Innovations in membrane and filtration manufacturing methods are essential to match the performance challenges or simply lower production costs. The reliance on conventional materials and production is both advantageous and disadvantageous. The market shifts with high-volume demand and the urgency to adapt to challenging situations. Take the case for the increased need for N95 masks and other personal protective equipment (PPE)s during the pandemic and the urgency to clean the air from pathogens.[1]
In membrane and filtration applications (including separations), a key driver for innovation is both performances and cost oriented. While having a higher production volume on an existing production line or maintaining the supply chain of materials is more accessible, using tools, including digital manufacturing and artificial intelligence (AI)/machine learning to prepare for the next generation of materials and. manufacturing methods is essential.[2] There is a need to examine the recent advancements in materials and processes in 3D printing for membrane and filtration-related applications: ultra-filtration performance, adsorbents, module spacers, novel filtration and desalination membranes, applications in water remediation, catalysis, etc.
Already, 3D printing is driving innovation in many industries and academic research: aerospace, automotive, marine, healthcare, etc., and this should include the clean air and water resource sector. 3D printing enables the fabrication of complex designs and objects. Depending on a combination of tool fabrication and materials choice, it can be a fast, cost-effective alternative and highly desirable over conventional membrane and filter manufacturing processes. [3][4]
In modern society, membrane separation and filtration processes are essential to provide supply safety, convenience, and scalability in manufacturing. It plays a significant role depending on the separation mechanisms, scale and size of the separation, and the flow or production rate. In the case of water purification, this can be at the point of access by the consumer or back to the production plant. Membrane processes can include microfiltration, ultrafiltration, and nanofiltration. Differentiation with membranes can simply be based on the famous Robeson diagram that plots selectivity vs. permeability, as shown in Figure 1. They are widely used in water purification (consumer), food and beverage processing, enhancement of bioreaction products, and other biotechnological applications. In the pharmaceutical industry, which involves phase purification, antibiotic, and protein purification and production, there is a high demand for purity and even asymmetric separations. More complicated mechanisms involving field gradients can be found in reverse osmosis, electrolysis, dialysis, and electrodialysis.
![Figure 2. 3D printed CO2 separation performance from a commercial-based silicone material: (a) DIW-printed PDMS membrane. (b) Mechanism of gas separation through the PDMS membrane. (c) Robeson upper bound correlation plot showing the gas separation performance of PDMS-0S and PDMS-10S membranes compared to other membranes reported in the literature. (d) Permeability and (e) selectivity of PDMS-0S and PDMS-10S. From Reference.[5]](https://www.filtnews.com/wp-content/uploads/IFN_042023_membranes_Figure2.jpg)
Also, it should be noted that this can be pressure driven for all processes except electrodialysis. In water purification, the microelectronics industry relies on very pure water, and therefore nanofiltration and reverse osmosis membrane methods have to be used for this specific water purification. Appreciating the scale based on particle size and flux behavior is essential. Carbon capture and enrichment of resources can involve gas separation, vapor permeation, pervaporation, and membrane distillation. What differentiates these processes, except for pervaporation, from other separation methods is that it consists of no phase change on the fluent. Regarding scale and size, dense membranes must be configured and utilized for gas separations (scrubbers, CO2 from natural gas, separating N2 from the air, organic vapor or acidic vapor removal from air or exhaust streams).
There is a need for different types of materials and fabrication methods for each of these applications. We have recently demonstrated enhanced CO2 separations in 3D-printed silicone membranes (PDMS).[4] Figure 2 shows performance and calibration with previously reported separations. It shows the DIW-printed PDMS membrane and the mechanism and flux of gas separation through the PDMS membrane. The Robeson upper bound correlation plot showing the gas separation performance of PDMS-0S and PDMS-10S membranes compared to other membranes is vital as it puts the permeability and (e) selectivity of PDMS materials into context.
Additive Manufacturing (AM) is a fabrication process using a “printing machine” for parts or prototypes by the “addition” of layer upon layer of materials based on a computer-aided design (CAD) model.[5] The 3D model also provides exact dimensions and geometry that can be translated to an actual processing “twin” based on controlled parameters that align with the machine’s capabilities. A tool path enables a precise axis orientation and boundary condition that further refines this fabrication process. The four stages of AM can be divided into four stages, as shown in Figure 3: 1) Selection of AM technology,
2) Design or acquisition of CAD file, 3) Conversion to an AM-friendly file or slicing, and 4) Actual fabrication by 3D printing. Although many reported methods exist, the technology can be divided into at least seven major categories. This includes material extrusion, powder bed fusion, vat polymerization, material jetting, binder jetting, directed energy deposition, and sheet lamination.
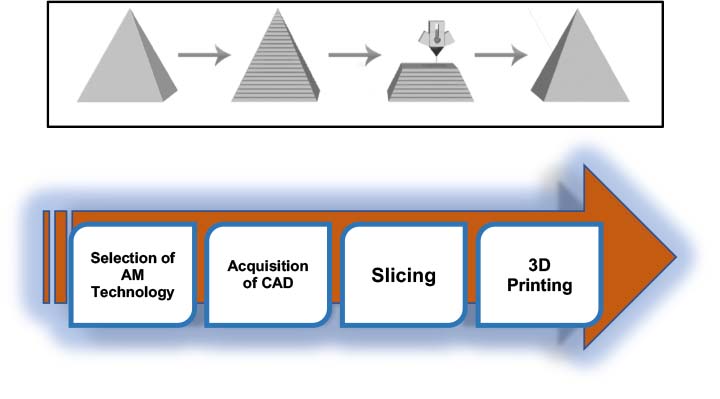
The choice of AM technology can be based on the materials used, the intended process of adhesion or curing, the quality or resolution of the final object or finished product, product specification or standardized properties, and finally, the intended application. In the membrane of filtration prototype or fabrication processes, it is possible that the parameter space for the application of AM will also depend on the environment and stresses that the object will be used. For example, in high-pressure and continuous flow applications, the membranes are expected to have thermo-mechanical properties (tensile, compressive, and flexural properties) that will not degrade based on the printing direction. By understanding the limitations of each method, it is possible to fabricate several unique geometries with peculiar flow or flux properties.
An example of AM method differentiation for membrane or filter application is as follows: In materials or binder Jetting technology, it uses droplets of liquid binder “glue” to join powders to form layers into a solid object. But the individual layers can have different compositions, defining the porosity based on powder size, asperity, and size distribution. The process is relatively simple and flexible in that the dispersion of the particles and choice of the binder are optimized for specific machines. Although in an actual filter or membrane application, it can have weak structural integrity at the interfaces due to poor binding properties and packing factors that degrade with constant flow and high pressures. In selective laser sintering (SLS), a form of Powder Bed Fusion that utilizes focused thermal energy with a laser or electron beam to deposit materials, the fusion or sintering is more robust. This is done by melting the materials (without needing the binder) and fusing them into the surface or layer formation process. This method can generate better membrane operation properties since it fuses the materials themselves with a high energy output, e.g., laser, on a layer-by-layer basis. The choice of powders, polydispersity, blends of powders with other powders and additives, etc., can be the route to improve and create new properties. The fused materials will be limited based on their melting points and cohesive properties. However, the manufacturing cost can be expensive and may be prone to deformations caused by non-uniform thermal contraction and expansion, even during fabrication.
A cost-effective compromise may be obtained in material extrusion methods, which is a widely used AM technology. These methods include focused deposition modeling (FDM) or direct ink writing (DIW). In this case, the viscous or melted material can flow and deposit layer by layer. The starting materials can be polymer filaments, pellets, or viscous solutions of gels or adhesives that can be fed into a heated or non-heated nozzle to form layers. But it can have thermo-mechanical issues due to the formation of voids in-between layers and the poor adhesion between layers.
Figure 3 shows our work on oil/water separation membranes based on 3D-printed silicone inks and their ability to retain performance after several cycles. [6] The ability to separate oil and water was built on the materials, including elastomeric properties. But the porosity was generated post-printing. In Vat Photopolymerization, which uses ultraviolet (UV) or visible light to initiate resin cross-linking to form 3D structures, high resolutions of the object finish can be achieved. The caveat is the lack of control over porosity because of the acceptable layer resolution (up to 50 microns). It can form high-quality material finishes with relatively low manufacturing costs but has issues with materials’ selectivity due to the limited type of acrylate chemistry that can be used. This may be modified by using compatible reactive oligomers or telomers of polyurethane, polybutadiene, polysulfones, etc., in the case of polymer membranes. Finally, an interesting process could be the sheet lamination technique which forms an object by consecutive bonding of cut-out material sheets. Based on prefabricated layer sheets, the sheet can have a porous nature and thermo-mechanical integrity. This process can be used on various materials and can be of relatively low cost due to using prefabricated laminate sheets with built-in membrane properties. But it has a poor surface finish and perhaps poor bonding between layers that may delaminate over time. Furthermore, it has less accurate X-Y-Z control and can have difficulty creating complex shapes.
![Figure 4: 3D printed oil-water silicone membranes. A) 3D printed the PDMS with drops of water (blue color) and oil (red color) on the surface. B) Contact angle image of drop water on the PDMS surface. C) Optical images demonstrating the selective oil absorption in water by the 3D-printed PDMS object. D) Optical images demonstrate the swelling of 3D-printed PDMS after oil absorption. E) Oil absorbency of PDMS sponges with different gaps and formulations. F) cyclic oil absorbency of 3D printed PDMS membranes. From Reference.[7]](https://www.filtnews.com/wp-content/uploads/IFN_042023_membranes_Figure4.jpg)
Technological advancements will allow materials scientists and engineers to create complex 2D and 3D digital membranes and systems work designs. The advent of AI in materials and manufacturing, including R&D and characterization methods, should append the industry. New membrane designs can be acquired using 3D modeling software, 3D scanning, and 3D imaging. Furthermore, 3D scanning and 3D imaging methods can obtain the unique shape and size of the prototype object as XYZ-coordinates. Slicing will enable the conversion of CAD into command codes for the 3D printer. Printing parameters like resolution, print speed, operating temperatures, etc., can be set to determine its tool path or guide how each layer of the 3D model should be created.
This detailed explanation should give a quick appreciation of 3D printing in membrane and filter design since each layer can be considered a “separation unit” which can be stacked directionally against the flux of separation of filtration direction. A significant advantage is the appreciation of the material itself, which can have thermo-mechanical and porosity of barrier properties that can be compared with other filter materials, e.g., for polymers this can enable new properties in polyurethanes, polyvinylidene fluoride, polysulfones, etc. The differentiation is that in macroscopic properties from monolithic bulk membranes from conventional manufacturing, it is possible to build these properties on a layer-by-layer and directional basis. If printing is the actual generation of the product, then post-processing can offer even greater systems engineering for a filtration or separation operation. These post- or finishing processes can include embossing, drilling, cutting support structures, removing excess or loose powder, washing excess resin, post-curing or generating more porogen, etc. This may be needed to enhance system integration’s final output quality and performance.
The rapid increase in research and development using 3D printing for membrane filtration, air filtration, desalination, and water purification applications, can potentially revolutionize the industry. New materials and 3D printers will emerge that are very specific for the membrane and filtration industry with highly controlled flow and flux behavior, higher printing resolution, better efficiency and speed in production, and, more importantly, broader material applicability in many demanding applications. This advancement can potentially reshape research and development in this industry. The future and prospects of 3D printing and new materials applications are bright.
References:
- Sumpter, B.; Hong, K.; Vasudevan, R.; Ivanov, I.; Advincula, R. “Autonomous continuous flow reactor synthesis for scalable atom-precision,” Carbon Trends 2023, 10,100234.
- Advincula, R.*; Dizon, J.; Chen, Q.; Niu, I.; Chung, J.; Kilpatrick, L.; Newman, R. “Additive manufacturing for COVID-19: devices, materials, prospects, and challenges,” MRS Communications 2020, 10 (3), pp.413-427.
- Tijing, L.*; Dizon, J.; Ibrahim, I.; Nisay, A.; Shon, H.; Advincula, R. “3D printing for membrane separation, desalination, and water treatment,” Applied Materials Today 2020, 18, 100486.
- Gutierrez, D.; Caldona, E.; Espiritu, R.; Advincula, R.*
”The potential of additively manufactured membranes for selective separation and capture of CO2,” MRS Communications 2021,
11 (4), p. 391-401. - Gutierrez, D.; Caldona, E.; Yang, Z.; Suo, X.; Cheng, X.; Dai, S.; Espiritu, R.; Advincula, R. * “3D-printed PDMS-based membranes for CO2 separation applications,” MRS Communications (2022). https://doi.org/10.1557/s43579-022-00287-1
- Dizon, J.; Espera, Jr., A.; Chen, Q.; Advincula, R.* “Mechanical characterization of 3D-printed polymers,” Additive Manufacturing 2017, 20, pp. 44-67.
- Chen, Q.; Zhao, J.; Ren, J.; Rong, L.; Cao, P-F.; Advincula, R.* “3D printed multifunctional, hyperelastic silicone rubber foam,” Advanced Functional Materials 2019, 29 (23), 1900469.