtration products as contract-manufactured products for customers?
Guy Gil: While Chase does not manufacture filtration products for customers on a contract basis, Chase’s dedicated lab for continuous ultrasonic and impulse testing is available for short-term pilot studies. Customers may send product to Chase in order to collect invaluable data such as bond strength, embossing quality, slit quality, power requirements, and processing line speed – information that is crucial in determining quality, feasibility and payback.
Chase has also performed short-term ultrasonic lamination and slitting trials in an effort to provide customers product while their machinery is being fabricated.
Ed Gregor: How has COVID-19 impacted your filtration business? Have there been any other industry trends that have impacted your business in recent years?
Guy Gil: As many know, the COVID-19 pandemic has put an enormous amount of pressure on filtration and Personal Protective Equipment suppliers to meet the increased demand for product. Chase Machine’s customers span both the filtration and medical markets where equipment to make facemasks, air filters and custom web handling equipment such as ultrasonic laminators, slitters and winding equipment are in high demand. In addition to our custom machinery, Chase’s ultrasonic sealing machinery such as our FS-90 and FS-180 machines have been difficult to keep in inventory.
Ed Gregor: Any trends you see having an influence on filtration going forward?
Guy Gil: I believe the filtration industry is positioned for a significant amount of growth in the coming years. If the pandemic taught us one thing, it was that PPE supplies were inadequate and the ability to fill the pipeline quickly was extremely difficult. Daily use of facemasks are going to become more and more accepted and the need to improve the filtration of air in offices, schools, factories, hotels and homes will certainly drive the demand for new and improved products.
For more information about Chase Machine and Engineering, contact Guy Gil at guygil@chasemachine.com or visit see chasemachine.com.