This is the first article in a two-part series covering the practical aspects of bag filtration technology. Part 1 introduces the filter media of the technology and some guidelines for housing selection. Part 2 presents proven methods for optimizing the filtration process.
Bag filtration is used in many industrial processes to remove unwanted particles from a liquid. Traditionally, this filtration method was a basic option for nominal non-critical applications. Today, filter bags are used to filter a lot of different liquids – from water to glue – for wider and more stringent applications and conditions. When selecting a filter bag and the assorted options various aspects need to be taken into consideration to make sure the best possible performance level will be achieved. Some of the most relevant criteria are:
- Characteristics and size of particles or solids to be removed (absolute versus nominal)
- Process conditions (flow rate, pressure, temperature)
- Filter media types
- Considerations for filter housing choice
Characteristics and size of particles
When cleaning a liquid, only certain contaminants may need to be removed, while others that are not critical or are valuable to the process, can or have to stay in the filtrate. When practically all particles of a specific size and larger need to be removed an “absolute” filter is needed. The absolute pore size rating specifies the pore size at which a particle of a particular size or larger will reliably be retained by the filter with defined efficiency (e.g. >99%) under strictly defined test conditions. For example, 15 µm absolute means that all particles with pore size of 15 µm or larger will be retained to 99% during one filtration process.
A “nominal” pore size rating refers to a filter capable of preventing passage of an undefined percentage of solid particles of greater than the stated pore size, which is normally expressed in micrometers (or microns). Conditions during filtration, such as operating pressure, shape and concentration of particles, have a significant effect on the retention capability of the filters.
The discussion on “nominal’ versus “absolute” is one of the most important criteria to look at. Nominal is not worse than absolute. The key is to find the filters that work best in the specific application without exceeding or putting in finer filters than needed. This is typically done by on-site testing. The cost-value ratio needs careful consideration – the finer the filter, the more expensive it will be. In addition, finer filters typically clog faster, too, which relates to downtime and again increasing costs. To avoid clogging, the industry often relies on two or more filtration steps. With every step, the filters become finer to remove smaller particles than in the previous step. This prefiltration process reduces the risk of the filter clogging before final filtered liquids are ready for usage.
Process conditions
The process conditions are highly relevant to choosing the right filtration solution. Depending on the application there might be a need for a specific temperature resistance or the ability to deal with higher pressures. Next to choosing the right type of filter, process parameters also play a role in the specific sizing of the system. Once the filter type is selected, the required flow rate defines the number of filter bags required. Depending on the process conditions, the quantity of filter bags can be increased. In a batch process, for example, more filter bags might need to be considered to avoid interruptions for changing out filter bags. Following a scheduled change-out interval may be more appropriate for better maintenance planning.
Other factors can be ergonomic in nature, or footprint or height restrictions. Often smaller, more compact filters are preferred for height accessibility or ease of exchange. When filtering viscous liquids, such as glues, paints or resins, it may be more practical to have a shorter type filter where the housing has a lower access point and the bag itself is shorter. The capacity will only be half of the more popular size, but the ergonomic advantage makes it the preferred option.
Filter media types
Filter bags are popular in many processes and industries, going from basic water over food products, paints and coatings to various chemicals and solvents and this in variable ambient temperatures for these applications. Typical filter materials are polypropylene, polyester and polyamide (nylon) – each has specific characteristics, making them compatible in specific conditions. There are three basic filter media types: Needlefelts, woven monofilament meshes and meltblown media.
Needlefelts are the most popular and are formed by mixing assorted sizes of fibers and condensing them together through a needling process. They carry a nominal rating between 1 µm and 200 µm. Here, polypropylene and polyester are commonly used and available in either a sewn or welded configuration.
Where a sewn filter bag with a metal ring used to be the standard choice, this has evolved to a fully welded version with a bypass-free plastic seal ring. The mixed fiber structure makes needlefelts a depth filter. This means particles can be trapped within the matrix of the filter. While large particles will stay on top, smaller ones migrate in the media structure and, depending on their size, will be trapped or can go through. Needlefelt filters enable high flow rates, while performing at low clean initial differential pressure. To limit fiber release into the filtrate, the polypropylene and polyester versions feature a singed or glazed surface finish. Specific versions are available for use in the food and beverage industry. These follow regulations in place for plastics in contact with foodstuff. Typical applications in the food industry include vegetable oils, fats and sugar solutions. Needlefelt bags are usually a single layer product and are available in standard- and extended-life variants.
Woven monofilament meshes form a 2D grid surface filter. They typically vary between a 5 µm and 1,200 µm particle size range. When considering round and crystalline particles, these filters can be considered to be absolute rated. As such, they will provide a much sharper cut off where it is critical to remove all particles of a certain size or bigger. A typical application here can be the protection of nozzles to prevent blocking of the opening. The most common material used is nylon or polyamide (Figure 1).
The last media group are the meltblown filter media, for which polypropylene or polyester are also the most common materials used. These types of filters are manufactured directly from a polymer without the need of using surfactants or specific additives, as needed for the processing of fibers or in the needling process. The filter media, therefore, has a purer, finer fiber structure, enabling a much tighter retention rate. Graded multilayer constructions provide a staged filtration process and optimal filtration capacity. These filter bags are typically used where particles need to be removed down to 1 µm on a high efficiency basis and typically have an absolute efficiency rating.
Considerations for housing choice
There are two basic flow patterns – top inlet or side inlet (Figure 2). Top inlet versions have the filter bag sealing ring compressed directly by the bolted lid. This improves sealing and eliminates potential bypass. The filter bag also sits level at the top of the filter and is, as such, easier to change out. This version is recommended for all higher efficiency filters. The housings also have a reduced height and better accessibility compared to the side entry models.
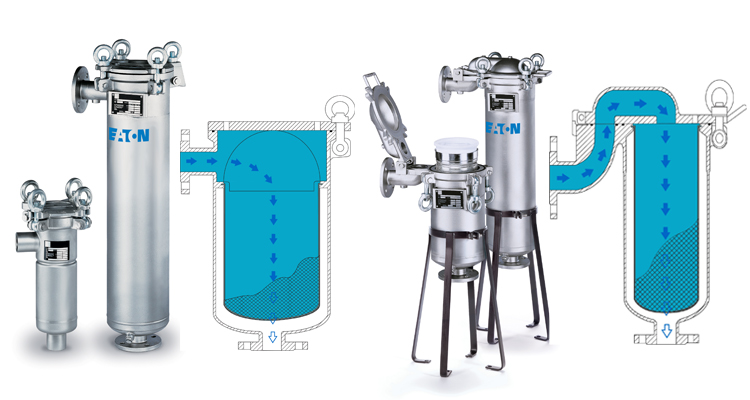
Finally, there are two extra accessories used to help facilitate filter bag operations. The Bag Lock, also known as Bag Positioner, tool is used to install the filter bag in an easy and correct way. As its intrinsic strength is limited, it needs to be supported by a metal basket which will take all the differential pressure. Unsupported bags can be prone to damage and bursting problems, certainly at the bottom seam area. The accessory can stay in the housing during filtration and prevents the filter from collapsing during backflushes. It can also be reused during the next maintenance phase. These accessories can also be equipped with magnetic rods, serving as an extra trap, catching ferritic particles prior to coming to the filter media. This enhances filter life or prevents damage from the sharp metallic particles.
Standard size 02 filter bags measure 7 inches in diameter with a length of 32 inches, which provides a filter surface of about 5 ft². However, inside the bag is a volume of close to 4.2 gallons, which remains mainly unused. When the filter is clogged-up and requires replacement, it can be sometimes difficult to drain this liquid, which leads to product loss and makes removing the bag significantly more difficult. A displacement balloon is a metal, stainless steel construction, that takes up that unused volume inside the filter bag. It is placed inside the bag and stays there during filtration, before removing the filter for maintenance, the bag positioner is taken out and the volume of the product inside the filter bag drops from 4.2 to 1.9 gallons. This accessory is very commonly used for all viscous and expensive products, e.g., paints and resins.
Next Month: Ways to improve filtration processes
Part II of this series will discuss field-proven methods to improve both the efficiency and cost-effectiveness of processes using bag filtration technology.
Part II of this article can be found here…