Three major German-headquartered suppliers of filtration materials – Freudenberg (Weinheim), Mahle (Stuttgart) and Mann+Hummel (Ludwigsburg) – have recently been doing a good deal of thinking about the future of the automotive industry.
Attitudes to public transport and mass transit systems have been transformed by the events of 2020 for the immediate future. Prior to COVID-19 – in Europe and Asia, if not yet as much in the United States – there has been a concentrated effort for some years to establish more efficient public transport systems, get more people to use them, and move gas-guzzling cars out of cities, in the general fight against rising carbon emissions.
With the virus still rampant, however, nobody wants to be in a crowded bus or train, with the proximity of any fellow human flagged up as a danger and crowded, enclosed spaces something to be avoided at all costs.
Sales decline
Yet the $2 trillion automotive industry has hardly benefited, with initial forecasts for the sales of private cars averaging out at a decline of around 20% globally for 2020. In 2019, some 91.8 million cars and light vehicles were produced worldwide, according to the Paris-based Organisation Internationale des Constructeurs d’Automobiles (OICA).
The longer-term challenge for suppliers of filter materials to the transportation sector meanwhile comes from the push to replace the internal combustion engine (ICE) entirely with a combination of battery-electric, plug-in hybrid and fuel cell alternatives, which has only accelerated in the past 12 months.
California action
In a first from any U.S. state, California – as the standard bearer for clean air regulations – announced in September that it would ban the sale of new combustion-engine vehicles starting in 2035.
The EV 30@30 campaign – launched in June 2017 by the Clean Energy Ministerial (CEM) involving 24 countries and the European Union – has already had a galvanizing effect.
Within a month of it, Swedish car giant Volvo announced it would launch only electric or hybrid vehicles from 2019, and the French government said it would end the sale of petrol and diesel vehicles by 2040. Two weeks later, the UK followed suit and announced that the sale of petrol and diesel vehicles would be banned in the country by 2040.
In December 2020 – despite all its immediate Brexit and COVID-19 issues – the UK went a stage further and announced that the ban on the sale of petrol and diesel vehicles would be moved forward to 2030.
If this happens – and it is a very big if – it would put the UK level with much less densely-populated and wealthier per capita Norway, where one out of every three cars purchased is already an electric vehicle.
China has meanwhile arguably taken the real lead in the field of both building electric vehicles and establishing the charging infrastructure to make them a realistic proposition.
Engine performance
For the filtration industry, the move away from the combustion engine is highly significant. There are currently more than 50 filters in an average passenger car, and many of them are connected to the performance of the engine.
Because combustion engines run at high temperatures, oil, in the presence of air, may oxidize and form tar and varnish sludge. Without suitable filtration systems, this sticky mixture adheres to moving components and causes wear and tear that can lead to reduced service life of the engine and its components.
Media employed for filtering fuel and oil must demonstrate good chemical and temperature resistance and the filtration system is also constantly subjected to a great deal of vibration, so it needs to withstand extreme operating conditions. And since the filter media represents the last line of defense for engines against contaminant-related wear and tear, its performance needs to be consistent and predictable during the service cycle.
Automotive air induction filters are meanwhile designed to remove suspended contaminant particles from the air stream that flows to the engine. These typically operate in near-ambient temperature conditions, depending on their proximity to the heated engines. Such filter media are designed to have a service life of two to three years.
Significant advances have been made in the performance and design of engine-related filters for modern vehicles over the past two decades and it has been a solid market bolstered by aftersales, but now a potentially major change in the landscape looms.
Batteries and fuel cells
Freudenberg has already established a leading position in the provision of battery separators for electric vehicles, with its ultra-thin products made from ceramic-impregnated polyester nonwovens.
These remain stable at high temperatures and do not shrink, while being significantly less sensitive to external mechanical stresses than competing products. The thinner separator can also contribute to a higher energy density in new batteries.
The company, however, believes that in the longer term, fuel cell cars will come to the fore, since compared to battery-powered cars, they have a longer range, can be refueled in only a few minutes, and are also suitable for buses and trucks.
Freudenberg’s gas diffusion layers (GDLs) ensure that hydrogen fuel is converted into power as efficiently as possible. They have a three-dimensional fiber structure and a chemically stable coating of electrically conductive carbon particles which makes them highly functional.
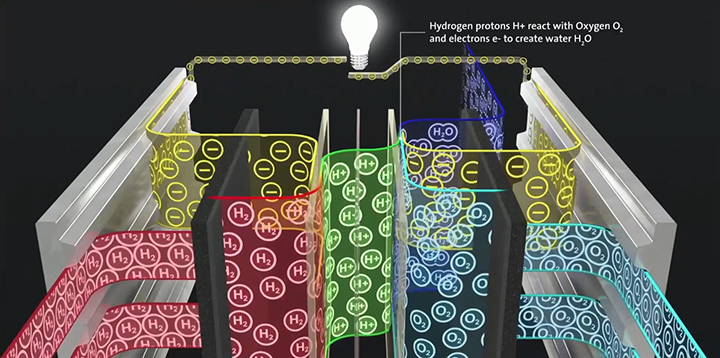
Functionality
Within the single fuel cell stack, the GDL is positioned between the bipolar anode and cathode plates at either side of the catalyst coated membranes. The material must be both thin and stiff, as well as porous, but thermally and electrically conductive – and keep water out while ensuring the membranes in the fuel cell remain wet.
The GDLs are produced in a roll-to-roll system with 100% camera-based surface inspection at Freudenberg. They are non-fragile and can be easily further processed, with magnetic polishing liquid (MPL) surfaces that are crack-free and a smooth and a morphology designed for customized applications. They have a high specific power density and are said to be the only product available on the market with a thickness of just 120 microns.
Among other developments at Freudenberg is a new friction insert for joints, addressing challenges with new electric vehicles in terms of NVH (noise, vibration and harshness) while having no negative impact on corrosion. It consists of a 20-micron nonwoven carrier material studded with harder particles, creating a micro interlocking system between parts while adding no additional tolerance.
Brake dust filter
Mann+Hummel has recently developed several high-performance room air purifiers aimed at fighting Covid-19 and continues to work on the needs of new mobility vehicles.
Representing an entirely new filtration application for example, its brake dust particle filter substantially reduces the particulates which are created during braking.
Braking in city traffic creates significantly more dust than exhaust emissions, the company points out – every braking action creates dust through friction on the disc and pads. This mainly comprises particulates, more than 90% of which are ultra-fine, and therefore harmful to both health and the environment.
The synthetic nonwoven filter media is resistant to temperature and corrosion, and the company is also developing sturdier versions made from both glass fibers and stainless-steel fibers.
The retention of the fine dust directly at the place where it is created prevents the soiling of alloy rims and to a large extent the tedious removal of entrenched brake dust.
In addition to use in cars, the filter can also be used in commercial vehicles and in railway applications, where a large amount of harmful fine dust is produced due to the high weight, long braking distance and frequent braking of rolling stock in semi-enclosed spaces such as railway stations.
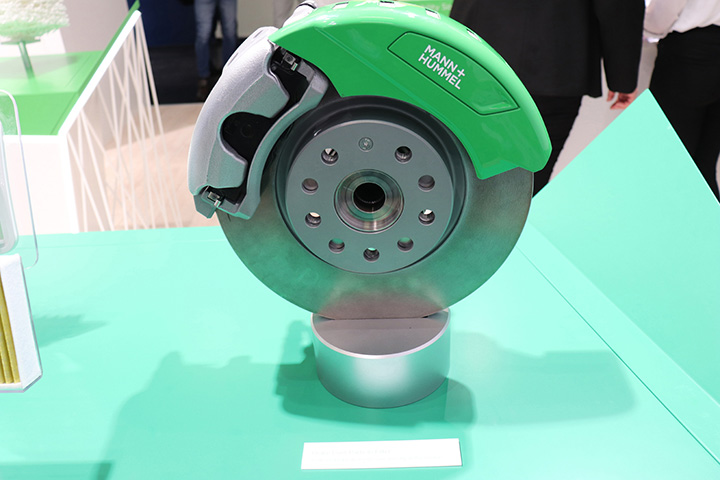
Multigrade eM-CO
The Mann+Hummel Multigrade eM-CO filter media is for use in the e-axle, which combines the electric motor, gearbox and power electronics in the latest electric vehicles.
The highly integrated e-axle has been designed to save installation space, components and wiring due to being integrated with the drive axle, to achieve up to 20% less weight and improving efficiency by between 5-10%.
Because the e-axle’s drive components are integrated, a common oil circuit is sufficient for cooling and lubrication, but there is a drawback – mechanical and electronic components are exposed to oil and metal particles and chips from the transmission, which can penetrate the power electronics and electric motor and cause serious damage.
As a result, these particles need to be efficiently removed by a filter integrated on the pump suction side directly in the oil sump, to protect the system from the pump to the return flow to the sump.
The glass-free Multigrade eM-CO filter media has a high chemical resistance and considerably lower differential pressure in comparison to conventional gearbox oil filters fitted on the suction side.
The media comprises consistent filter layers without uncontrolled artificial media bypass – something which is necessary for conventional products due to their high loss of differential pressure.
Further Mann+Hummel, new mobility developments to date include:
- An ion exchanger filter for fuel cells which maintains the low conductivity of the coolant in fuel cells.
- A cathode air cleaner system for fuel cells with highly efficient water separation, to protect the layers of activated carbon.
- A coolant particle filter for fuel cells, which ensures cleanness of the coolant necessary for the thermal management of electric vehicles and a cooling air particle filter for high-voltage battery systems, in addition to battery frames, air drying cartridges and venting units for them.
OzonePRO
Mahle’s latest development could only really have been conceived in response to the virus of 2020, with its smart air conditioning system – in which fine-particulate sensors are directly integrated – supporting the fight against fine particulates in a vehicle’s cabin.
With immediate access to both cabin air and external air, the system can react quickly and precisely to changing pollution levels, and its cleaning keeps the air in a vehicle clean.
The Mahle OzonePRO stand-alone unit has been proven in tests to reduce the number of bovine coronaviruses (BCoV) – similar to the SARS-CoV-2 viruse that causes COVID-19 and used in testing because they pose less immediate risk to those conducting the tests – by around 99.7%, during a 35-minute purification cycle.
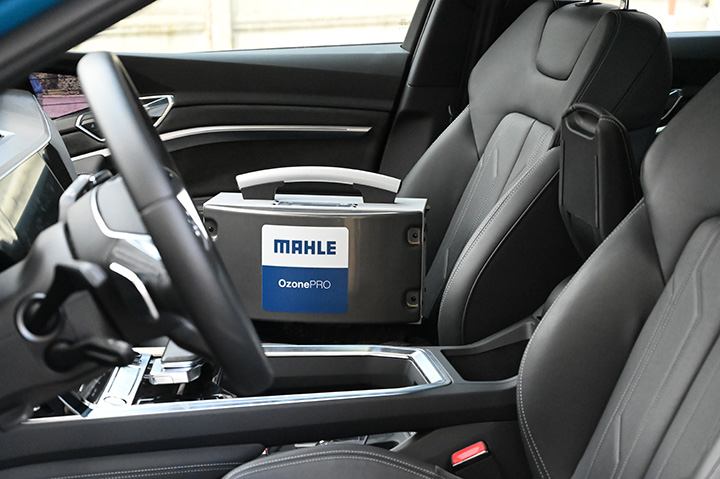
While the sanitizing process is underway, the OzonePRO sensors continuously measure the concentration of ozone produced in the environment and keep it constant, at the same time avoiding excessive ozone values to prevent oxidation damage to car interiors. The unit is fully automated and notifies the user via a related app when the process is finished.
With an ozone output of 5,000 mg/h, one unit, weighing just 3kg, can sanitize interiors with a surface area of up to 30 square meters or a volume of around 75 cubic meters – roughly the equivalent to the volume of a coach.
These development are unlikely to be the last filtration innovation for the automotive industry, as the industry transitions to new vehicle types, and indoor air quality inside these vehicles becomes a more pressing topic of discussion in light of the COVID-19 pandemic.