In the dynamic and global filtration industry, news and information is breaking on a daily basis. International Filtration News is tracking stories relevant to our industry from air and gas filtration to liquid filtration and the various end-uses for filtration technology. Here we will post news stories relevant to filtration and its downstream applications on an ongoing basis. Please check back for regular updates. If you have news that you feel should be added to this summary report, please email it to Matt Migliore at mmigliore@inda.media.
Most recent update: March 30, 2021
Lydall reports strong fourth quarter results, driven by gains in specialty filtration business
Lydall Inc. announced financial results for the fourth quarter ended December 31, 2020, with adjusted EBITDA growing over 40% from the same period last year and strong cash flow , driven by strong demand for the company’s Performance Materials (“PM”) specialty filtration products and a sharp recovery in sealing products. Specialty filtration sales grew 51% or $11.3 million, including $5.0 million of one-time purchases related to a previously announced facility closure; sealing and advanced solutions sales grew by 17.9%.
Parts sales in the Thermal Acoustical Solutions (“TAS”) segment grew 9.4% compared to Q4 2019, and 4.1% compared to the Q3 2020.
While Technical Nonwovens (“TNW”) segment saw a sales decline of 4.1%, adjusted EBITDA margin remained consistent at 11.8%, down only 20 basis points from prior year.
“In December we communicated our strategy to deliver sustained shareholder value and our fourth quarter results represent the focus and commitment Lydall has to executing on this vision,” said Sara A. Greenstein, President and Chief Executive Officer. “Over the course of 2020 we navigated a global pandemic, a shutdown of global automotive production, ongoing supply chain disruptions, uncertain economic and political environments, and have emerged a stronger and more agile company. We will continue to execute to ensure we achieve the objectives outlined in our strategy by efficiently deploying capital to profitably grow in specialty filtration and advanced materials solutions.”
Ms. Greenstein concluded, “We anticipate continued healthy demand and order activity across all three segments as the end markets we serve recover from a tumultuous 2020. Additionally, elevated demand for specialty filtration solutions are expected to continue beyond 2021 as the structural shift towards better indoor and outdoor air quality drives further demand for these products.”
In related news, Lydall announced its Performance Materials business segment is increasing prices for its Filtration and Specialty Insulation products supplied globally. The price adjustment is driven by significant and ongoing increases in key raw material and freight costs.
“Lydall remains committed to reducing overall costs and making our operations more efficient through our One Lydall strategy and focused transformation initiatives,” said Lydall Performance Materials President Ashish Diwanji. “However, these extensive efforts are not enough to offset the sustained inflationary pressures that are widespread in today’s market. We must modify our pricing to ensure that we can continue to deliver the innovative products and high-quality, advanced materials our customers depend on to bring the world’s most essential products to market.”
Source: lydall.com
Researchers employ copper foam to filter microbes in facemasks and air filtration systems
During the COVID-19 pandemic, people have grown accustomed to wearing facemasks, but many coverings are fragile and not easily disinfected. According to research published in ACS Nano Letters, Georgetown University Department of Physics professor Kai Liu and his group of researchers have transformed copper nanowires into metal foams that could be used in facemasks and air filtration systems, which are more durable and have the potential to effectively filter out microbes.
“When a person with a respiratory infection, such as COVID-19, coughs or sneezes, they release small droplets and aerosolized particles into the air,” said graduate student James Malloy (C’22), first author of the study, “Minuscule particles can stay airborne for hours, so materials that can trap these tiny particles are ideal for use in face masks and air filters. The foams filter efficiently and can be easily decontaminated, reused repeatedly, and recycled.”
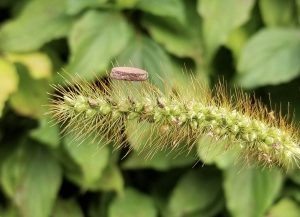
Though current filtration systems such as those in N95 masks are helpful in reducing the spread of COVID-19, the materials they are made with contain some drawbacks.
Fiberglass, carbon nanotubes and polypropylene fibers are not durable enough to undergo repeated decontamination procedures and some further rely on electrostatics that precludes washing, which leads to large amounts of waste from single-time use.
Liu’s team recently developed metallic foams with microscopic pores that are stronger and more resistant to deformation, solvents and high temperatures and pressures. As such, they wanted to test copper foams to see if they could effectively remove submicron-sized aerosols while also being durable enough to be decontaminated and reused.
Their most effective material was 2.5 millimeters thick and trapped 97% of deep submicron aerosolized salt particles, which are commonly used in facemask tests.
Read the full story: https://college.georgetown.edu/news-story/research-by-physics-professor-shows-copper-foam-could-be-highly-efficient-durable-filter-for-reusable-masks-and-air-cleaners/
Source: https://www.georgetown.edu/
Filtration business continues to perform well, as Neenah reports Q4 2020 results
Neenah Inc. reported adjusted operating income of $21 million and corresponding earnings per share of $0.87, equaling Q4 2019. Favorable results in Technical Products were partially offset by lower pricing in a few categories such as backings that have price adjusters tied to raw material input costs. Neenah’s filtration business continued to perform extremely well, and fourth quarter revenues were up almost 30% to a record $66 million.
Performance was led by the company’s Technical Products segment. With the combination of a strong market demand, new product launches and manufacturing efficiencies, this business segment increased 11% versus Q4 2019 and adjusted operating income of $18 million reached the highest quarterly level in recent history.
Market demand in Fine Paper & Packaging, as expected, had a more extended recovery curve. Neenah reported this segment remains on track to recover 90% of its pre-COVID quarterly run rate of $90 million this year.
Both business segments delivered another sequential quarter of improved sales, profits and margins, according to the company. Versus the third quarter, sales increased 8%; adjusted operating income was up by more than 30%; and adjusted earnings per share were up almost 60%.
These results were led by Neenah’s Technical Products segment, which now makes up almost 65% of total revenue. Sales of $137 million in the quarter were up from quarter three, and grew 11% versus 2019. The increase was driven primarily by volume growth and helped by currency translation as the stronger euro increased the top line by about $5 million.
Transportation, filtration media sales grew strongly in Europe and the U.S. and sales of industrial filters increased by more than 20%. Industrial filtration growth was led by gains in products used for evaporative cooling and other similar applications. Quarterly revenues also included about $4 million for facemask media, which the company began selling in 2020.
Outside of filtration, Neenah’s Industrial Solutions business also performed well with almost 20% growth in backings, primarily due to increased tape revenue with new products introduced at some of the company’s most strategic customers earlier in the year.
Source: neenah.com
AFS FiltCon 2021 releases technical conference schedule
The AFS FiltCon 2021 Conference, taking place from April 19-21, 2021, will feature two plenary presentations, 42 technical presentations, an expo and a student poster competition. New Product Awards for 2019 and 2020 and Honorific Awards for 2020 will be announced at the awards ceremony on Tuesday, April 20.
The plenary presentations are How Global Mega Trends, Particularly the ‘Race to Zero Emissions’, and COVID are Impacting the Filtration Industry from Brian Lane of Parker Hannifin’s Global Filtration Business and Impacts on Filtration Market Growth with Josh Ayer, vice president and managing direction at Hollingsworth & Vose, Americas.
Due to the virtual setting of the conference, the presentations will be available to all participants, either live or on-demand for up to two weeks post conference. Registration begins Friday, March 26.
View the full conference schedule at: filtcon.memberclicks.net/schedule
Source: afssociety.org
DuPont donates water treatment system to South African community
DuPont, in collaboration with Kusini Water and the U.S. Embassy in South Africa, donated a multi-technology water treatment plant that will provide safe, pure water to Reneilwe Primary School and the local community of Temba, Hammanskraal.
The area’s water sources are afflicted by high levels of nitrate and phosphate contaminants, making municipal water unsafe to drink. The new ultrafiltration membrane and ultraviolet light system removes impurities from groundwater pumped out of a new borehole and can supply up to 4,000 liters of healthy drinking water per hour, driven by solar power. A water kiosk has been built to dispense it to the local community and generate revenue for the school to operate the system sustainably, with five “water champions” from the community trained by Kusini Water to autonomously operate and maintain the plant.
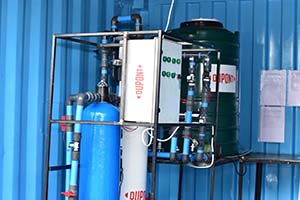
“We are delighted to be involved with such a beneficial project as this, which contributes to Sustainable Development Goal 6 – Clean Water and Sanitation,” said Semano Sekatle, regional commercial manager, DuPont Sub-Saharan Africa. “With the right partnership approach, no one in this world need suffer from a lack of safe water, as effective and highly advanced technology is available that can be community-run.”
Source: dupont.com
Veolia North America to provide sustainable power for wastewater treatment as part of Rialto microgrid project
The City of Rialto, in partnership with Rialto Water Services and Veolia North America, have announced a joint commitment to the next phase of a plan to design and install a microgrid powered through a combination of biogas cogeneration, solar power and backup battery storage to supply electricity for the city’s wastewater treatment plant.
The project, one of the first of its kind in California, is meant to bring the city greater resilience and efficiency in its wastewater treatment system.
Once the new microgrid is in place, the plant will be less vulnerable to power outages that could cause the plant to shut down and lead to potential wastewater spills into nearby waterways.
The microgrid project is expected to cost approximately $8 million once completed in 2024, with no funding coming from increased taxes in the community. Instead, the funding will be absorbed by a concession arrangement under which the wastewater plant is operated. This 30-year public private partnership was established to improve operation of the City of Rialto’s water and wastewater system, and to raise significant capital from private equity partners and capital finance markets.
The concession agreement’s initial funding allowed the city to invest in necessary capital improvements in the system while setting aside funding for deferred utility system lease payments and strategic reserve funds. With most of those initial efforts now completed, the microgrid project represents the first of the next-generation projects supporting the city’s commitment to innovation and sustainability. The microgrid project is expected to save the city approximately $350,000 per year in energy costs, with an average return on investment in about eight years.
The first stage of the microgrid project, a feasibility study conducted by VNA’s energy consulting company, SourceOne Inc., was recently completed. The Rialto City Council recently voted to approve the second phase, which will involve the design of the microgrid.
Source: veolianorthamerica.com
Timeline: Spa Holdings 3 Oy orchestrates buyout of Ahlstrom-Munksjö
On January 20, 2021 Spa Holdings 3 Oy announced that, together with certain other share purchases, its holding of the shares and voting rights in Ahlstrom-Munksjö would increase to approximately 81% after it completes its voluntary public cash tender offer to acquire all of the issued and outstanding shares in Ahlstrom-Munksjö that are not held by Ahlstrom-Munksjö or any of its subsidiaries. The settlement of such tender offer took place on February 4, 2021 and, therefore, pursuant to Condition 7.7 (Change of Control) of the terms and conditions of the Capital Securities, a Change of Control occurred and became effective on February 4, 2021. Subsequently, on February 10, 2021, Ahlstrom-Munksjö announced that the shareholding of Spa Holdings 3 Oy in Ahlstrom-Munksjö had exceeded the threshold of 90%.
Ahlstrom-Munksjö announced on February 5, 2021 that a “Change of Control Event” pursuant to the terms and conditions of the Notes had occurred, as a result of which noteholders could require prepayment of their Notes as provided in the terms and conditions of the Notes. The deadline for noteholders to require prepayment of their Notes is March 19, 2021.
On February 19, 2021, Ahlstrom-Munksjö Oyj held an Extraordinary General Meeting (EGM) at which a new board was named, it was announced the company is investigating a potential change of headquarters from Helsinki to another European Union country, and that the company is exploring changing the company structure to a Societas Europaea (SE).
On February 19, 2021, Ahlstrom-Munksjö Oyj also entered into an intercompany facilities agreement with Spa Holdings 3 Oy and Spa US Holdco, Inc, making up to EUR 550 million and a revolving facility of up to EUR 270 million available to Ahlstrom-Munksjö USA Inc, with facilities of up to $260 million for the purposes of refinancing existing indebtedness of Ahlstrom-Munksjö and its subsidiaries as required, and for providing Ahlstrom-Munksjö and its subsidiaries financing for its general corporate purposes and working capital requirements.
On February 19, 2021, Ahlstrom-Munksjö announced its intent to exercise its redemption right in respect of the Capital Securities in accordance with Clause 7.7 (Change of Control) of the terms and conditions of the Capital Securities. Ahlstrom-Munksjö announced irrevocably that on July 29, 2021, Ahlstrom-Munksjö will redeem the Capital Securities in whole at their Nominal Amount, together with any Accrued Interest (each as defined in the terms and conditions of the Capital Securities) in accordance with the terms and conditions of the Capital Securities.
Due to Spa Holdings 3’s application for the above-mentioned arbitration proceedings, the Redemption Board of the Finland Chamber of Commerce has petitioned the District Court of Helsinki for the appointment of a trustee to supervise the interests of Ahlstrom-Munksjö’s minority shareholders during the redemption process. With its decision given on March 9, 2021, the District Court of Helsinki has appointed attorney at law Antti Kuusimäki to act as such trustee.
Source: ahlstrom-munksjo.com
Micronics launches new website highlighting filter press and baghouse solutions
Micronics Engineered Filtration Group, Inc. launched a new website, highlighting its filter press and baghouse solutions. The new website focuses on industries and applications from Mining & Mineral Processing to Chemical Manufacturing, Energy from Waste, Coal-Fired Power Generation, Steel, Cement, Lime, Aggregates, Industrial, Food and Beverage, Battery Recycling, Pharma & Biotech, and Municipal.
“Micronics is a leader in both Filter Press Solutions and Baghouse Solutions and we felt it was beneficial to our worldwide customers to communicate the breadth and scope of Micronics’ offerings and capabilities in one place and in one new, modern, updated website – all under one roof,” according to Chris Cummins, President and CEO, Micronics Engineered Filtration Group.
“Since joining Micronics less than one year ago, I have been impressed with the talent & capabilities of the Micronics team around the globe, and this has been especially true in this challenging past year, through which our team excelled and pulled together to meet our customers’ needs. We trust that our new website will convey these strong capabilities of the Micronics Engineered Filtration Group, and that the extensive new content and imagery will allow you to better get to know us as a Total Engineered Filtration Solutions provider,” Cummins added.
“We are pleased to debut our expanded In-House Laboratory Services on the new Micronics Engineered Filtration Group website as well as other newly featured filtration products & services such as our Filter Press Cloth Installation/Changeout services that complements our industry-leading Filter Bag Changeout Services for Baghouses,” said Senior Vice President of Sales, Jason Wettstaedt.
“The new Micronics website allows users to better access the extensive blog content that Micronics – as a Total Engineered Filtration Solutions provider – has been developing over the past several years including a deep focus on filter media solutions, filter press solutions, baghouse solutions, and information specific to industries/applications,” added Wettstaedt.
Source: micronicsinc.com
Researchers funded by DuPont link production of clean water to membrane density
Through funding and leadership of DuPont Water Solutions, researchers recently found that the density of water filtration membranes, even at the atomic scale, can greatly affect how much clean water can be produced with reverse-osmosis membranes. The study demonstrated that precise control of density can increase membrane efficiency by 30 to 40 percent resulting in more water filtered with less energy — potentially making water purification and desalination processes more sustainable, productive, and affordable.
DuPont Water Solutions, the leading manufacturing of reverse osmosis and desalination membranes, along with the National Science Foundation, initiated, funded and supported the research.
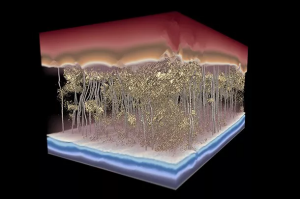
While conventional knowledge suggested that greater membrane thickness reduced how much water could flow through a membrane, DuPont researchers found that thicker membranes could be more permeable. DuPont initiated the research to better understand levers that could improve their membranes’ ability to increase the production of clean water while using less energy.
In addition to DuPont Water Solutions, researchers from Penn State, The University of Texas at Austin, Iowa State University, and Dow Chemical Company were engaged in the research and recently published the key findings as to the impact of density of water filtration membranes in the January 1, 2021 issue of Science. The article was also highlighted as the cover of this issue.
The researchers found that the thickness does not matter as much as avoiding highly dense nanoscale regions, or “dead zones.” The researchers determined desalination membranes are inconsistent in density and mass distribution, which can hold back their performance. Homogenizing density at the nanoscale is a previously unidentified key to increasing how much clean water these membranes can create, while using significantly less energy.
Read the full story: https://www.dupont.com/news/dupont-research-uncovers-key-maximizing-clean-water.html
Source: dupont.com
Colquímica Adhesives to open new production facilities in North Carolina
Colquímica Adhesives, with headquarters in Portugal and one of the world’s largest players in the development and commercialization of hot melt adhesives for industrial applications, will open a new subsidiary with related facilities in Charlotte, North Carolina in March.
The new $12 million, 100,000 square-foot plant is the Portuguese company’s first important production facility in the U.S. The new unit, Colquímica Adhesives Inc. will produce adhesives for the personal hygiene, packaging, and product assembly industries, and is expected to represent a 20% increase in the company’s production capacity.
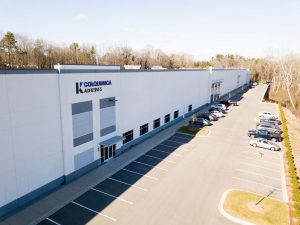
Seven years after opening the first production unit outside the country in Poznan, Poland, Colquímica Adhesives is building on its globalization strategy by expanding industrial operations to the U.S. “This new manufacturing facility reaffirms our commitment toward investing in the U.S. economy, as well as its dedication toward U.S. consumers,” said Pedro Gonçalves, CEO of Colquímica Adhesives Inc.
“Charlotte is an outstanding and strategic location for us. Being situated in a central point on the East Coast will allow a close service to Colquímica’s customers, with good proximity to all the main industrial states and major cities. It is very well served in terms of logistic infrastructure, road communications, and seaports,” he added.
The chosen location will allow the company to effectively serve not only North America but also Canadian, Mexican, and Latin American markets.
Colquímica Adhesives had a turnover of $126 million in 2020, and currently has more than 300 employees. The company is present in more than 65 countries and has a capacity of 143 million pounds of industrial adhesives per year.
Source: colquimica.pt
Shortage of raw materials for adhesives manufacturers
Outages in Europe and in the U.S. as well as limited freight capacities on sea and on land is having a negative impact on the availability of raw materials essential to adhesive manufacturing.
Global adhesives manufacturer Jowat is among businesses facing a disruption to the supply of key raw materials and adhesive intermediates caused by outages at several European and US American chemical manufacturers.
Availability of raw materials essential to adhesive manufacturing had already been limited prior to the outages. The situation has been further exacerbated by the recent severe winter weather in the U.S., which led to the loss of a large part of refinery and chemical production capacities in the country. This has also impacted the supply chains of Jowat’s international locations.
According to the US American Adhesive and Sealant Council (ASC), supply chains in and from the USA will take weeks or even months to recover.
In addition, the situation is made even more challenging by currently long transport times and limited availability of freight capacities on sea and on land. In the global raw material market, this also has a significant impact on the current supply situation in Europe and Asia.
“We regret the current shortage situation and are doing our utmost to remain a reliable supplier and partner for our customers. Our global orientation helps us operate in a flexible manner and reduce the negative consequences of supply bottlenecks as far as possible. In this unprecedented situation, however, supply disruptions can hardly be avoided,” said Klaus Kullmann, Managing Director at Jowat SE.
Source: www.jowat.com
Wallner Expac becomes 100% employee-owned company
Wallner Expac, Inc. completed a transaction to become 100% employee-owned through its newly created Employee Stock Ownership Plan (“ESOP”). The Company was founded in 1959 in Southern California, and with locations in Ontario, California, El Paso, Texas and Kennesaw, Georgia it is among the largest expanded metal manufacturer in North America to produce light gauge material for metal backing used in air filters.
After 62 years of significant expansion and growth, the shareholders of Wallner Expac have transitioned 100% of the company’s total ownership to all of the employees of the company through a qualified retirement plan known as an ESOP. All eligible employees will be granted shares of company stock each year, at no cost, allowing them to earn ownership over time through their service to the company and accumulate tax-deferred retirement wealth. Wallner Expac joins a group of elite 100% employee-owned companies across the United States of America.
According to Mariana Orozco, President & CEO, “Each employee of Wallner Expac is a trusted team member. The founders of our company want our employees to feel that they ‘own and operate’ their own business which fosters tremendous pride resulting from owning a stake in the Company. They also want our hard-working and loyal employees to benefit beyond their wages alone if they continue to help grow Wallner Expac. Together we strive to be more efficient, innovative, safe and responsive to our clients’ needs.”
The Wallner family decided to implement this plan because they felt it was the best and most sustainable path forward for the employees and managers of the Company in a manner that protects the legacy that they have built.
Wallner Expac was advised by Ambrose Advisors, a national investment banking firm specialized in employee-ownership transactions. Best Best & Krieger LLP acted as legal counsel in connection with the transaction.
Source: expac.com
Mann+Hummel acquires Pamlico Air to complement Tri-Dim subsidiary in commercial and industrial air filtration
The Mann+Hummel Group today announced its strategic investment in Pamlico Air, a U.S. manufacturer and provider of air filter products, mainly for retail and wholesale applications. Pamlico Air will be part of the Mann+Hummel Group and complement the existing air filtration portfolio of its subsidiary Tri-Dim, which focuses primarily on the commercial and industrial air filtration aftermarket.
“By investing in Pamlico Air, we see a tremendous opportunity to accelerate the growth of our Life Sciences & Environment business unit,” said Kurk Wilks, President & CEO of the Mann+Hummel Group. “We highly value Pamlico Air’s expertise and leadership in the area of retail and wholesale air filtration. As part of the Mann+Hummel Group, Pamlico Air will strengthen our filtration offering in the aftermarket business as well as open up opportunities in the planning and specification phase of new installments.”
“This strategic partnership with Mann+Hummel enhances Pamlico Air’s operational capabilities and gives us a significant stake in one of the most exciting segments of filtration,” said Harry Smith, CEO of Pamlico Air. “We see significant opportunities to drive value for Mann+Hummel’s air filtration business in the region.”
“We look forward to joining forces with the Pamlico Air team to expand our existing product portfolio in North America, and accelerate efforts in strategic business areas,” said Mark King, President at Tri-Dim Filter Corporation. “Both companies share the same market understanding and value for our customers, which is why we see great growth opportunities ahead.” The North American retail and wholesale air filtration market is one of the largest and fastest growing filtration segments. Pamlico Air, with its product superiority and distribution excellence, will be a strong addition to Mann+Hummel’s portfolio in the field of air filtration.
Pamlico Air will continue to be led by Harry Smith and his management team. Mark King remains president of the Mann+Hummel subsidiary Tri-Dim Filter Corporation and will work
closely with the Pamlico Air leadership team as one organization.
Source: mann-hummel.com
Lydall CEO, Sara Greenstein, bullish on filtration products during interview on ‘Mad Money’
Lydall CEO Sara Greenstein told CNBC’s Jim Cramer that the company is working with the Biden White House to help replenish the national stockpile of personal protection equipment, and she expects demand for specialty filtration products to be greater beyond the pandemic.
The Manchester, Connecticut-based company makes specialty filtration material that is used in N95 respirators and surgical masks, items that are especially critical for healthcare and frontline workers during a health crisis.
Greenstein said in a “Mad Money” interview that President Joe Biden’s administration is “actively pursuing efforts” to build a strategic stockpile.
Read the full story: https://www.cnbc.com/2021/02/26/lydall-ceo-sees-demand-boom-for-its-filtration-material-beyond-pandemic.html
Source: lydall.com
AFS announces upcoming virtual courses and chapter meetings
The American Filtration and Separation Society (AFS) has announced its upcoming course schedule and chapter meetings. The event lineup includes:
Tuesday, March 16, 2021 – 9:00 – 11:00 am – CDT
*Daylight savings time (US) begins on March 14
Virtual Course – Automatic Filtration Technologies for the Chemical Process Industries
The use of manual filtration solutions, such as plate filters, bag filters, and filter presses, can create process problems and operator safety concerns in chemical manufacturing processes. This course covers automatic technologies designed to help alleviate these potential problems. This event is presented by Barry A. Perlmutter, president of Perlmutter Idea Development, LLC. Perlmutter has 38 years of technical engineering and business marketing experience in the field of solid-liquid separation including filtration, centrifugation, and process drying. His strong professional skills focus on process solutions, innovation strategy, market expansion, and business development.
Thursday, March 18, 2021 – 9:00 am – 9:45 am – CDT – USA
Chapter Meeting – Great Lakes
Overview of the Current Requirements for General Barrier Face Coverings
Discussed will be a review of the new ASTM specification for barrier face coverings, ASTM F3502. Barrier face coverings are defined as a product worn on the face specifically covering at least the wearer’s nose and mouth with the primary purpose of providing source control and providing a degree of particulate filtration to reduce the amount of inhaled particulate matter. This event will be presented by Matthew McGarrity of SGS-IBR. McGarrity has been in testing, inspection, and certification for more than 10 years and specializes in regulatory, industry, and quality requirements. His areas of focus are respirators and medical PPE such as gowns, gloves, and surgical masks.
Tuesday, March 30, 2021 – 9:00 am – 11:00 am – CDT – USA
Virtual Course – Review of the Regulatory Requirements and Classifications of Respirators and Facemasks
This course, also presented by SGS-IBR, is designed to help the audiences gain a fundamental understanding of the medical mask and respirator industry. It will also provide must-know information about usage, regulatory, and test methods It is an excellent course for anyone who aspires to learn more than the basic information about medical masks and respirators. It is especially useful for those who are interested in this market as this course will provide the information ne3eded to make an informed decision regarding the possible market entry.
For more information and to register for any of these events, visit https://www.afssociety.org/virtual-courses.
Source: afssociety.org