Despite the vast scale, complexity and diversity of today’s filtration system installations, the simple filter media is the key to everything.
Or the not so simple filter media, as became evident when assessing just a handful of the over 200 presentations running parallel to this year’s FILTECH exhibition, which took place in Cologne, Germany, from October 22-24.
Among media-related presentations were those from filtration businesses that now belong to some of the biggest organizations in the world.
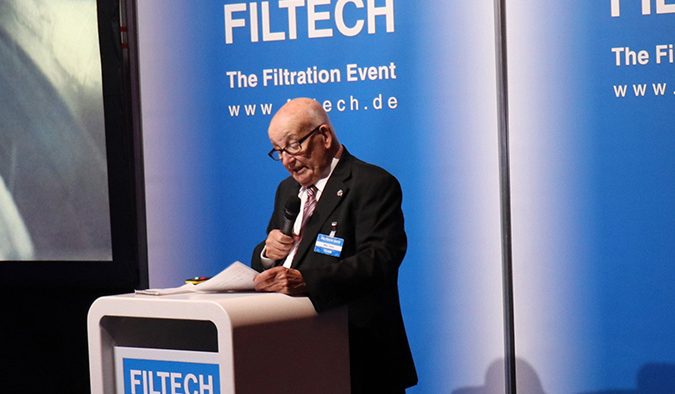
Motion and control technologies leader Parker Hannifin, for example, employs some 58,000 people at over 100 divisions worldwide, with sales in 2018 of $14.3 billion. Further, it has approximately 450,000 customers who purchase its products throughout virtually every significant manufacturing, transportation and processing industry.
Advanced algorithms
Jagan Gorle, from Parker Hannifin’s Filtration Group, outlined the company’s comprehensive approach to new filter media development, specifically in relation to the creation of analytical models for two-layer products consisting of both coarse and fine layers. A theoretical analysis of both layers and the effectiveness of their combination is first performed, with the findings validated using computational flow dynamics (CFD). The CFD analysis is based on the transient turbulence modeling of the flow through the media and considers the effect of both temperature and flow rate on filtration efficiency.
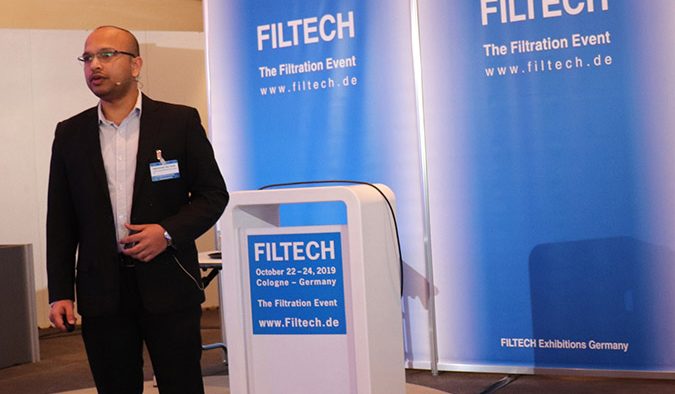
“The flow intricacies and uncertain boundary conditions are reflected more in the case of double-layered media which caused the theory to deviate from experimental and computational results,” Gorle said. “The huge gain in the filtration performance with double-layered media is penalized by increased pressure drop compared to single layers.”
In a second step, multi-objective optimization of the media’s performance is carried out by taking its packing density, thickness of the element in flat sheet form and fiber diameter as decision variables.
“Advanced algorithms can generate the best design solutions,” Gorle concluded.
Virtual development
With sales of around $4.3 billion in 2018, the family owned Mann+Hummel Group, headquartered in Ludwigsburg, Germany, is a world leader in liquid and air filters, intake systems and cabin filters and its well-known Mann-Filter brand product portfolio consists of some 4,600 filter types for more than 225,000 separate applications.
It is currently involved in a range of activities in the fields of electric vehicles and modern drivetrain concepts, as well as outside air quality, and the company had an extensive display of new developments on show at Filtech 2019.
Mann+Hummel’s Thomas Gose said that while development cycles are getting shorter and time-to-market is key, augmenting conventional filter media development with sophisticated computational methods has great potential to address current and future needs.
“Over the past decade, computer simulation of the loading kinetics at the microscale level has evolved into a powerful tool for the development of future generations of filter media,” he said. “This is becoming increasingly essential to achieve the desired filtration performance, to improve energy consumption and to detect cost savings. The valuable insight offered by virtual filter media development provides details of the filter media design and filtration performance, enabling the development of innovative virtual filter media prototypes.”
He outlined how, starting from a reference material structure based on micro-computed tomography, the derivation and validation of a virtual fiber model is arrived at, which in turn is computationally investigated and optimized.
“Hidden potentials are revealed, and we are able to identify optimized virtual filter media design concepts for specific objectives, such as filter lifetime enhancements or cost savings,” he concluded.
“Over the years several technical options, ranging from textile-based reinforcements to surface coatings, have been promoted by filter cloth manufacturers and adopted by the market in various industries,” de Angelis said. “Among their major drawbacks are the creation of an over-thickness that might not be accommodated within the equipment design, or poor resistance to withstand aggressive chemical environment. BlueTes, selectively applied, is a highly effective new solution.”
Ultipleat
Pall Corporation is another huge industry player, which during 2015 was acquired by Washington-headquartered Danaher for $13.8 billion. Danaher is a global science and technology organization employing 71,000 people, with sales in 2018 of $19.9 billion.
Dominik Steinberger of Pall introduced the company’s latest cartridge-type Vector filter designed to replace traditional bag filters, for significant performance improvements.
The key to it is what the company calls Ultipleat technology, in which the pleats are tilted and partially laid over each other to fill more space within the overall structure. In addition, Vector filters have greater rigidity than filter bags and their reinforced sliding flanges and elastomer gaskets are a response to issues related to poor sealing in bag filters.
“The media is the core of everything,” Steinberger said. “This advanced filter technology allows for the filtration of an extended range of viscosities, while minimizing differential pressure, resulting in reduced energy losses and operational costs.”
Zero emissions
Hans-Jörg Imminger, of the leading German nonwoven filter media manufacturer BWF Envirotec, outlined how his company is getting close to achieving zero fine dust emissions in industrial filtration.
The company has engineered a highly versatile ePTFE membrane coating called PM-Tec, which is being applied to nonwovens. Because the membrane is a derivative of non-sticking chemicals, its surface is slick, making bag cleaning more complete and requiring less energy. The membrane is microns-thick and laminated to the dirty-air side of the fabric felt to capture dust, keeping it from getting into the fabric felt.
A main advantage of PM-Tec is its impact on the baghouse’s differential pressure (dp) at start-up, with a higher resistance to flow compared to a non-laminated fabric. As a consequence, the start-up dp is higher, but the dp over the life of the filter will be lower and consistent. This is a direct result of the membrane’s ability to capture dust on the surface and prevent the filter from becoming blinded from dust penetration into the fabric.
BlueTes
Another family-owned company is Testori, based in Novate Milanese, Italy, which has developed a new aliphatic polyurethane resin called BlueTes, which acts as an impermeable and chemically resistant anti-abrasion coating on media.
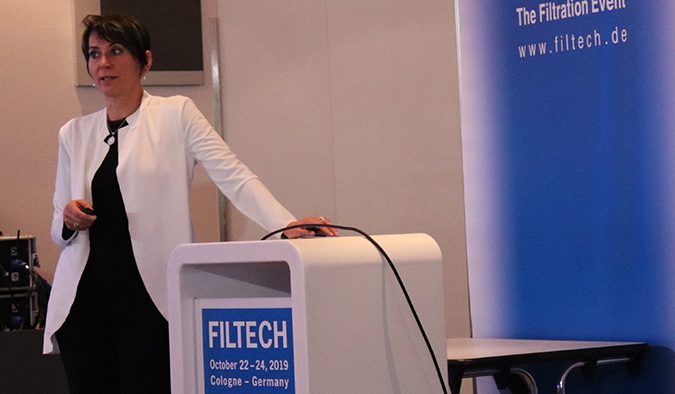
Daniel de Angelis of the company explained that abrasion is among the more critical factors affecting the useful operational life of a filter cloth installed on a filter press, especially in the mining and metal refining industries where solid-liquid separation is performed. This is due to an aggressive chemical environment and the physical nature of the suspended solids in the inlet sludge. The further crystallization of dissolved solids also contributes to the potential mechanical failure of the filter media. Abrasion is more likely to occur in correspondence to specific localized areas of the filter cloth.
“Over the years several technical options, ranging from textile-based reinforcements to surface coatings, have been promoted by filter cloth manufacturers and adopted by the market in various industries,” de Angelis said. “Among their major drawbacks are the creation of an over-thickness that might not be accommodated within the equipment design, or poor resistance to withstand aggressive chemical environment. BlueTes, selectively applied, is a highly effective new solution.”
Sinterflo FMC
Media based on various metals were high on the agenda at FILTECH, and a leader in this field is Belgium-headquartered Bekaert, which has been working with UK-headquartered Porvair on a new product called Sinterflo FMC.
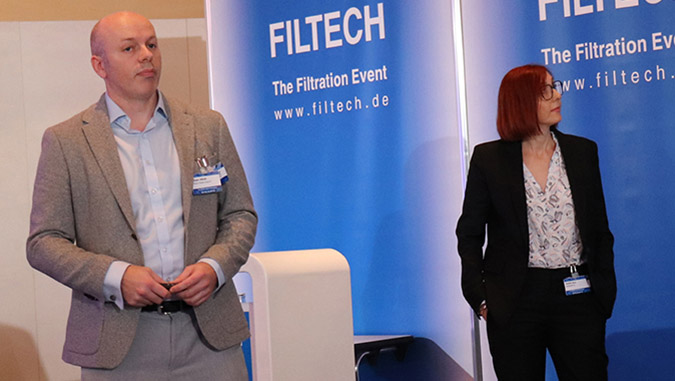
Bryan Allbut of Porvair explained that it was developed in response to a request from an existing rotary kiln exhaust gas application, where there had been problems with the use of ceramic filter breakages. It is described as a “true composite material” combining the benefits of both sintered metal fiber and precision woven mesh. It is composed of random fiber webs and woven mesh structures that are sintered to form a homogenous yet multiple layered structure, designed to deliver performance, strength and practicality in cleaning.
“Controlling the thickness of the fine fiber at the flow inlet face ensures the permeability is maximized whilst providing a surface capable of rapid filter cake development,” explained Bekaert’s Aurelie Goux. “The asymmetric pore structure provided by this material is critical to the development of the filter cake and the in-situ ability to clean through pulsejet operation. A coarse fiber structure embedded within the composite promotes a high integrity sintered interface along with a more open structure to provide flow distribution in operational flow direction and diffusion in the reverse direction when cleaning.”
“Sinterflo FMC is now providing a solution at lower capital cost and reduced element weight, with no internal support cage necessary,” Allbut added.
Three-in-one
Finally, in considering material combinations for filter media, a product combining both wovens and nonwovens, as well as metallic wire mesh layers, has been introduced to the market by Spörl, based in Sigmaringendorf, Germany.
The company’s Martin Müller said that new Compomesh is aimed at hot gas, dedusting, melt and exhaust particulate filtration applications, with its nonwoven surrounding a woven fabric and protecting it from blocking, while the wire mesh layer ensures mechanical stability.
“Metal wire meshes have a particularly high selectivity in particle separation and are robust and durable,” he explained. “Compomesh provides increased dirt holding capacity and an increased lifetime due to its unique structure.”
A review of the highlights from FILTECH 2019’s more than 400 exhibitors will be published in the next edition of International Filtration News.