“Swiss precision” is the proud claim made by G Bopp + Co AG, first established in 1881 in Eastern Switzerland. This family business, now into its fourth generation, remains true to its location in Switzerland to this day.
Originally manufacturers of coarse wire mesh, the business has transformed over the decades to ever finer woven wire cloth, where individual wire diameters can measure less than 15 microns. A significant milestone on this path was the development of micronic filter meshes for the Apollo space program. Demonstrating advanced levels of innovation, G Bopp + Co AG succeeded in meeting these new challenges, working within a very limited timeframe. For some 50 years now, on every mission, 760 metal filters made of Bopp mesh have gone into space aboard the Saturn V rocket; they appear to have mastered their task brilliantly. Bopp continues to supply the aerospace industry, but this is just one of many industry sectors supplied by the company. Bopp products are used in biotechnology and the pharmaceutical industry, in the automotive industry, in environmental technology such as solar and fuel cells, in screen printing, in acoustics and so many more applications.
The production of such fine wire cloth is particularly challenging in terms of raw materials. Only the highest quality molten metal can be used by Bopp‘s in-house wire drawing plant Filinox to draw wires, which measure only a fifth the thickness of a human hair. With Filinox an integral part of the business, Bopp is the only wire weaver in the world to operate its own wire drawing plant.
Today, Bopp is one of the world’s leading manufacturers of woven wire cloth. While earlier sales of the products in roll form were more prevalent. Today it is far more likely to be fabricated products, developed and produced working in close cooperation with individual customers. The product portfolio includes a comprehensive range of single layer filter media as well as the increasingly popular sintered meshes, where carefully selected mesh types are combined and bonded using heat and pressure. This process combines the advantages of each individual mesh layer and achieves the finest filtration results while achieving high levels of resistance to physical load.
In this issue of IFN, we interview Peter Bopp, president of the Board and CEO at G Bopp, to learn more about what has led to this company’s success over its many years in business.
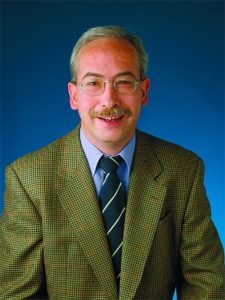
Ed Gregor: It seems to me G Bopp & Co. has for decades had the reputation as one of the few global performance quality weavers of wire cloth. Is this still the case?
Peter Bopp: More than ever! I’m proud to see the progress we’ve made over the past years. Continuous investment in all areas of the business is paying off, and we remain committed to maintaining our leading edge. We have established a strong position in our own niche market, supplying primarily fine woven wire cloth and fabricated products. Over time, we have acquired significant knowledge and skills as well as establishing a considerable resource in terms of machinery and equipment.
Ed Gregor: It also appears G Bopp & Co. has morphed itself with primary emphasis on weaving to supplying both wire cloth and fabricating downstream parts. Is that a fair statement?
Peter Bopp: Our business has changed considerably over recent years. Weaving remains a vital core competence. However, our strategic direction means that we have added to our strengths. Primarily this covers the professional fabrication of our wire cloths into complex finished filter modules, designed in seamlessly to the manufacturing processes of our customers.
Ed Gregor: What stimulated this change of direction?
Peter Bopp: Our customer expectations changed. Increasingly today, businesses are looking for reliable suppliers, with whom they can work closely as a team in terms of problem solving and who can use their competences to provide effective solutions. We recognized this situation early and transformed ourselves into just such a business partner.
We decided long ago to commit to Switzerland as our place of manufacture and to develop there. With the exception of the high costs, Switzerland’s economic advantages are considerable. We secure our competitiveness with high levels of automation, an economically advantageous environment and above all well trained people with innovative ideas.
~Peter Bopp
Ed Gregor: Does Bopp supply woven wire cloth roll stock to fabricators?
Peter Bopp: Bopp has always served this market sector, which remains very important to us. Even when we made the strategic decision to focus on fabricated products, we continued to look after this customer segment and see no negative crossover.
Ed Gregor: What categories of metal wire do you weave beyond stainless steel? Any precious metals?
Peter Bopp: That’s an easy question to answer – all metallic materials and alloys available on the market that can be woven. This includes noble metals, heat and chemical resistant alloys, special material grades and also aluminium, brass, bronze, copper, nickel and many others.
Ed Gregor: Zurich Switzerland is a high-cost city, do you have locations elsewhere and what do you see in the future?
Peter Bopp: Indeed it is. We decided long ago to commit to Switzerland as our place of manufacture and to develop there. With the exception of the high costs, Switzerland’s economic advantages are considerable. We secure our competitiveness with high levels of automation, an economically advantageous environment and above all well trained people with innovative ideas. Our success across the globe demonstrates that we have continued to achieve on this basis.
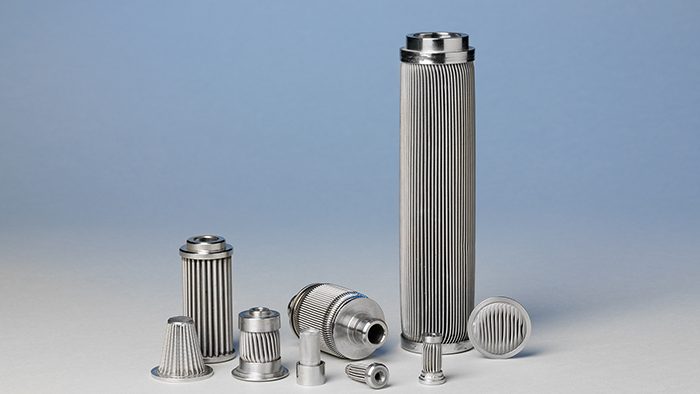
Ed Gregor: What is the Bopp’s biggest unmet need?
Peter Bopp: In today’s fast-moving world, it is a prerequisite for every business to meet continuously changing demands from customers. We are no exception to the rule. We want to become more agile and more flexible at every level, in order to fulfil new requirements as quickly as possible. This is the challenge we are always striving to meet.
Ed Gregor: Please tell us about what new resources Bopp has available.
Peter Bopp: Where should I start? We are investing at every level in order to grow. One significant current project is the expansion of one of our two weaving mills, where we are adding thousands of square metres to expand production and also to accommodate new weaving machines. These machines are completely developed and built in house. Alongside this work, existing equipment is being redesigned, rebuilt and made fit for the future.
We have also made considerable steps forward in terms of quality management. Today, we have access to measuring equipment with previously unattainable levels of precision and accuracy. I would also like to emphasise our increasing product portfolio, specifically Compomesh and Betamesh Plus, capable of even finer particulate filtration. We are just about to launch Betamesh Plus.
Ed Gregor: What do you see different or emerging in the future for wire cloth roll stock and/or fabricated parts? Please elaborate what is behind this trend.
Peter Bopp: More recently, customer relationships have been closer than ever before. We expect this trend to intensify into the future. Because product lifecycles are becoming ever shorter, we need to stay close to our customers in order to understand and fulfil their requirements, otherwise you run the risk of failing to produce for your markets. This is a real challenge for our sales team as well as for our technical personnel. Fortunately we also have a few perennially popular products, which have been in demand for many years in large quantities. We have a comprehensive product portfolio and keep on average 10,000 rolls in stock at any time. Our customers expect the quickest possible delivery times. We are committed to achieving this on their behalf.
For more information, please contact Martin Jeitler, sales manager at Bopp, at mjeitler@Bopp.ch.