Filtration impacts every aspect of our lives. Most people are familiar with the air dust filters in the HVAC unit or the cartridge filters in the refrigerator for drinking water; however, very few are aware that most manufactured goods we use and processed food we eat require filtration or separation, directly or indirectly. Filtration processes can be physical, chemical, or biological operations that separate one or more matters from a mixture. The filter medium is designed such that it will allow the fluids – called filtrates – to pass through; however, it will retain solids that are oversized. When standard filter media fall short, porous polymer filters are used by design engineers to correct that shortfall.
What are porous polymers?
Porous polymers are materials with microscopic pores that are intentionally created and designed to provide various functionalities – such as filtration, venting, wicking, diffusion, and absorption. While there are several types of porous polymer technologies, the technologies of choice for filtration are sintered plastics and porous fiber.
To visualize the sintering process, imagine a jar that is filled with marbles, and then heat is applied such that these marbles bond with each other. When the jar is taken away, a body of particulates that are bonded together remain in the shape of the jar. The spaces between the particles are the pores.
To visualize the fiber bonding process, imagine straws that are held together and heated so that the fibers melt at certain points and bond to each other. These porous fibers can be made bicomponent, where one fiber is used on the inside and another on the outside to add functionality. Fiber media have very high pore volumes so fluid flow is higher, and they have a very high holding capacity for contaminants.
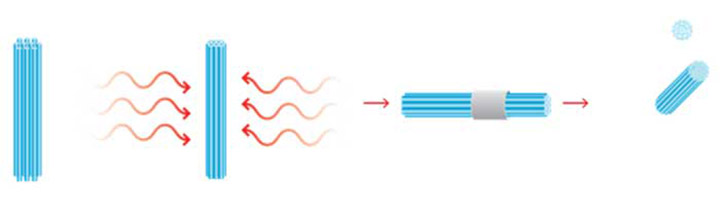
Importance of pore size in filtration
The pore size is the size of the voids in the porous media. Pore size impacts the efficiency of filtration, the distance and wicking speed of a fluid, and the rate of the flow of fluid through the media. The pore size can be controlled to achieve desired functionality. The degree of filtration is primarily determined by the pore size, or the size of the largest particle that can pass through the filter.
One of the biggest differentiators with porous polymers is the ability to use both surface and depth filtration. Surface filtration is a common form where particles are retained on the surface of a filter if they are not able to pass through. In depth filtration, the fluid is made to pass through a torturous path to a medium. Particles are trapped both at the surface and inside the filter media, as they navigate the tortuous path through the filter, and both filter media structure and thickness influence retention. Porous polymers can be designed to remove one molecule or a mixture of molecules of different sizes.
Customizing your filtration media for better product performance
While the possibilities are endless, some common use cases for porous polymer filtration media include:
- Removing water from fuel or diesel streams
- Removing harmful gases from gas sensors
- Removing contaminants from pools and spas
- Removing aerosol and liquid viral or bacterial contaminants from lab samples
- Removing contaminants from reusable pharmaceutical inhalers while ensuring metered dosing and sterility
For more information about porous polymers, check out our free The Science Inside educational webinar series at www.porex.com/webinar or reach out to one of our engineers directly for a consultation at www.porex.com/ask-an-engineer.
This content is sponsored by:
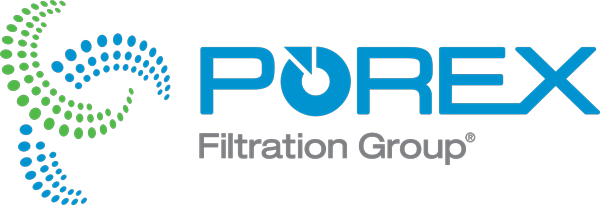