July/August 2015 | Volume 34 No. 4
By Stephen Hiner, Chief Engineer – Gas Turbine Inlet Systems, CLARCOR Industrial Air
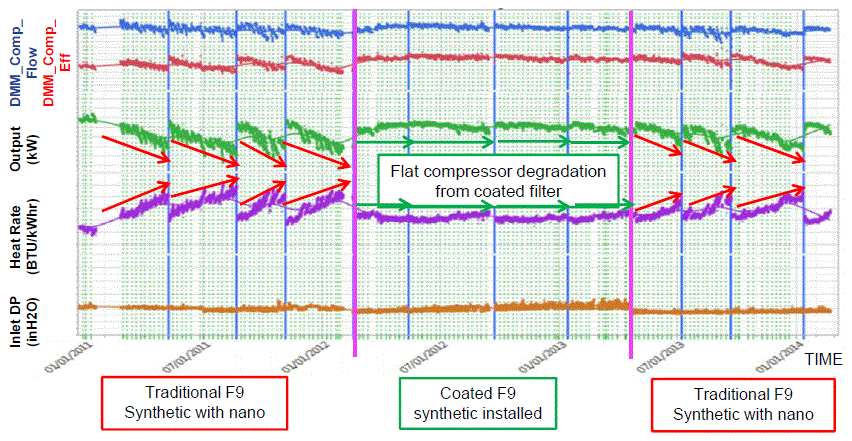
Gas turbines are used for driving electrical generators, pumps and compressors and for creating steam in applications such as gas power stations, marine vessels, offshore platforms, smelting plants, pipelines, LNG loading stations, refineries and chemical plants. A gas turbine is a high value asset and the enormous amount of air they consume during operation means the quality of this air is a critical element for their performance, availability and reliability. Due to the nature of the end processes that rely on a properly working turbine, needing to stop a gas turbine for an unplanned outage can often result in large, costly production losses.
A gas turbine filtration system may have to deal with a combination of dust, salt, hydrocarbons and other contaminants as well as high levels of moisture, extreme conditions or varying temperatures. Poor inlet filtration can lead to foreign object damage, erosion, fouling, cooling passages becoming plugged, and fusion of particles within the turbine, leading to costly downtime or even worse, catastrophic component failure. Traditional filtration systems are built to mitigate most of these failure modes today but fouling and cold end-corrosion can still be problematic areas needing to be overcome.
Cold-end corrosion is caused by a mixture of corrosives entering the machine in the form of a solid, liquid, gas or vapor. Media filters are used to remove solids but do not generally remove liquid corrosives, such as salt. These can, however, be dealt with through the use of water removal stages and hydrophobic treated filters. Gaseous and vapor borne corrosives cannot be effectively stopped by any filtration method that exists today.
Fouling, caused by dirt adhering to the compressor blades, does not cause permanent damage but does reduce compression efficiency, which negatively affects the performance of the machine. In high value processes, the loss of efficiency and turbine availability can be very costly. To combat this, operators periodically shut down the turbine to “offline” wash in order to restore performance levels. For many operators, there are real advantages to maintaining efficiency as well as reducing (or even eliminating) the offline wash frequency.
Prevent Fouling from Reducing Turbine Efficiency
Compressor fouling reduces heat rate (fuel efficiency) and causes power output losses of the turbine over time. There are two methods to stop fouling. The first is to prevent the fine (less than one micron) particulates that cause this phenomenon from reaching the machine internals. This can be achieved through the use of high efficiency EPA or HEPA filters (typically E10 or above). The use of these filters alone, however, only addresses dry contaminants and, by the very nature of the finer media used, they are likely to be more sensitive to any moisture present in the airflow. This, in turn, requires significant investment to upgrade the filter house to handle the moisture without creating a high differential pressure.
In an ideal world, all gas turbine inlet systems would be fitted with filter houses designed to be large enough to accommodate HEPA filters that stop virtually all particulate contaminants from entering and fouling the machine. In reality, however, most existing gas turbine filter houses are too small for HEPA filters to operate at their optimum flow rates and as such, their use can create operational issues.
The second method to prevent fouling is to stop the small contaminants that reach the machine from sticking to the compressor blades. The use of hydrophobic and advanced fiber coated filters can stop the sticky contaminants from reaching the compressor and therefore prevent compressor fouling.
Figure 1 highlights the difference between compressor performances when fitted with traditional F9 filters compared with enhanced F9 filters that have hydrophobic and advanced fiber coated media. Both filters have approximately the same fractional efficiency when new. The vertical red lines show when offline compressor washes were performed. It can be clearly seen that, although the operator continued with a regular frequency of offline washes, the performance of the compressor shows little deterioration over time when media with advanced coatings were used to protect the system. The graph also shows the same compressor being refitted with traditional F9 media filters after the use of the coated media filters, and how the clear decline in performance returns between washes, which undeniably confirms the benefit and value of the advanced media coatings for superior filtration and improved gas turbine characteristics.
The ideal filter solution provides high efficiency (fine fibers) as well as long service life (achieved using multi-layer composite media) that are highly pleatable to give performance and compactness in robustly (strong media) designed units. Operators require the filters to give predictable, reliable performance even with changing environmental conditions; meaning filters need to handle moisture effectively. Hydrophobic and advanced fiber coated filters have been shown to provide this performance in the harshest conditions such as coastal, offshore and desert installations as well as to prevent liquid corrosives from entering the turbine, which can cause permanent damage through cold end corrosion.
Air filters are used in many applications but when used in gas turbine installations, they are subjected to significantly higher pressures and harsher environmental conditions than are typical in commercial applications like HVAC protection. Therefore, gas turbine filters must be more robust in their construction and performance.
Challenges for the Nonwovens Industry
As filter technology advances to address real world challenges and provides predictable, reliable, long life operation, there are still many challenges for the nonwovens industry to address. Moisture and other liquids are an issue in many high efficiency applications and innovation needs to continue to create higher efficiency media that is less sensitive to mist, spray, fog and hydrocarbons, while also having the strength to handle the harsh operating pressures and environmental conditions.
Where pulse cleanable media is used, this presents additional challenges as the high efficiency filter layer needs to be on the surface of the filter so that the pulse can be effective in removing the captured contaminants – but this is where it is particularly vulnerable to moisture. To date, upgrades to pulse cartridges to achieve greater filtration efficiency and turbine protection typically mean that the pulse system has to be turned off since the new media is not sufficiently robust to withstand regular back pulsing with compressed air.
Advanced coatings on fibers have proven their worth in terms of protecting the turbine from sticky contaminants and liquid corrosives, but further research and development work remains to determine how to prevent these properties from wearing off over time as the filter loads with real world dust.
Synthetic media is preferred in gas turbine inlet filtration because of its strength and superior resistance to moisture and other chemicals, but to date filters installed in the field have not performed equivalent to results achieved during lab testing. Therefore, more effort needs to be focused on developing synthetic media that truly holds or improves its efficiency in real world applications.
Summary
As manufacturers push the boundaries of turbine technology to provide more power and greater fuel efficiency, these advanced units also become more susceptible and sensitive to the quality of air and fuel they use. To protect compressor efficiency, a filtration system needs to prevent fine contaminant particles from reaching the compressor blades. If this is not possible because of size constraints in existing installations, then utilizing a filter with the latest filter coating technology can prevent contaminants from sticking to compressor blades, which would otherwise decrease turbine performance.
Although there are areas where further research and development could produce media that addresses more of the real world challenges filter installations experience, hydrophobic and advanced coated media currently available in the marketplace have been proven to protect operating efficiencies and reduce the need for offline washing. This not only helps ensure optimized production and energy efficiency, but in applications where a turbine outage has a large impact on high value productivity, can save millions of dollars in lost production.
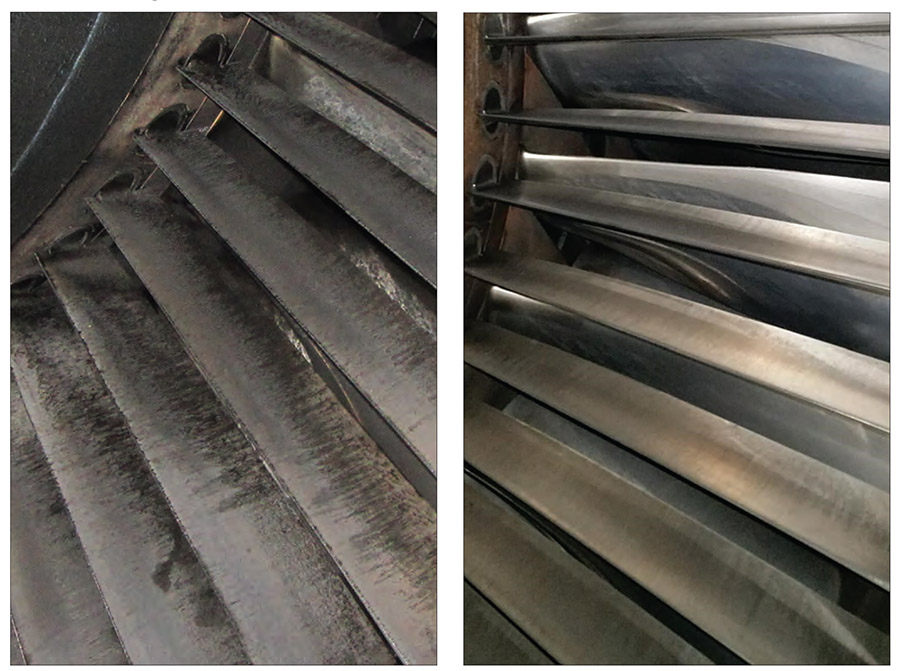
About CLARCOR Industrial Air
With 50 years of experience delivering innovative solutions for gas turbine inlet filtration and monitoring fleet-wide performance data, CLARCOR’s industry and applications experts select the appropriate filter for clients site designed to meet their specific operating goals.
CLARCOR Industrial Air supplies a full range of inlet systems and filters engineered to meet operating goals, including:
- Higher power output
- Lower operating costs
- Proven performance utilizing advanced filter technology
- Extended gas turbine availability
- Maximum protection against corrosion and fouling
- Easy maintenance and change out
CLARCOR is the choice for advanced filtration for new units and replacement filters. The company’s inlet system designs include self-cleaning (pulse) and static inlet systems for all gas turbine OEMs. CLARCOR supplies a full range of filter types at all efficiency levels. The predictable and reliable performance of their air filters significantly reduces compressor contamination and the need for unplanned maintenance.