In the dynamic and global filtration industry, news and information is breaking on a daily basis. International Filtration News is tracking stories relevant to our industry from air and gas filtration to liquid filtration and the various end-uses for filtration technology. Here we will post news stories relevant to filtration and its downstream applications on an ongoing basis. Please check back for regular updates. If you have news that you feel should be added to this summary report, please email it to Ken Norberg: ken@filtnews.com
Most recent update: October 30, 2023
Koch Separation Solutions Rebrands as Kovalus Separation Solutions
Sun Capital Partners, Inc. (Sun Capital), a leading private investment firm focused on defensible businesses in growing markets with tangible performance improvement opportunities, announced its affiliate has completed the acquisition of Koch Separation Solutions, a subsidiary of Koch Industries, Inc.
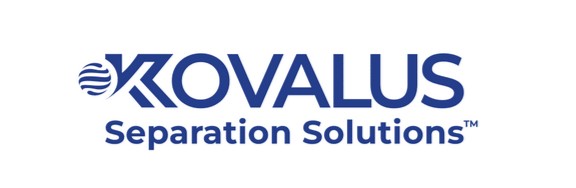
Koch Separation Solutions officially assumes its new name and brand, Kovalus Separation Solutions™. Kovalus continues its operations, now as a standalone business, under the existing management team. Kovalus was founded in 1963 and is headquartered in Wilmington, Massachusetts with over 700 employees across several global offices and four manufacturing sites. It provides membrane filtration, ion exchange, evaporators, dryers, and proprietary cheesemaking technologies to the industrial, food, beverage, dairy, and other markets.
Delbag and Nordic Air Becomes Hengst Filtration
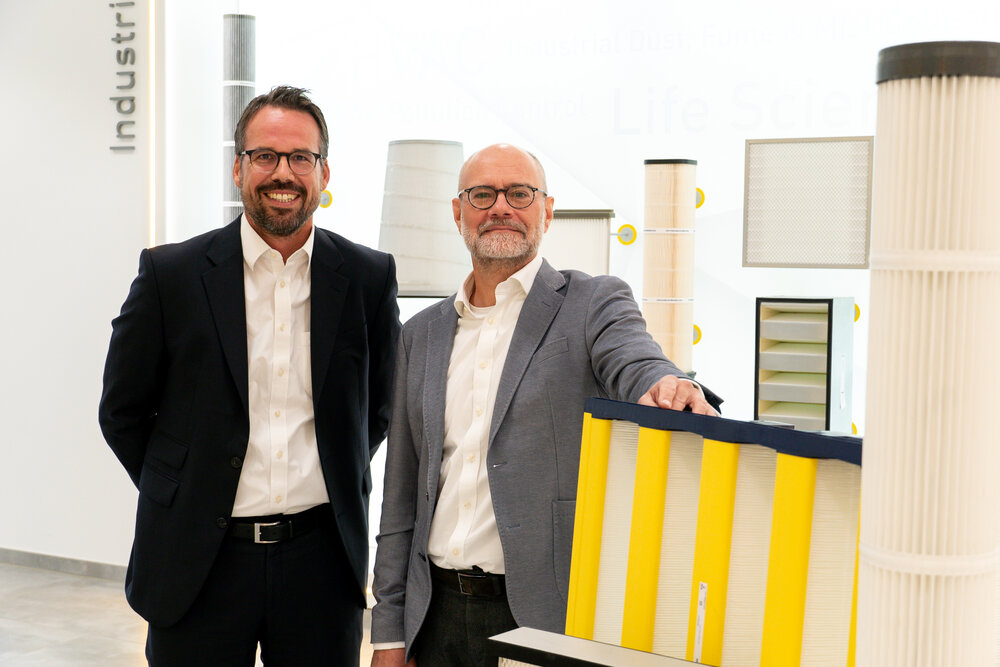
Hengst is consolidating its expertise in the field of industrial air filtration and is bringing together the two brands DELBAG and Nordic Air Filtration under the umbrella brand Hengst Filtration. “With the know-how of DELBAG and Nordic Air Filtration and the resources of the entire Hengst Group, we are developing pioneering solutions for state-of-the-art air filtration. The Hengst Filtration brand will also stand for quality, innovation and commitment in the field of air filtration – for a clean future and a pure planet,” explains Christopher Heine, CEO of Hengst SE.
In recent years, DELBAG and Nordic Air Filtration have already embarked on a common mission, namely to develop sustainable and energy-efficient products. ’DELBAG’s new HEPA filters MacroPur PRO and AbsoPur PRO have a significantly lower differential pressure, reducing energy costs in operation by up to 40% compared to other models. In addition, DELBAG uses Nordic Air Filtration’s filter cartridges in its dust collectors, increasing uptime through improved dust removal.
In applications with high demands on air quality for employees and processes, such as in the food industry or various industrial processes, different filter efficiency grades and housing designs are necessary. The DELBAG portfolio focuses on the development of pocket filters, compact filters and activated carbon filter cartridges as well as industrial extraction systems and air intake systems. Nordic Air Filtration concentrates on the development of static and pulse filter cartridges with a wide range of filter media. By consolidating this experience, customers benefit from a full range of products from a single source.
North American Filtration Enhances Green Solutions with Acquisition of Filtrex Incorporated
North American Filtration (NAF), a leading manufacturer and distributor of commercial pool filtration, chemical feed equipment and chemicals, announced the acquisition of Filtrex Incorporated. Filtrex is a prominent manufacturer of regenerative media filter systems and components.
The integration of Filtrex’s filtration technology embodies NAF’s commitment to delivering industry-leading, eco-conscious solutions. “This acquisition marks a new era of innovation and reinforces our shared commitment to a greener future,” said Chris Tedeschi, President of NAF’s Aquatics Division.
Ron Neugold, former President of Filtrex, expressed enthusiasm for the acquisition, stating, “We are thrilled to have Filtrex join the NAF family of companies. We believe that the combined knowledge, expertise, and resources will lead to continued product innovation and customer satisfaction.”
NAF has a well-established dedication to providing customers with the most advanced and efficient liquid filtration and separation technologies.
Madison Names Jonathan M. Pratt to lead Filtration Group
Madison Industries, one of the world’s largest privately held companies, announced that it has named Jonathan M. Pratt President and CEO of Filtration Group. As CEO, Pratt will partner with the Filtration Group team to establish a growth culture and drive operational excellence as the organization continues its mission to make the world safer, healthier and more productive.
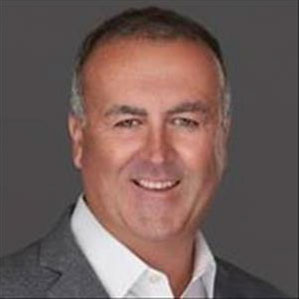
“Finding a talent like Jon is rare,” said Madison founder and CEO Larry Gies. “Jon is a proven business builder who has successfully built great organizations in the life science and filtration markets. He is passionate about coaching leaders and building something that will long outlast him.”
Prior to joining Filtration Group, Pratt served as senior vice president of the ~$2.5 billion Waters Division of Waters Corporation (NYSE: WAT), an analytical laboratory instrument and software company. Prior to joining Waters, he led Danaher’s Beckman Coulter Life Sciences operating company, a leading provider of instruments and services to the life science research and industrial markets with revenues of over $1 billion. At Pall Corporation, Jon was responsible for a $0.5 billion global portfolio of food & beverage, laboratory and bioprocessing filtration and instrument solutions.
Sun Capital Purchases Kovalus Separation Solutions
Sun Capital Partners Inc., a private equity firm focused on defensible businesses in growing markets, has purchased Koch Separation Solutions, a subsidiary of Koch Industries Inc., and rebranded the business to Kovalus Separation Solutions.
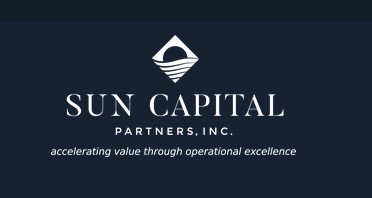
Kovalus was founded in 1963 and is headquartered in Wilmington, Mass. with over 700 employees across several global offices and four manufacturing sites. It offers membrane filtration, ion exchange, evaporators, dryers and proprietary cheesemaking technologies to the industrial, food, beverage, dairy and other markets. The acquisition of Kovalus by Sun Capital’s affiliate paves the way for Kovalus to strengthen its market presence and improve its economies of scale.
Medicom Inaugurates New Mask Filter Plant in Canada
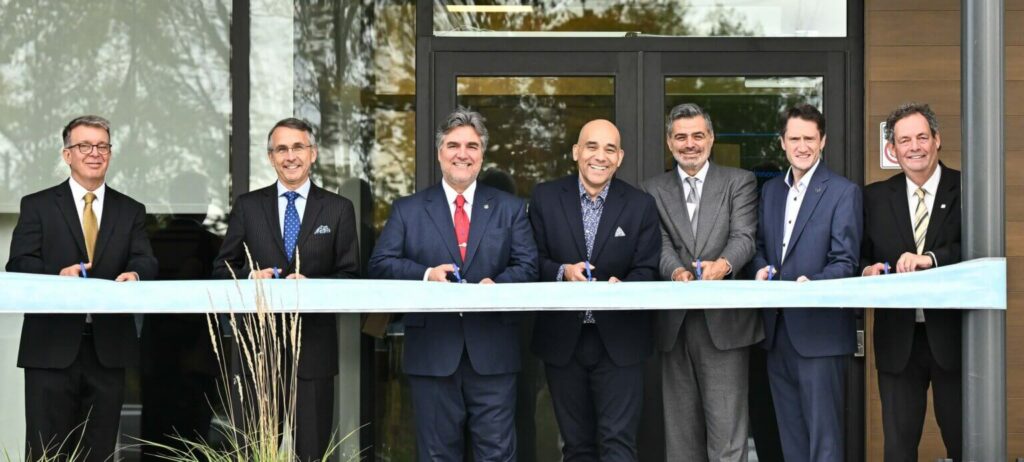
Medicom Group, one of the world’s leading providers of infection prevention and control solutions, celebrated the official inauguration of its new mask filter plant, Meltech Innovation in Saint-Eustache, Canada. The meltblown polypropylene component of surgical and respiratory masks, which acts as a filter for harmful particles, will be the plant’s main output.
The total investment of close to $50 million, will also create 26 skilled jobs. Meltblown polyproplylene was one of the materials facing a worldwide shortage during the pandemic. Given the highly strategic nature of the project, the Government of Canada has committed to investing up to $29 million through the Strategic Innovation Fund.
“The construction of our new mask filter plant represents another important milestone in our vertical and sustainable integration strategy. Once operational, this critical component that we have mostly imported from Europe up till now will travel only 30 km from Saint-Eustache to be transformed into face and respiratory (N95) masks in Montreal. This means that Medicom will be able to offer the same protection so appreciated by our healthcare providers, but with a significantly reduced environmental impact,” said Guillaume Laverdure, CEO of Medicom.
Attached to the plant is a unique innovation center with a main focus on designing the next generation of greener, more sophisticated, and more efficient filters in terms of breathability and protection. However, R&D for medical purposes will only be part of the output as Meltech will also develop products that can be used for air filtration, membrane filtration, battery separators, supercapacitors and more. All of this will be done with a view to marketing and exporting.
Parker Hannifin Exceeds Emissions Reduction Target
Global air filtration expert Parker Hannifin unveiled exceptional results from its carbon reduction strategy with the first full year of implementation showing substantial savings. With an ambitious goal of reaching carbon neutral operations by 2040, last year Parker Hannifin established a year-on-year emissions reduction target of 3% from a 2019 benchmark. Parker Gas Turbine Filtration has slashed emissions by 13% in just the first year under its enhanced Environmental, Social and Governance (ESG) plan.
As part of this overarching strategy, Parker Hannifin created performance metrics around each individual division, for the gas turbine business for example, empowering them to drive positive change in the transition to net zero carbon.
Exploring different projects to achieve this goal, one significant measure adopted in FY 2023 was to install a new roof at the Parker Hannifin manufacturing facility in Alton, U.K. This resulted in a substantial reduction in gas and energy consumption. Furthermore, as part of this project a secondary layer was added to the existing roof, improving the building’s overall energy efficiency.
Some of the energy efficiency improvements also extend to the filter manufacturing process itself with tightly controlled temperatures for glue points and using automatic timers rather than working 24 hours a day as was the case previously. Lowering the set point on air compressors so that they work optimally has also resulted in savings. Furthermore, energy monitoring and data loggers across the distribution system allows Parker Hannifin to identify where further savings may be achieved in the future.
The results speak for themselves. The emissions baseline in 2019 was around 946,000 tonnes of CO2e equivalent across the Division. The policy was introduced at the start of the last financial year in July 2022 and for 2023, the first year of implementation of the strategy, that figure was already down to 823,000 tonnes CO2e, about a 13% reduction.
University at Buffalo: Researchers Develop Heat-Resistant Nanoporous Membrane
Industry has long relied upon energy-intensive processes, such as distillation and crystallization, to separate molecules that ultimately serve as ingredients in medicine, chemicals and other products.
In recent decades, there has been a push to supplant these processes with membranes, which are potentially a lower-cost and eco-friendly alternative. Unfortunately, most membranes are made from polymers that degrade during use, making them impractical.
To solve this problem, a University at Buffalo-led research team has created a new, sturdier membrane that can withstand harsh environments — high temperatures, high pressure and complex chemical solvents — associated with industrial separation processes.
Made from an inorganic material called carbon-doped metal oxide, it is described in a study published Sept. 7 in Science.
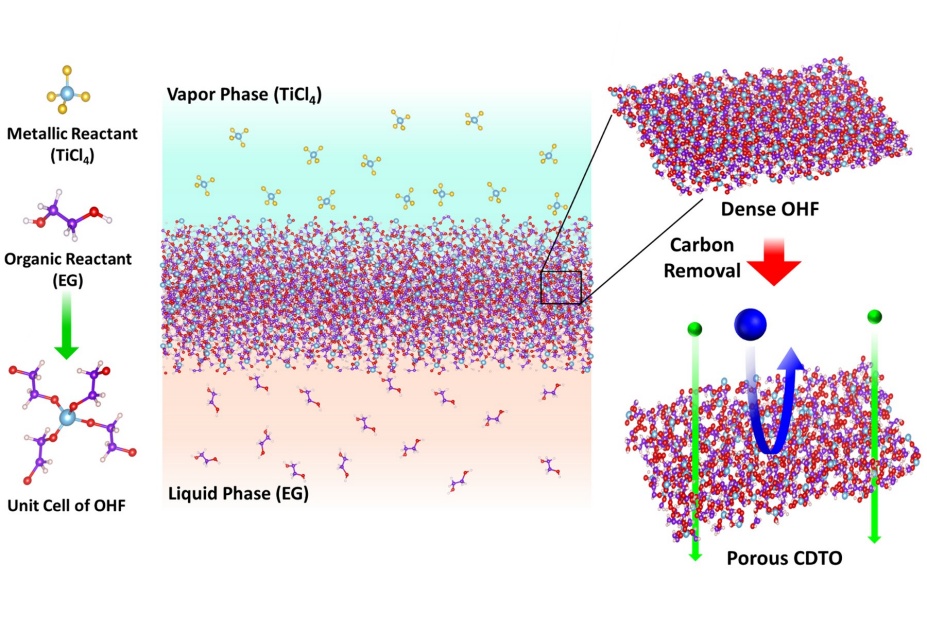
“The processes of separating molecules — whether for water desalination, the production of medicine or fertilizers — use an incredible amount of energy,” said corresponding author Miao Yu, SUNY Empire Innovation Professor in the Department of Chemical and Biological Engineering, School of Engineering and Applied Sciences.
“What we have developed is a technique to easily fabricate defect-free, strong membranes that have rigid nanopores that can be precisely controlled to allow different-sized molecules to pass through,” adds Yu, a core faculty member in the UB RENEW Institute.
To create the membrane, the research team took inspiration from two common, but unrelated, manufacturing techniques. The first is molecular layer deposition, which involves layering thin films of materials and is most often associated with semiconductor production. The second technique is interfacial polymerization, which is a method of combining chemicals that is commonly used to create fuel cells, chemical sensors and other electronics.
“These methods are not new,” says Sengupta, “however the manner in which we apply them is, and that is the key to creating our new nanoporous membranes.”
In experiments, researchers merged two low-cost reactants — liquid ethylene glycol and gaseous titanium tetrachloride — on an aluminum-based support. Within minutes, the reaction created a thin-film.
To create the nanopores, they applied heat to the film. The heat burns off carbon, creating tiny, microscopic holes for molecules to pass through. The size of the nanopores can be anywhere from 0.6 to 1.2 nanometers in diameter — as determined by the calcination gas environment, as well as the amount and duration of heat.
The method allows researchers to avoid a nagging problem — small holes merging into larger ones, thus making them more porous than intended — with creating polymer-based membranes.
FiltXPO™ 2023 Brought the World of Filtration Together for New Technologies and Innovations
INDA, the Association of the Nonwoven Fabrics Industry, announced that C-suite leaders and product developers convened October 10-12, Chicago, IL for the third edition of FiltXPO™. FiltXPO is an exhibition and technical conference dedicated exclusively to filtration and separation products and processes. Leading-edge exhibitors displayed their products and services to technology scouts and business developers.
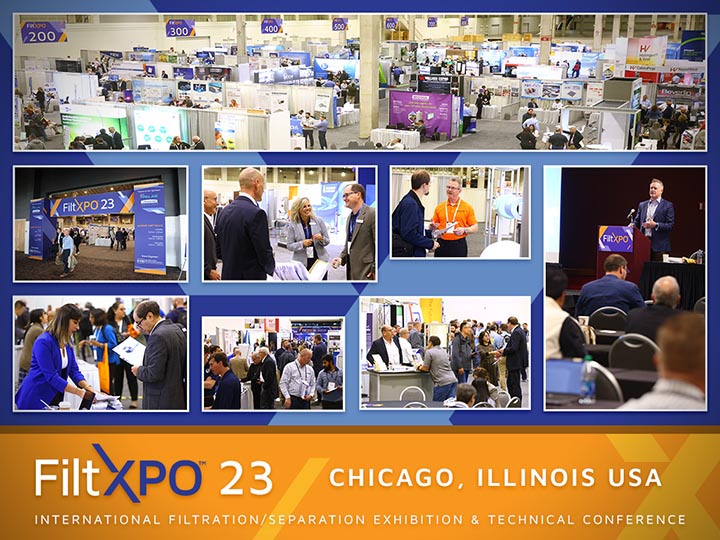
The technical conference highlighted key topics affecting the filtration industry today and for the future and was co-organized by the Waterloo Filtration Institute. The conference featured sessions on filter media technologies, advancements and opportunities in filtration machinery and equipment, innovations in clean air for homes and urban areas, standards and testing, industry trends and new developments, and filtration challenges and opportunities.
The two-day Filter Media Course, conducted by Behnam Pourdeyhimi, Ph.D., Professor and Executive Director, The Nonwovens Institute; Hechmi Hamouda, Ph.D., Professor Textile Engineering, NC State University (ret.); and Hooman Tafreshi, Ph.D., Associate Professor Mechanical and Aerospace Engineering, NC State University, allowed participants to develop an overall understanding of nonwovens and their applications in air, liquid, and aerosol filtration, technologies, unmet needs, and trends for future development.
The next edition of FiltXPO and the Filter Media Course will be co-located with IDEA®, taking place April 29-May 1, 2025, Miami Beach, FL. More information will be available January 2024.
Almina to Use Metso Technology for Copper and Zinc Concentrator in Portugal
Almina Minas do Alentejo S.A. is proceeding with the preparations to upgrade the copper and zinc concentrator at their Almina mine in Aljustrel, in the Iberian pyrite belt in Portugal. The company placed an order with Metso as the key equipment supplier for this project in the first quarter of 2023.
Metso has now completed the basic engineering of the grinding island. Delivery of the concentrator plant equipment will take place around the end of the second quarter in 2024, with the project expected to be commissioning by the end of the first quarter of 2025.
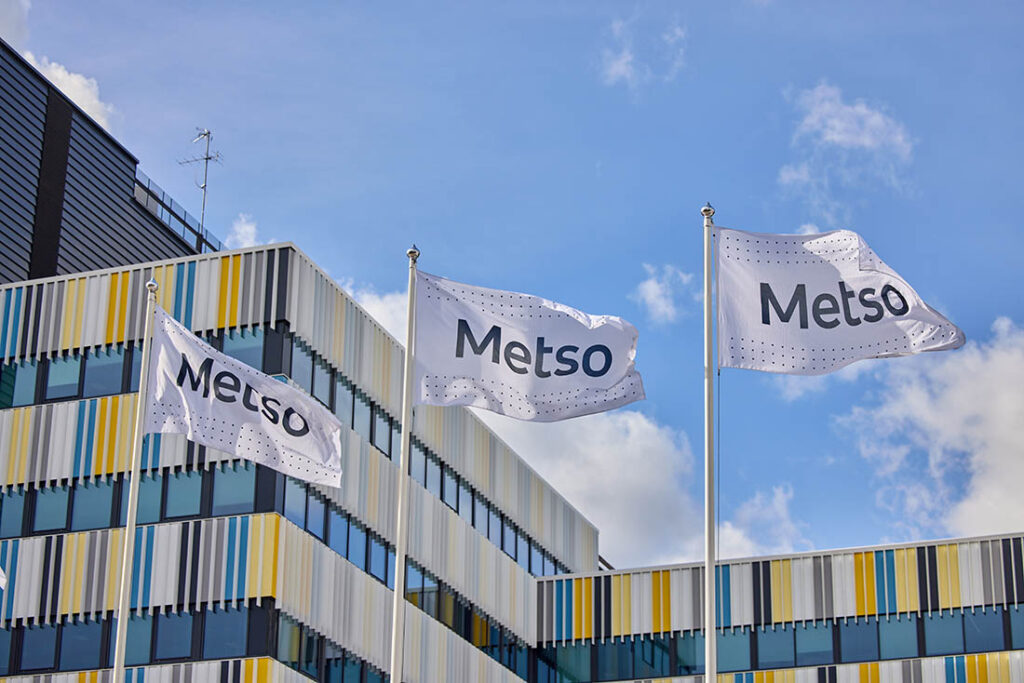
“Collaboration between Almina Minas do Alentejo S.A and Metso is strong. We are excited to continue working with Almina on this project, for which they selected us to supply the grinding island, ultra-fine grinding technology, as well as flotation, filtration, and thickening equipment, as well as all slurry pumps. The deliveries will be fast as the plant will be built already within the next 24 months,” explains Saso Kitanoski, President for Metso’s Europe Market Area.
According to Miguel Santos, Senior Sales Manager for Metso Minerals in Iberia & Italy, Almina chose to collaborate with Metso on the engineering for the grinding island as Metso was able to bring extensive expertise and confidence that the project will deliver robust performance, availability, and sustainability results. “Almina trusts Metso as a partner for this project as we can provide them with a comprehensive package of solutions to help them achieve their targets. Several of the solutions to be delivered to Almina feature our Planet Positive technology.”
Carlsberg Wins Global Industrial Water Reuse Award
Carlsberg Group, leveraging water technologies from DuPont, was awarded the Global Industrial Water Reuse Champion Award for its water recycling plant and commitment to water reuse and recycling in its brewing processes.
Using DesaliTec™ closed circuit reverse osmosis (CCRO) technology as part of its total water management (TWM) treatment plant, Carlsberg Group reduced water consumption by 58.8 percent—or 500,000m3 per year—virtually eliminating wastewater from the water-intensive brewing process at its flagship brewery in Fredericia, Denmark.
Carlsberg’s total water management system project, which recycles the non-ingredient water used for cleaning and other industrial processes, was led by the Belgian circular water specialists, Pantarein Water and included expertise and technologies from Dutch water treatment system designer Lenntech, DuPont Water Solutions, and Danish industrial pumps specialist Grundfos.
Evonik Expands Production Capacity for Gas Separation Membranes
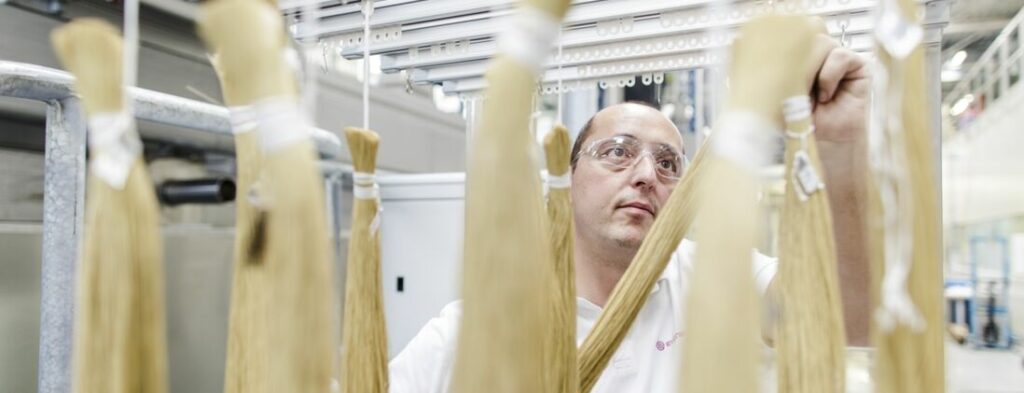
Evonik will expand capacity for production of its SEPURAN® hollow fiber membranes in Schörfling and Lenzing, Austria. The specialty chemicals company already put into operation a new hollow fiber spinning facility in Schörfling at the beginning of the year. On the occasion of the ceremonial opening of this plant, Evonik Chief Executive Officer Christian Kullmann announced the construction of a further production line: “We are going full throttle for the green transformation and are investing a mid-double-digit million euro amount as the next step to grow our membranes business.” Construction in Schörfling and Lenzing is scheduled to start in early 2024, with completion planned for the first half of 2025.
The growth of the membrane business clearly follows the Group’s strategy. “We invest in innovative green technologies that offer superior sustainability benefits to our customers,” says Kullmann. “The dynamic development of the membrane business shows that the green transformation is underway and that we are playing a key role in it.” By 2030, Evonik aims to increase the proportion of revenue generated by Next Generation Solutions to more than 50 percent from currently 43 percent. Next Generation Solutions are products with demonstrably superior sustainability benefits.
With membranes for the treatment of biogas and the extraction of hydrogen, for example, Evonik is making an important contribution to the defossilization of the energy industry. The trend towards renewable energy is driving the steadily growing demand in the membrane business.
At the heart of Evonik’s SEPURAN® membrane technology are fine hollow fibers made of a high-performance polymer specially developed by Evonik that is highly resistant to pressure and temperature. The upcoming capacity expansion includes construction of an additional plant for spinning hollow fibers and the expansion of the infrastructure necessary for producing membrane modules at the Schörfling site. The neighboring site in Lenzing will expand production of the required raw material (high-performance plastic).
The Nonwovens Institute Expands ISO-Accredited Filtration Testing Lab
The Nonwovens Institute (NWI) announced its newly expanded Filtration Testing Lab, featuring services for facemasks and respirators, along with filter media for automotive, HEPA and HVAC applications.
Importantly, NWI’s Filtration Testing Lab is A2LA Accredited for ISO 17025*, enabling it to meet NIOSH requirements for testing materials used in respirators, and it is outfitted with equipment to perform ASTM F2299 testing for the measurement of Particle Filtration Efficiency (PFE) at 0.1 microns.
In addition to NWI’s Filtration Testing Lab, NWI offers a fully equipped Analytical and Physical Testing Lab with more than 60 tests available for nonwoven materials. NWI also offers lab- and pilot-scale capabilities for Fiber Spinning, Meltblown, Spunbond and Hydroentangling, Staple/Carded Nonwovens, among others.
NWI will be exhibiting at FiltXPO™ 2023, Oct. 10-12, Navy Pier in Chicago. Visit NWI at Booth No. 826 to learn more about its Filtration Testing Lab and capabilities.
Metso Signs EUR 85 Million Contract Copper Concentrator to Kazakhstan
Metso has signed a contract for the delivery of a new copper concentrator to be built in Kazakhstan. The order value of approximately EUR 85 million is booked in the Minerals segment’s third-quarter 2023 orders received.
Metso’s scope of delivery consists of the main process equipment for grinding, flotation and dewatering and includes HIGmill® high-intensity grinding mills, TankCell® flotation cells in different sizes in the 30 to 630 cubic meter range, Larox® PF pressure filters, HRT High-Rate Thickeners, an on-line sampling and analyzing system, as well as field instrumentation and Proscon® automation for the whole concentrator plant.
The flotation cells, pressure filters and high-rate thickeners are part of the company’s Planet Positive portfolio, thanks to their superior energy and water efficiency.
Finish Thompson Acquires Penguin Pumps Inc.
Finish Thompson, Inc. is announced the acquisition of Penguin Pumps, Inc., parent company of Filter Pump Industries.
Penguin Pumps is a 24-person company based in southern California. They manufacture corrosion resistant pumps, mixers, filter systems, and filter chambers primarily used in the surface finishing, chemical processing, and chemical manufacturing industries.
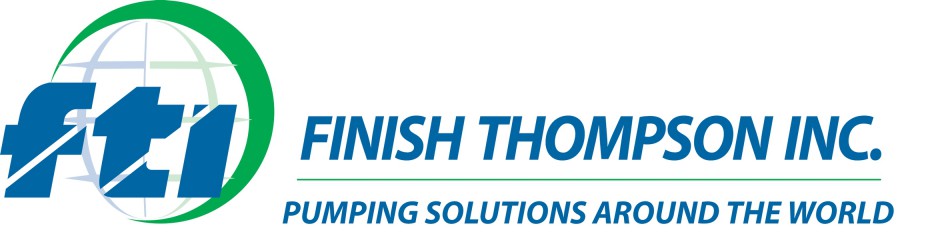
“As family-owned businesses, Finish Thompson and Penguin Pumps share many of the same values, including a focus on employees, quality products, and customer satisfaction,” said Casey Bowes, CEO of Finish Thompson. “With this purchase, we are able to maintain these values across both companies while also opening up new areas of growth for Finish Thompson’s own pump products.”
The purchase of Penguin Pumps will give Finish Thompson a full offering of filtration systems, supported by Finish Thompson’s quality range of mag-drive centrifugal pumps. Additionally, Penguin Pump’s vertical plastic pumps and tank and drum mixers perfectly complement Finish Thompson’s line of horizontal centrifugal pumps, air-operated double diaphragm pumps (FTI Air), and drum pumps.
Rensa Filtration buys Smith Filter
Rensa Filtration, a manufacturer and distributor of consumable, mission-critical air filtration products, announced that it recently completed the acquisition of Smith Filter, based in Moline, IL. This acquisition expands Rensa’s product portfolio into metal air filters. Smith’s metal filters help protect equipment and processes in commercial and industrial filtration applications involving high temperatures and harsh environments.
“I am pleased that Sharilyn, Jim and Matt Solis and the Smith Filter team decided to partner with Rensa to support the next phase of growth for their company,” said Brandon Ost, CEO and Founder of Rensa Filtration. “Smith Filter is an iconic brand known for high quality metal air filters. I want to thank Sharilyn and Jim for their leadership and commitment to the air filter industry and wish them well in their retirement.”
Matt Solis and his management team will continue to lead the Smith Filter business and manufacturing operations in Moline.
Smith’s metal air filters represent another key category in Rensa’s growing offering of specialty air filters. In addition to pleated filters, bag filters, high-capacity filters and high efficiency filters used across many applications, Smith metal filters will complement Rensa’s Permatron® brand of low-pressure drop intake filter screens and Rensa’s D-Mark® brand of activated carbon filters used in odor and pollution control applications.
Smith Filter represents Rensa’s tenth acquisition, and the fifth acquisition under Audax Private Equity since the firm’s investment in 2022.
NX Filtration Supplies Beer Filtration Membranes to Carlsberg Fredericia in Denmark
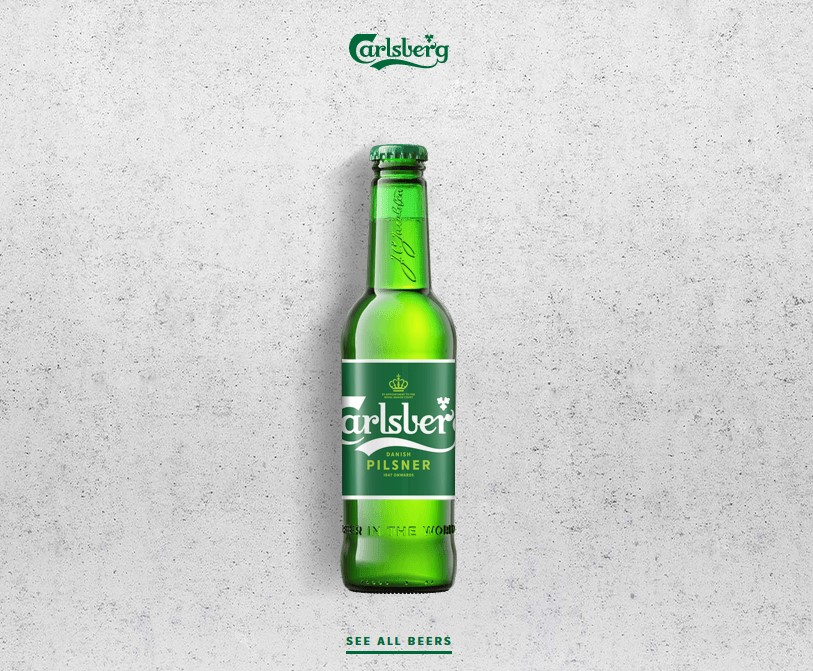
NX Filtration, the global provider of breakthrough filtration technology, has supplied its membranes to Carlsberg’s Fredericia brewery in Denmark, one of the largest breweries in Europe, that has a strong focus on process optimization and sustainability. NX Filtration’s microfiltration membranes are being used to further improve performance and sustainability of Carlsberg’s flagship brewery.
NX Filtration is among the few suppliers of hollow fiber microfiltration membranes to the beer industry globally. Microfiltration offers a superior alternative for traditional filtration method (diatomaceous earth) because of its higher and more constant quality, lower energy use, the possibility of continuous operation and the avoidance of environmental impact.
For Carlsberg’s Fredericia brewery, NX Filtration supplied its microfiltration modules to further optimize the beer filtration process in the brewery. NX Filtration’s membrane modules offer the highest quality and unique characteristics in terms of robustness, energy and chemical consumption, costs, and operability and handling.