The story of Bekaert started in 1880 in Zwevegem, a smaller rural village in Belgium, where local farmers were faced with the perennial problem of cattle showing the stubborn habit of straying beyond the boundaries of their fields and onto other people’s property. Leo Leander Bekaert translated this challenge into a business opportunity, starting up a small business in barbed wire by putting nails in twisted wire. Leo Leander Bekaert didn’t invent barbed wire, but he soon designed his own barbs – star-shaped “crowns” with six sharp points, which could be woven into the wire. In 1881, he patented this invention and in next to no time, recruited most of the village to work at home making his “crowns” to enable Bekaert to continue producing at full speed.
Now, 140 years later, Bekaert is reinforcing 30 percent of all tires in the world with steel cord products, reinforcing more than 10 million cubic meters of concrete per year with Dramix steel fibers and offering a wide range of steel wire products to various applications in agriculture, mining, energy, consumer goods, construction and automotive.
Bekaert’s Fiber Technologies business unit manufactures metal fibers and, in some cases, sinters fibers composed of pure metals and metallic alloys, which can be processed into textile products, porous media and plastic-coated metals, pushing the boundaries of metal fiber technology to enable new applications that contribute to a cleaner, safer, quieter and more comfortable world.
With five production sites, three R&D centers and sales offices in most regions, Bekaert Fiber Technologies is the market leader in the production of these fine metal fibers, ranging from below 1 micron to over 40 micron. The product portfolio consists of metal fibers (continuous fibers, short & staple fibers, anti-static fibers and conductive grades), blends & yarns (conductive blends, conductive spun yarns, conductive and durable heating yearns), heat resistant textiles (knitted fabrics, braided ropes, square braids and sleeves) and porous media (nonwoven fabrics, sintered media, engineered media and engineered 3D shapes).
R&D and co-development is part of the company’s DNA, allowing Bekaert Fiber Technologies to become a leading supplier in critical applications in nuclear, semiconductor, automotive and the aviation industry. Metal fibers provide a solution for numerous filtration applications – including nanofiltration – that other material forms are unable to match, providing high temperature and corrosion resistance, high mechanical strength and high porosity for low pressure drops.
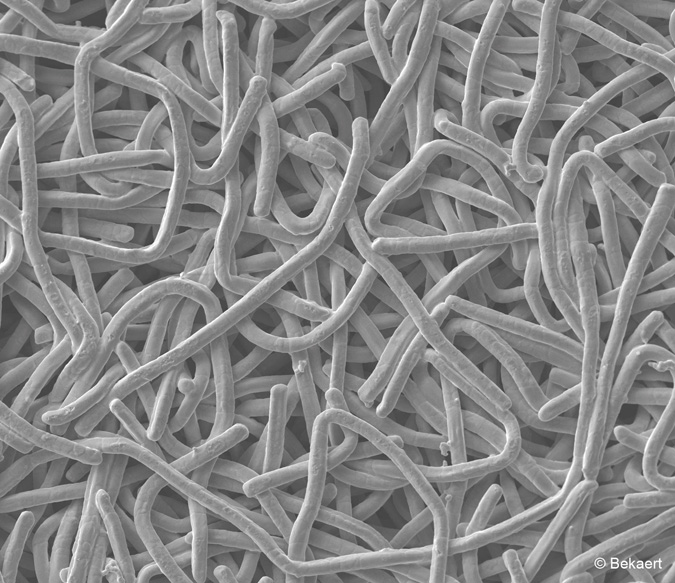
In this issue of IFN, we interview Ms. Inge Schildermans, vice president of Baekert Fiber Technologies.
Ed Gregor: What differentiates Bekaert from the competition in filtration media?
Inge Schildermans: We believe the following six reasons are critical factors that enable Bekaert to differentiate from the competition.
- High permeability – the combination of high porosity and thin filter layers at high mechanical strength provides unique permeability characteristics at levels unmatched by any other filter medium
- High porosity – metal fibers produce media with a high fraction of void space and up to 90% porosity, resulting in low pressure drops, high flow rates and high permeability
- High dirt holding capacity – the combination of the tortuous path and graded layers of fiber diameters, metal fiber can hold more dirt compared to metallic mesh and other non-metallic filter media
- High mechanical strength – metal fibers enable a mechanically strong 3D network of metal-to-metal connections. The media maintains its integrity under high vibration and pressure
- Thermal & corrosion resistance – metal fibers in alloys 304, 316L, Fecralloy®, Inconel® 601 and Hastelloy® display high-temperature corrosion resistance at both the surface and the underlying steel.
- Our global footprint enables us to remain a market leader for production of metal fibers, local R&D and application support in the end application.
Ed Gregor: Are there any new metals, on the way or recently offered for use in filtration?
Inge Schildermans: 316 stainless steel has been the backbone of our business along with certain high-end alloys like Hastelloy, Inconel and Fecralloy which are used in special demanding situations, but the above differentiation areas are where Bekaert shines with its filtration capabilities. We continuously try to extend the limits of fiber manufacturing, both in physical properties (eg nano-dimensions) as in material composition (such as Ti, Ni, Cu, etc.)
Ed Gregor: Do you sell fiber and yarns as well as sintered constructions into filtration?
Inge Schildermans: Yes, we sell fibers and yarns as well as sintered constructions, but let me be clear, we do not make or supply final or finished filters which would be in direct competition with our customers. Obviously, we do not (want to) go that route.
Hydraulic fluid filtration systems based on metal fibers display a significantly improved performance and durability along with reduced operating costs compared to traditional glass fiber and cellulose fiber media.
Ed Gregor: Can you tell us more about your filtration business?
Inge Schildermans: In general, polymer filtration is an important part of the overall filtration portfolio of our business. Here we see overcapacity in polyester polymer market with much consolidation happening worldwide while increasing higher graded polymer production overall (optical film), also, recycling of plastics, requesting more demanding, robust and qualitative filtration. In addition, more stringent environmental legislation is increasing internationally, pushing boundaries of dust abatement with conventional means (cyclones, scrubbers, ESP) to dust abatement at high temperatures. In the semiconductor industry, there is the push for smaller footprints and lower pressure drops while requesting even finer and finer filter ratings. In the aviation industry the trend is for more safe, clean and reliable hydraulic systems, shifting from the traditional filtration using glass fibers to more robust filtration from metal fibers.
Ed Gregor: Speaking of trends, a perfect lead-in for my final question. What are recent trends in metal fiber filtration?
Inge Schildermans: Hydraulic fluid filtration systems based on metal fibers display a significantly improved performance and durability along with reduced operating costs compared to traditional glass fiber and cellulose fiber media. Metal fibers show increased mechanical strength and electrical dissipation, reduced particle shedding, and improved cleanliness levels of the hydraulic fluid.
Tests have demonstrated that metal fiber filters can reduce failures in hydraulic components tenfold, with a corresponding doubling of the mean-time between failure, which lowers the risk of fatal accidents and significantly reduces maintenance and repair costs for fleet operators. For these reasons, metal fiber media are being increasingly used for aviation hydraulic fluid filtration systems instead of traditional glass fiber media. One such product is Bekaert’s Bekipor® metal fiber, which maintains its efficiency and integrity of structure throughout its lifetime thanks to strong, sintered bonds, and its high resistance to shock, vibration and pulsing flows proven in Dynamic Filtration Efficiency Testing (DFE) and operational trials.
For inquiries about Bekaert Fiber Tehcnology, contact Mark Willingham at Mark.Willingham@bekaert.com.