Topics Covered At Edana’s Filtrex 2014 Conference In Berlin Ranged From Sector Specific And Immediate Issues To The Broader Future of Transportation And Manufacturing
November/December 2014 | Volume 33, No. 6
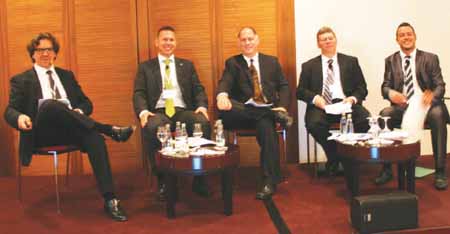
Single-stage nonwoven filter media are no longer sufficient for meeting water separation efficiency requirements in modern fuel tanks and diesel fuel systems. This was one of the key messages to be taken away from the EDANA Filtrex 2014 conference held in Berlin, Germany, from October 1-2.
Another couple of messages were rather bigger in terms of their implications ÔÇö that the continued growth of the global automotive industry can no longer be taken for granted, and that digital industrialization is poised to change everything anyway.
RETHINKING DESIGN
During a panel discussion on fuel filtration, Andrew Shepard, director of global market management at Hollingsworth & Vose Engine and Filtration said that new regulations for diesel and other fuels are currently impacting all along the supply chain in respect of:
- Emissions requirements
- Fuel quality
- Biofuel impact
- Sustainability
- Service intervals
- Compliance testing
All of this, he said, is resulting in the need to rethink filter design, because at the moment, particulate removal is the key goal.
In diesel engines, however ÔÇö and those with bio content, which are even more vulnerable ÔÇö water removal needs to be the first priority.
Water enters the fuel tank and diesel fuel in a number of ways. Sub-standard fuel with a high water content can be a possible cause, as can misfuelling, the ingress of water via the fuel tank ventilation or condensation.
The consequences include corrosion and cavitation on injectors, valves and the injection pump ÔÇö which can ultimately lead to a system failure. In addition, free water can cause microbiological growth and corrosion processes, which frequently lead to premature blockage of the fuel filter or pitting corrosion of the filter housing.
Today, commercial vehicle engines are developed for global use. Modern fuel filter systems must therefore meet a variety of demands in terms of fuel quality, contamination, water content and use with regard to their filtration and separation requirements.
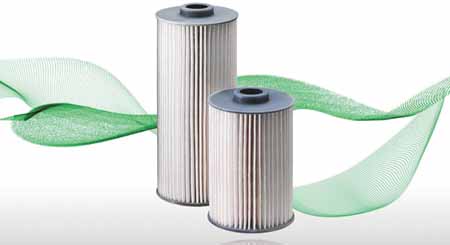
SINGLE-STAGE CONCEPTS
In the past, single-stage concepts were sufficient to meet the requirements for water separation efficiency. For this purpose, the filter element was equipped with a water barrier layer on the flow side. This concept, however, is no longer adequate for pressure side filter operation or for the use of modern low-sulphur fuels, which contain biofuels and have a high additive content, in order to effectively protect the injection system from damage.
If water from the fuel tank enters into the fuel circuit, it is broken up into small droplets in the low-pressure fuel pump. After several fuel cycles, extremely small droplets may form. A stable fuel/water emulsion then forms, which does not separate, even over several days.
Separating small droplets presents a challenge for fuel filter systems ÔÇö filter elements that are based on a water repellent effect on the flow side of the filter cannot ensure water separation in the long term. The small droplets are not separated at the surface but as a result of their size, are forced through the pores of the filter medium. The hydrophobic properties are impaired to such an extent, particularly by additive components in biofuel and separated impurities, that the water separation capability is completely lost over the service life of the filter.
MULTIGRADE
“The more contaminated the fuel, the greater the filtration requirement,” said Harald Banzhaf, director of R&D in liquid filter elements at Mann+Hummel, headquartered in Ludwigsburg, Germany. “The injection technology in common rail systems already operates at 2,500 bar pressure and now Bosch, for one, is talking about going up to 3,000 bar, which will require even cleaner fuels.”
In order to ensure reliable water separation over the service life of the filter element, Mann+Hummel has developed a three-stage filtration concept, which is used in its latest Multigrade filtration modules.
With this concept, the fuel flows from the outside to the inside of the filter element. In the first stage, solid particles are filtered out and it’s crucial that the coalescer and the hydrophobic fabric are not contaminated by particles. The coalescer then retains the water droplets and combines them to form much larger drops. In the third stage, the hydrophobic screen fabric prevents the drops from following the fuel into the injection system. The separated water itself is collected in the filtration module, detected there and emptied out either manually or automatically. Thanks to the high water separation efficiencies that can be achieved, the injection systems and commercial vehicle engines are reliably protected.
MOBILITY
But while there may be currently more than fifty filters in an average passenger car or truck ÔÇö contributing to functions ranging from the performance of the engine, oil and fuel consumption through to the quality of the air in the cabin ÔÇö Philip G. Gott, of leading U.S. analyst IHS Automotive, based in Lexington, Mass., said that the world is in the early stages of a massive shift in consumer preferences for personal mobility.
Congestion, he said, now costs cities billions each year. It impedes the efficient movement of goods and as a result manufacturing within them stalls, with employers moving out.
“At the same time, it’s beneficial to keep people clustered in cities, so mass transportation infrastructure and alternatives to the car are essential for progress. Car ownership peaks as a function of population density and at ten thousand people per square kilometer it starts to go down.”
The growth of the new light vehicle market, he predicted, may soon level out at an annual 100 million units, which will mean 30 million less of them will be produced each year than has previously been forecasted going forward. And by 2035, this will mean there will be 260 million fewer light vehicles on the roads than there are today, as older cars reach the end of life and are not replaced.
Asian cities, Gott suggested, will not grow to the motorization rates of the West, and indeed, Beijing has already imposed a cap on new vehicle registrations to keep the overall number of vehicles down to 150 per thousand people.
“Such measures will mean slower growth for replacement filters in the next 20 years, but at the same time, systems that improve air quality in mass transit and other shared vehicles will provide new opportunities,” he concluded.
NEW MANUFACTURING
Another keynote speaker at Filtrex 2014, Robert Glaze, of the Brenva Institute, based in Colorado Springs, Colo., believes even greater changes are in the pipeline.
Five years ago, said Glaze, overall technology R&D could be divided into one third biotech, one third new energy and one third communications and computation.
“Today, it’s one third biotech, one third computational science and one third new manufacturing, and digital industrialization is the next revolution,” he said. “3D and 4D printing is leading to a rapid materials evolution and machines are becoming ever smarter. There will be end-to-end automation as machines replace humans at an ever faster rate.”
Some of the things that are coming next, he suggested, include:
- Brain-computer interface and affective technologies
- Multi-functional additive manufacturing and molecular recombination
- Predictive and anomaly analytics
- Increasingly rapid prototyping for speed to market
- 3D bio-printing, bio-chips and neuro-technologies
4D PRINTING
“MIT has already developed context-aware materials via 4D printing, and 3D printing is already more sophisticated than you think,” said Glaze. “Machines will soon become co-workers and colleagues. The major chemical companies, meanwhile, are very worried about molecular recombination technology because it threatens to put them out of business. This all implies changes in corporations and manufacturing companies as much as it does manufacturing methods.
“We’re going to see the disintermediation of labor as flow analytics replaces individual metrics and organizations evolve into non-human-based ecosystems, along with distributed intelligence in networks, systems and, ultimately, humans. This will be a major challenge, and already, Apple has plans in place to eliminate its entire existing supply and retail chains ÔÇö involving a million people around the world ÔÇö in the next five years. Instead of holding inventory, it now plans to install its own huge 3D printing machines strategically around the world.”