Airmid Healthgroup is on a mission to take testing to the next level by validating consumer product expectations and understanding more about air quality post-COVID.
With the 2020 pandemic came heightened concern for clean air and surfaces, as well as an increased use of personal anti-viral and anti-bacterial solutions. According to recent reports, 928 billion face masks totaling $389 billion in sales were sold during the pandemic. Market data provider Statista estimated that global sales of face masks, including surgical, respirators (N95-like) and cloth masks, surged from 12.5 billion in 2019 (mainly for medical personnel) to 378.9 billion in 2020 alone. Hand sanitizer sales also jumped 600% according to the Wall Street Journal – and while it settled down to more normal numbers, this category remains strong and increasing. Furthermore, according to manufacturing companies, the demand for disinfectant products spiked more than 500%. The global wipes marketplace skyrocketed and is estimated to increase 8.2% by 2027.
All in all, personal protective equipment, surface wipes, air purifying sprays were the consumer’s first line of defense to battle the rogue virus. Products vowed to be effective, such as “kills 99.9% of germs,” whether “proven to be effective” or not. While the “shelter-in-place” setting was controllable, air quality in public places was – and still is – subject to air filtration that is controlled by others. From transportation to schools to places of business, the public relies on air filtration systems to be as effective as possible.
This air movement is a concern to the team at Airmid Healthgroup, a testing, inspection and certification company specializing in aerobiology – the study of airborne microorganisms, pollen, spores, and seeds, especially as agents of infection. Airmid founder and CEO Dr. Bruce Mitchell uses his medical background to advise on results for their clients. They provide verifiable scientific evidence on the effectiveness of products, services, equipment, and media. Furthermore, the company uses their test environments to understand the correlation between air movement and impacts on public health.
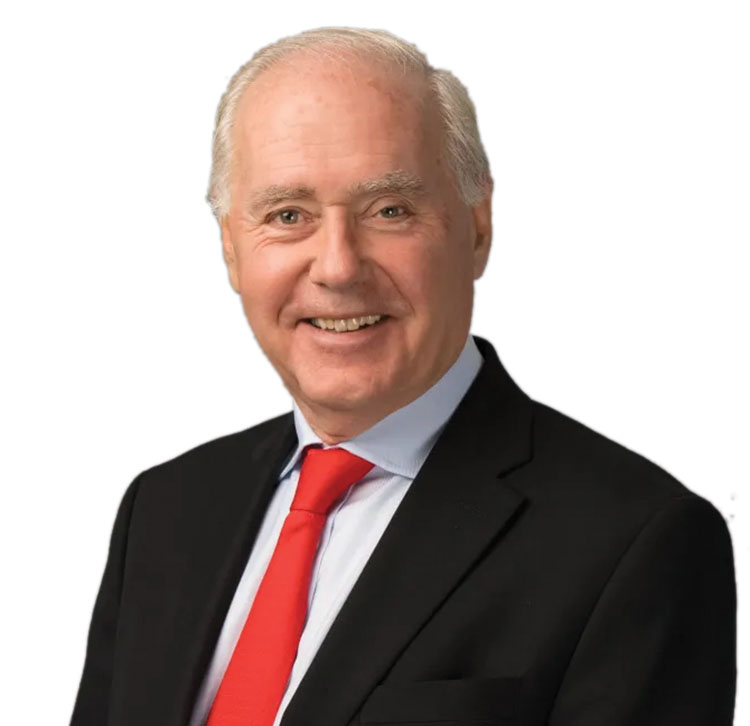
International Filtration News spoke to Dr. Mitchell on his mission to study air quality, and Airmid’s dedication to quality testing and certification solutions.
International Filtration News: What is your background and how did Airmid Healthgroup begin?
Dr. Bruce Mitchell, Airmid CEO: I was a practicing medical doctor and a clinician for the great majority of my life. My medical background has taken me through the United Kingdom, the United States and Canada, as well as Ireland. Among other experience, in the U.S., I was based in Connecticut, where I was a fellow in Yale University and in Canada, I was at a McMaster University. Currently, I am a fellow of the Royal College of Physicians in Ireland, the Royal College of Physicians in Canada and a diplomat of the American Board of Allergy and Immunology. I also serve as director of the Immunology Laboratory, Blackrock Clinic and a past President of the Allergy Foundation of Ireland, and a past member of the WHO sponsored International Workshop on Dust Mite Allergy.
So, you could say that I am heavy on the academic side of medicine. In particular, I worked under Tom Platts-Mills [currently a Professor, Medicine at University of Virginia specializing in Asthma, Allergy and Immunology]. He and I worked closely for many years doing research involving environmental controls. Ultimately, we each went on to different opportunities.
Much of the environmental research on which he and I focused was related to asthma and allergy – what in our environments make people become asthmatic.
It was always clear to me that there was a need for measurement. The information on common exposures and dose responses was not based in science.
I had in my mind early on to develop a laboratory facility that could fill this gap in research, and it took me quite some time to get here. I made several attempts early on, but I was too busy, clinically. Then in 2008, an opportunity came and this time I took it to start Airmid. The result has been very successful, and we are helping our international client base to verify their product claims.
IFN: Tell us about your facilities and capabilities.
Mitchell: While we are based in Dublin, Ireland, the largest portion of our client base comes from corporate brands in the U.S. We’ve even gone as far as Hong Kong to do a study for a client. We also work with government authorities in Ireland on mold remediation in old buildings.
At the onset of COVID-19, we had an array of testing capabilities to offer and were overwhelmed with client work to verify claims. We leveraged our viral capabilities which we had developed prior to the pandemic, as well as utilized our established microbiology lab and allergy lab. A unique element of our services became quite beneficial to our client services – which is our suite of nine test chambers of varying sizes.
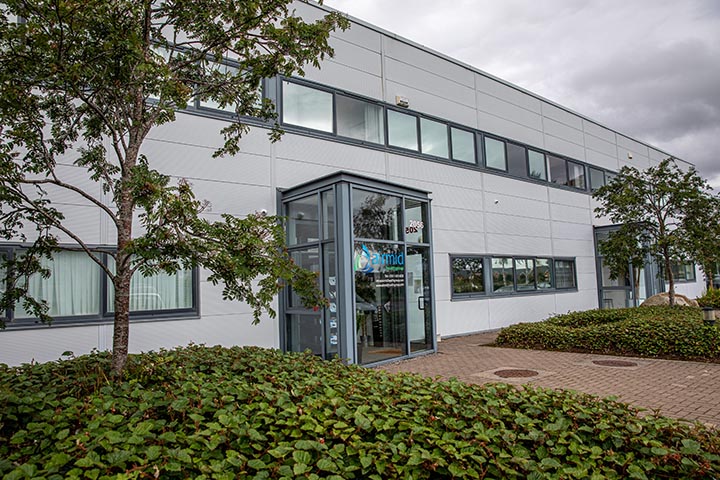
Essentially, these chambers are a variant of clean room technology, built by engineers who have this expertise, and are completely controlled to avoid any contamination. As full-size rooms, we can mimic a variety of environmental conditions, safely introduce and contain microorganisms, evaluate how they behave when in contact with a client solution, and then decontaminate the chambers quickly, without harm. We can create relevant climate conditions, like specific temperature, humidity, air change rate, and air flow rate. It only takes seconds to dump all the air out of a test chamber to clear it.
In the main laboratory, we perform our analytical work with bacteria, mold, and viruses. We can take samples to see what occurs in a certain situation we have had fascinating experiences with allergens,
microorganisms, and mold, which has been particularly interesting for us.
For example, we can evaluate filters which support mold growth, such as paper media, does the mold stay on the filter or does to go into the interstices of the HVAC system, contaminating the ducting? We can determine the quality of the air that’s coming out of the duct. This data becomes highly relevant and highly important for companies and end users to know.
IFN: Is testing of claims and verification becoming more commonplace?
Mitchell: During COVID-19, we were at capacity with testing. It was so busy. But in general, testing can be seen as cost prohibitive, and some may not want to test unless mandated. We want companies to voluntarily test their claims, not be mandated.
Recently in the UK, an infant tragically died while living with her family in a damp apartment where toxic mold was growing. This is not a unique case, and it is happening in a first world country in 2023. Wherever the responsibility lies, we need to look out for our fellow human beings. In my opinion, you’ve got to know how products, equipment, and filter media function and how contaminants spread.
We work with many kinds of companies and manufacturers – like makers of mattresses, air and surface cleaning products, vacuum cleaners, dehumidifiers, and others. They ask us to verify their unique product claim as to its performance. Where viruses are concerned, if you are going to say “kills 99% of all germs,” data is important.
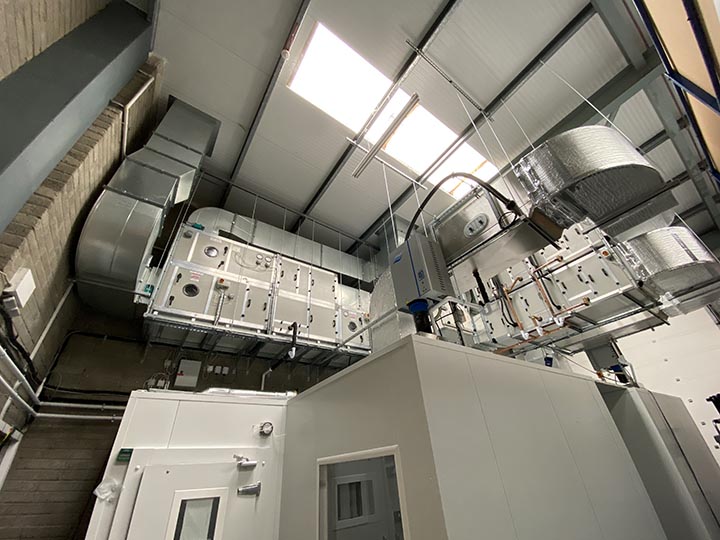
IFN: What happens when testing for a client does not meet their expectations?
Mitchell: About 20% of our client’s tests do not meet their desired measurements. However, we provide consultancy to our clients, with actionable ideas and thoughts. Honestly, companies hate when their products do not work as expected. Yet, most companies who seek our third-party verification are confident they will receive the results they claim because of their internal testing.
IFN: Tell us about your team and mission.
Mitchell: Our mission is to prevent ill health caused by exposure to indoor air pollutants. To achieve this goal, we have assembled a unique physician led multi-disciplinary team of 20-25 scientists specializing in virology, bacteriology, mycology and allergy.
Very few of the team are nonscientific. Many are trained in varying degrees and disciplines in microbiology, with specialties in bacteria or fungal molds or in testing systems. Even Airmid’s Head
of Operations, Jake Behan, is a trained micro-biologist.
IFN: Explain your testing methodology.
Mitchell: Our work primarily is chamber work. For instance, one project involved recreating a public washroom in an office setting, where we evaluated the facilities. We tracked movement of people and various functions of the space to discover the points of contamination.
If you’ve got the flu or coronavirus as the contaminant, and your solution is applied, that is one thing. But my mind wants to know, once the application is in use, then what is a person subsequently contributing to contamination when sitting or moving through these treated spaces? What other surfaces are affected?
This is very interesting to me. The fact is that you disturb the air as you merely move through a space. How do you cause contamination of the air when you turn on the hand dryer? Well, it all depends how it’s designed. So then, should we use paper towels? In both cases, you’re essentially pushing water vapor into the air.
If the water vapor is carrying something into the air, what are the ramifications? Then, consider the floor as contaminated, as an example. Will a vacuum cleaner or filter become a source of contamination to other areas? And so on.
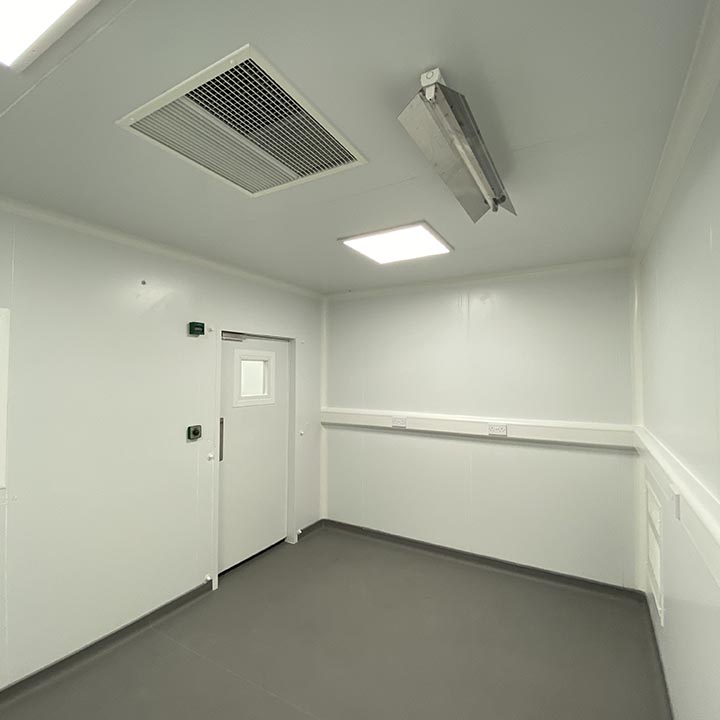
IFN: What’s in store for Airmid’s future?
Mitchell: We grew during the pandemic at a massive rate; we couldn’t really sustain it. Therefore, we had to prioritize and focused on air purification. We must have tested hundreds of air cleaners, with all sorts of technologies – from filtration to plasma to ionization to composites. Currently, business growth is tied to
upgrading our accreditations. We have ISO 17025 accreditation, and we are qualifying for GLP (Good Laboratory Practices). Our next area of focus is to providing testing services to the MedTech and Pharma industry.
IFN: How do you support the textile and filtration industry with testing?
Mitchell: We work with manufacturers of textiles, such as evaluating extremely fine fibers to provide the potency of the microfiber in a particular direction, like anti-allergen, anti-viral or anti-bacterial. We can similarly determine results for odor reduction. The textile can be a garment to cleaning cloth. You’ll see some products that have anti-microbial additives incorporated in them and that there is a sanitation element, particularly in the bedding sector.
One active interest stemming from our work during COVID is the importance of effective filtration technologies in transportation, and we are currently working with companies on this within Europe. The goal is to prevent infection from spreading within public transportation. We want to mitigate situations and seek out environmentally-friendly approaches to balance energy efficiency and effective filtration technologies that can do the same job as, say, a HEPA filter.
To remove 99% of airborne molecules requires quite a lot of energy to produce effective results to create that airflow across the filter. There are many novel technologies that are being introduced that may or may not be effective. We are working to develop methods to accurately assess how well these technologies perform.
A product may work well on a bench test, but when scaling to the size of an actual environment in our test chamber, when simulating an airplane or train carriage, air flow patterns behave very differently. Therefore, product efficacy is also very different.
IFN: Tell us about your work in large-scale filtration testing.
Mitchell: We can link our chambers to simulate a home environment. We can evaluate what happens in one space as a consequence of what is happening in another space. That’s highly relevant to heating ventilation and air conditioning systems. It’s fascinating how you can model the contamination pattern and sequence that occurs. We have recirculation capabilities, either by extending ducting around the outside of the chambers or within the chamber, which illustrates the flexibility of our testing systems.
We have been working to accurately represent public transportation vehicles to effectively assess whether certain technologies are beneficial. I think it’s very important going forward to offer this type of full-scale testing to support companies that are addressing this question. We want industrial filtration end-users to be confident that their air quality solutions are tested and effective, especially when the next pandemic comes around. Eventually it will come, at some point, in our future.
We are expanding our facilities, which will include two buildings totaling 10,000 sq. ft. We’ve earmarked one for a larger test chamber to simulate transportation environments, such as an airplane, subway car or bus.
We can control the hygiene of a surface with products and sprays, but with air, there is no real control other than what is used for filtration. There are regulations on water quality, but none on air quality. As we learn, we can better assist with the development side of new products, such as prototype testing.
IFN: What is the general future of testing?
Mitchell: There are large companies behind filtration, in the U.S. and internationally. It is not a fast-moving industry. I’d like to see it evolve a little bit more. I think we’re ready for a jump to the next level. I believe it is on the radar, but because you’re dealing with large-scale mass-manufactured air systems, it’s not something that you can really change on a dime. Industry has work together on systems and media.
In textiles, there are still things to learn. How long does the effect of a product last? It is one thing to know the saturation level, but another is its continued effectiveness.
Another practical test is contact time. In testing, air is circulating at a controlled rate, yet in a real situation, air moves more unpredictably. Is the tested item getting the correct contact time for the solution and does it perform well? Is the technology wrong or possibly is it the design?
We’re on a mission to look at these deeper, challenging questions that affect the health and well-being of consumers, and help clients bring advanced solutions to end-users that meet and exceed expectations.