This is the second installment in a new recurring column in IFN called “Moon Shots,” highlighting innovations and new ways of thinking in the filtration industry. The first article in this series, “Overcoming the Gordian knot of the water, energy, CO2 nexus,” can be found at https://bit.ly/waterenergynexus. If you would like to pitch your “Moon Shot” idea for publication in an upcoming issue of IFN, please contact Matt Migliore at mmigliore@inda.media or +1 (919) 459-3754.
Yes! We are going to the moon and beyond. After our first visit to the moon, Neil Armstrong and Buzz Aldrin noted that dust was a big problem. Indeed, our crews need clean air. Filters can do the job – if we think outside the Earth.
The challenge
Filtering airborne particles in extraterrestrial human habitats poses unique challenges unlike any on Earth. The air cleaning and filtration systems not only need to remove a broad size range of particles, such as skin flakes, hair and clothing fibers, and other substances from food and hygiene operations, but they must also remove any extraterrestrial planetary dust tracked into the habitat by the crew returning from extra vehicular activities, as well as debris from operating machinery and equipment inside the habitat.
Keep in mind that at the low-to-zero gravity encountered in space, even large particles will remain airborne and will become a problem. Further, the absence of atmospheres on extraterrestrial bodies like the moon or Mars results in sharp-edged particles from the planetary surfaces, which can cause severe damage to humans and equipment, and even to the filters used to remove them. All this needs to be accomplished without any make-up air from outside, since every cubic foot of make-up air needs to be either shipped from Earth or made in space.
Adding to the challenge is the servicing or replacing filters in space, which is not a trivial task. Not only do replacement filters add to the payload requiring extra rocket boost and extra workload on the crew for maintaining the system, but the distances involved make sending replacements impractical. Consider a one-way trip to Mars can be nearly a year long.
Designing a filter system is only half the challenge. How do we test to verify its performance? Think of it as combining the ASHRAE and HEPA filter test methods into one and adding in the filter life for good measure. All at low spacecraft cabin pressures and microgravity to simulate conditions in space as much as possible.
Meeting this challenge will require a system capable of filtering particle sizes spread over several orders of magnitude, from nano sizes to several hundred microns, and the system must be able to operate for a long duration, even years, without filter changes. And test methods would be required to verify its performance.
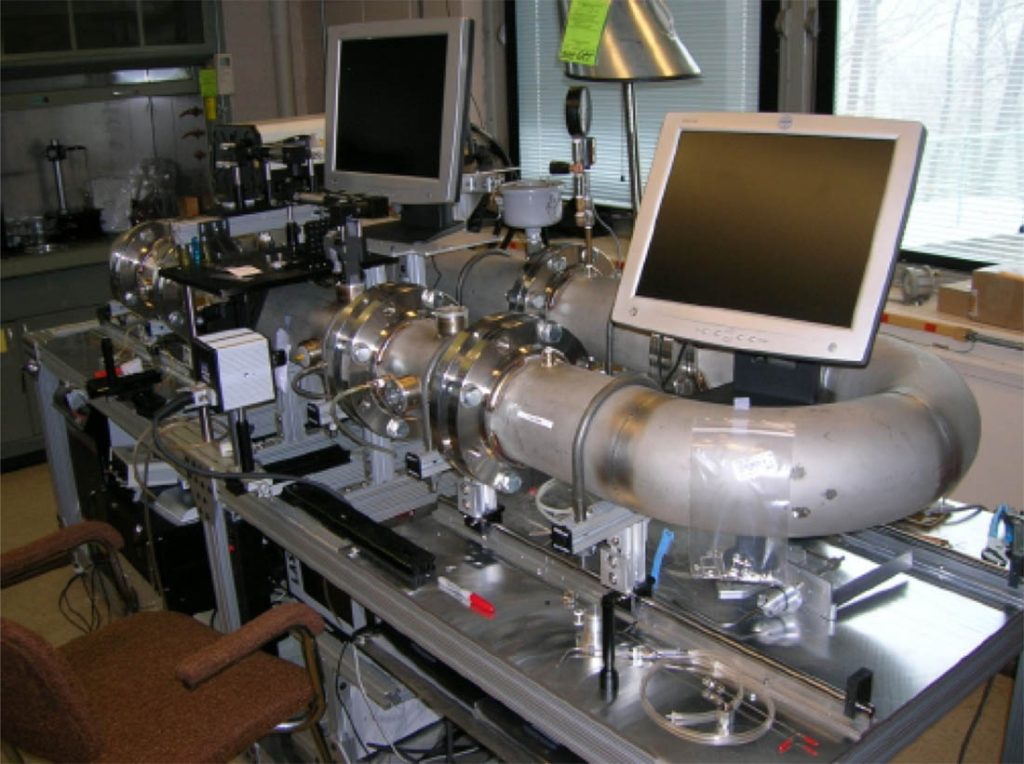
Filtration system
The large range of particle size will require multi-stage filtration. Think of a filter system for a MASH (Mobile Army Surgical Hospital) in the middle of a desert. While several available filter designs and layouts are considered, one was designed specifically to meet the requirements.
The Scroll filter is a three-stage filter (Figure 1). This is a patented device jointly developed by scientists at NASA Glenn Research Center and AERFIL. The first stage of this device is an impactor with a cleanable impactor plate that allows for virtually endless in-use life. The cut size can be modified to suit the space mission needs. The second stage is rolling pleated filter where the filter media is indexed when fully loaded to expose fresh media. Any media to suit the mission specs can be used, and even altered during the design and testing phase. The impactor or the media filter stages are modular and may be stacked to achieve any desired filtration performance. The final filter in this configuration is expected to be a traditional HEPA filter that remains for the duration of the mission. This is along the lines of cleanroom filters with adequate prefilters that are designed for the life of the cleanroom.
The Scroll filter has commercial applications, and one company has licensed the patent from NASA.
Testing
Unless a filter is tested, its performance will be unknown. On Earth, we readily use test methods and standards. While the methods, in principle, will suit filters for space, there are a few challenges. Among these are the low operating pressures, the unique shapes and size ranges of particles to be filtered, and the microgravity operating environment. Testing the Scroll filter was done three different ways. First, the components, mainly the media, were tested in a specially built multi-pass test rig (Figure 2).
The rig was built to test in vacuum down to ~10 Torr for simulating spacecraft cabin pressures and planetary surface environments. This hard vacuum limited the size of the rig to a 6” diameter for safety reasons. The rig has the usual complement of particle detection instruments. Due to the vacuum, a patented dust feeder was built to generate the lunar dust simulant challenge aerosol. Although the rig may be used for testing scaled down versions of full filters and other components required for the mission, for this project, only flat-sheet media were tested.
Meeting this challenge will require a system capable of filtering particles sizes spread over several orders of magnitude, from nanosizes to several hundred microns, and the system must be able to operate for a long duration, even years, without filter changes.
Particles to be filtered during crewed missions to the moon include those typically found indoors, such as dust, skin flakes, emission for equipment, etc., as well as the lunar dust tracked in from outside the habitat by the crew. The usual oil or salt aerosols used in filter test standards can be considered acceptable aerosol challenges with respect to indoor air filtration. For lunar dust, NASA has formulated a proprietary dust to simulate the lunar regolith. These are gritty solid particles approximating what is expected on the lunar surface. Testing with these simulants at lower pressures showed higher efficiencies than at ambient pressures. This was as expected due to the reduced drag at lower pressure.
Confirming performance of systems in microgravity is essential for space missions. Typically, these are first conducted in zero gravity simulated in parabolic flights. For these flights, an aircraft flies in vertical parabolas, as shown in Figure 3, to simulate the weightless state from the free fall. Weightlessness starts when aircraft reaches the top of the parabola and then starts free falling. As the aircraft approaches the bottom of the parabola and starts pulling up the low-g period ends. The shape and geometry of the parabolas are set to simulate the microgravity required for testing. Although true zero gravity is possible in these flight patterns, the short duration of these patterns, often under two minutes means a test interval in microgravity of about 20-25 seconds.
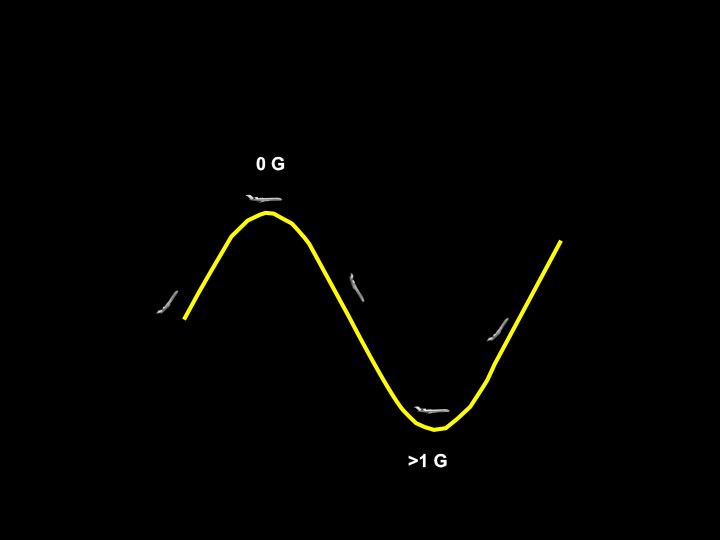
For filter testing, the biggest challenge was and is to the generation of a uniform challenge aerosol and complete the up and downstream measurements in under 25 seconds. Preliminary results confirmed that filter performance in microgravity is similar to that on Earth. As with all systems for space missions, the final configurations of any of the selected systems will undergo longer duration testing under microgravity conditions in the Space Station.
For more information on the scroll filter and for testing in the test rig featured in this article, please contact the author at vijay@aerfil.com.
The views expressed are the author’s and not endorsed or approved by NASA.