This railway is using powerful filter media to deliver optimum results while consuming significantly less water
Cleaning various parts, such as spring retainers, traverses and axle guides, is critically important when servicing trains. Only when the dirt and residue has been thoroughly removed can maintenance personnel confidently inspect parts for possible damage. Schweizerische Südostbahn AG (SOB, Swiss Southeast Railway) is relying on track cleaning concepts from BvL Oberflächentechnik for its service center. And with the help of filtration solutions from Eaton, the cleaning system can be used to clean parts with maximum efficiency.
Industrial parts cleaning
Rail companies count on BvL Oberflächentechnik (Emsbüren, Germany) when it comes to parts cleaning. With a tradition tracing back 150 years, BvL is a leading manufacturer of industrial cleaning systems to rail transport operators and many other companies that have a need for clean parts.
Thorough and consistent results are paramount when performing water-based industrial cleaning. Schweizerische Südostbahn AG (SOB, Swiss Southeast Railway) – which operates across much of Switzerland – traditionally cleaned train parts at a service center in Samstagern using a manual washing chamber as well as a high-pressure jet for large parts. This was time- and labor-intensive and consumed significant amounts of water.
SOB turned to BvL for a redesigned cleaning system with a smaller footprint that would better accommodate the confined spaces of the Samstagern center. BvL delivered a tailor-made solution based on its Pacific TA large-volume spray cleaning system, but that requires about 15% less space. In this context, the loading concept of the system is modified: One of two loading trucks which guide parts into the system now has half the operating length. Additionally, a pressure washer allows cleaning tasks to be performed by hand when required.

Durable filter delivers benefits
Of special concern to SOB was the efficiency of parts cleaning in terms of personnel costs and water and energy consumption. In response, BvL designed its system with an option to adjust operating height to accommodate different parts, which allows cleaning performance to be intensified and process time shortened.
Another factor contributing to both improved performance and reduced environmental impact is the ability to filter the water used for cleaning, which can then be reused several times. BvL has relied on Eaton’s expertise in this area for years and works closely with Eaton’s Filtration Division as its primary supplier of filtration solutions.
At Samstagern, the cleaning system must stay ready for use, meaning it was important to select filter elements that do not need replaced often. Eaton recommended its HAYFLOW element that can provide up to five times longer service life opposed to standard filter bags. Designed for higher flow rates, the element has a filter area up to 65% larger than most bags.
The HAYFLOW elements are contained in Eaton TOPLINE stainless-steel housings having an inlet at the top, which saves space compared to locating the inlet on the non-filtration side. This design also provides a better seal and makes it simpler to replace filter elements.
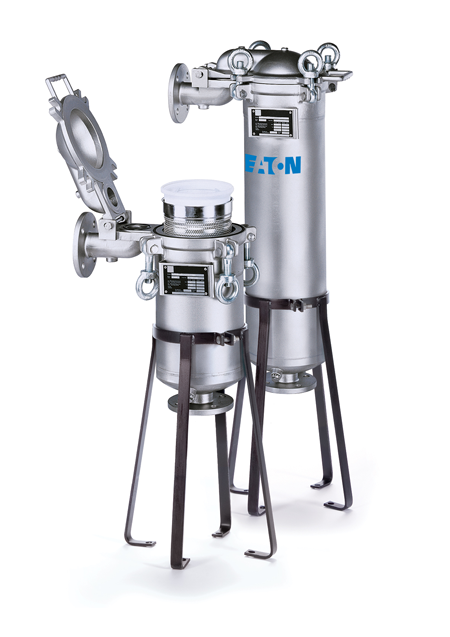
(© 2021 Eaton. All rights reserved.)
Alternatively, Eaton’s HAYFLOW Q elements can be inserted into the same housings for enhanced filtering performance. These use Eaton’s DURAGAF extended-life filter material that acts as a high-performance pre-filter and depth filter. In combination with a nylon monofilament cover layer, a final filter retention rating at 10 μm is achieved.
Best cleaning results
SOB reports that train parts are now cleaned with significantly better results and less effort demanded from employees. Cleaning fluid can also be guided through the full-flow filtration in the cycle, while sensors on the BvL system and a comparison with the reference pressure allow operators to forecast water consumption more accurately.
Additionally, the large-parts system and manual cleaning chamber are both able to use the same source of cleaning fluid, meaning water can be taken from the existing system and used many times in the circulatory system.
SOB is now able to clean parts using minimal water and energy, with maximum convenience for personnel. Manual cleaning is virtually eliminated, and hours worked in all areas of production and maintenance are decreased. For this rail company, high-quality filtration is essential for cleaning system efficiency and the associated conservation of resources.
This content is sponsored by Eaton.
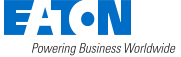