Part I of this series introduced the filter media of modern bag filtration technology and the relevant criteria for selecting components of a bag filtration system. Here is a summary of the key points:
- Characteristics and size of particles or solids to be removed (absolute versus nominal)
When cleaning a liquid, only certain contaminants may need to be removed but others, which are not critical or which are valuable, can or have to stay in the filtrate. A filter that removes all particles of a specific size under strictly defined test conditions is an “absolute” filter, while a filter that prevents an undefined percentage of solid particles of greater than the stated pore size, which is normally expressed in micrometers (or microns), is a “nominal” filter. The decision between nominal and absolute is one of the most important criteria to look at. Nominal is not worse than absolute. The key is to find the filters that work best in the specific application without exceeding or putting in finer filters than needed. This is typically done by on-site testing. - Process conditions (flow rate, pressure, temperature)
Once the filter type is selected, the required flow rate defines the number of filter bags required. Depending on the process conditions, the quantity of filter bags can be increased. In a batch process, for example, more filter bags might need to be considered to avoid interruptions for changing out filter bags. Other factors can be ergonomic in nature, or footprint or height restrictions. - Filter media types
The three most common filter medias are needlefelts, woven monofilament meshes and meltblown media. Each technology offers specific filtration characteristics that makes them an optimum choice for a particular range of applications, type of particle to be removed and liquid being filtered. - Considerations for filter housing choice
There are two basic filter housing flow patterns – top inlet or side inlet. Top inlet versions are generally preferred because they have the filter bag sealing ring compressed directly by the bolted lid which improves sealing and eliminates potential bypass.
Ways to improve filtration processes
One of the key challenges in sizing and selecting the filter media is to find the type of filter that comes closest to the optimal maintenance interval. In the industry many types of filter bags are available that will give the same particle retention efficiency capability but have different capacity levels. All of these filter bags can also be used in the same filter housing, though some may need additional tools or support baskets.
The optimal capacity of the filter bag can be chosen when the filter system is sized up or the capacity can also easily be upgraded in already running applications. Increasing the capacity and life of a filter bag reduces maintenance intervals, saves on product losses and disposal cost. Even when the filter bag is more expensive, optimal selection can offset this additional outlay by bringing savings in process cost.
There are 4 different approaches to increase capacity:
- Add more or larger filter bags (traditional way)
- Switch to higher capacity filter media
- Increase the filter area in the existing filter
- Multi-step filtration (prefilter/final filter) with different pore sizes
The traditional way
The most traditional approach to increase capacity is to increase the number or size of the filters. This can be achieved by installing an extra filter or exchanging the bag filter housing for a larger one. It is, however, a costly option requiring investment, process downtime and extra available floorspace. There are, however, more astute ways of tackling this problem. Based on the solution there are ways to boost the capacity by a factor 2, 5 or even up to 10 compared to basic standard needlefelt media. There are two criteria that will play a role here. One is the capacity of the media used and the second is the surface area packed into one single filter.
With the new developments in materials and technology, filter bags are becoming more and more popular – even in highly sophisticated applications. Being capable of “nominal” to “absolute” filter levels, filter bags can be valid alternatives in many stringent applications.
Higher capacity media
Instead of adding additional filters there is the option to switch to higher capacity media. As we learned above a standard needlefelt is a depth media. Here, the contaminant is trapped in between the fibers of the media and filling the void volume inside that media. Standard needlefelt media (polypropylene or polyester) typically have thicknesses of 2 to 3 mm (0.08 to 0.12 inches). There are high-capacity, or often called extended lifetime, media available. They feature the same removal efficiencies, taking out the same size particles, but are at least twice as thick and have more than double void volume. Hence, when loaded optimally, capacity increases of up to 2 to 3 times can be expected. An added benefit of using thicker filters is the increased retention capability for gelatinous or deformable matter. The filter bag itself is visually similar, apart from the thickness of the media.
Increase filter area
Another way to increase the capacity is to add filter surface inside the same filter bag. Various designs can be found and each, however, comes with its specific benefits and limitations.
Increasing the filter surface lowers the velocity of the liquid through the filter media. There is also a direct correlation between the velocity through a filter and the capability to optimally load the void volume in the depth of the media. There is a theory that says when you double the filter surface, you can increase the capacity by a factor 2 to 4. The higher gains relate more to applications where there is a constant cake build-up of crystalline particles of the same size. This is not always the case and, in reality, the capacity gain will be somewhere in the middle. What is true, however, is that there always will be an extra gain above the sheer increase of surface.
There are two common ways to increase the surface inside the filter bag. One design has a normal outer shape, but also features an additional inner cylinder of a smaller diameter, which is inverted inside the outer cylinder. Both are joined at the bottom by a simple flange. The filtration surface can be increased by as much as 65%. As an additional and very important advantage is that the inner volume of the filter bag is reduced by 75%. This is volume that is not used and can be taken up by unfiltered liquid, which is lost when the filter is hard to drain.
A second and most typical way to increase the surface inside a filter is the pleating process (Figure 1). However, the right balance needs to be found between the surface area and media depth. When used in bag filtration one further factor plays a crucial role; this is the direction of the flow. A cartridge filter operates with a flow from out to in. In a circular pleated construction, however, the unfiltered liquid arrives where the pleats are nicely open. The filtrate leaves the pleats where they are dense and compressed – here there is no particle build-up. In a filter bag concept, however, this goes the other way. It is critical, therefore, to design the filter so that liquid and particles can pass through the pleat structure at the inside and can be trapped inside the filter media. A proper use of separation and drainage layers can help here.
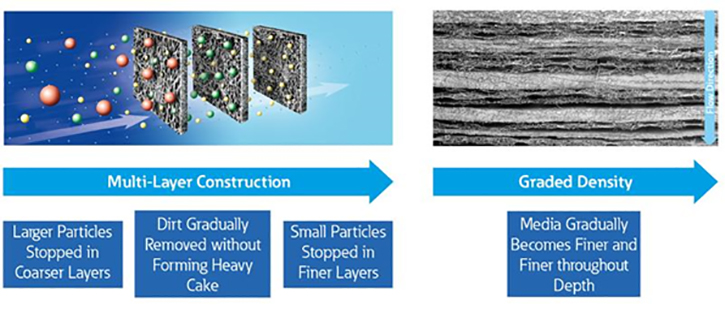
Multi-Step filtration
Last but not least, multi-step filtration is always worth considering to increase the capacity of a filter. This concept combines two or more filter levels with different pore sizes – pre- and final-filtration. Certainly, when having contaminant with a very wide spread of particles sizes, it makes sense to remove contaminants in different stages. It can even be with different filter systems (Figure 2).
In traditional filter bags, the basic way again is to install multiple filter housings, this time connected in series. Filter bags of a lower to a higher retention are then passed through in sequence. As an alternative multilayer filter bags can be selected – the benefit being that, as they are all together in one bag, only one housing is needed and footprint is reduced. This type of installation is used for higher efficiency filter bags, where particles of descending size are held back through the graded depth of the filter.
50 years of bag filtration – a standard evolving
With more than 50 years in use, bag filtration is a standard process used around the world. Its ease-of-use and high capacities have always been the major benefits of filter bags. With the new developments in materials and technology, filter bags are becoming more and more popular – even in highly sophisticated applications. Being capable of “nominal” to “absolute” filter levels, filter bags can be valid alternatives in many stringent applications.
Thoughtful planning and appropriate scaling are the keys to success when choosing the right filter bags, and there is no substitute for experience. Eaton Filtration offers in-depth consultancy on choosing the right filter technology and filter bag to its partners and clients and guarantees the same high level of product quality worldwide. More information on filter bags and other filtration solutions can be found at eaton.com/us/en-us/products/filtration-solutions.html.
Part I of this article can be found here…