This article provides a brief history on the use of nonwoven roll media for metalworking coolant filters. These filters are typically employed in machining, grinding, rolling, drawing and forming applications. They apply to all types of flatbed filters – gravity, vacuum and pressure – which have unique aspects compared to other types of filters. These filters are used on closed-loop, multi-pass systems and must handle a continuous input of contaminants because the operations they serve create them. The media acts as a “foundation” to develop the cake of contaminants, providing a more effective barrier (Figure 1). Yet even with filtering, there will always be a level of contaminant left in the fluid, and the goal is to maintain this contaminant at an acceptable level for the application.
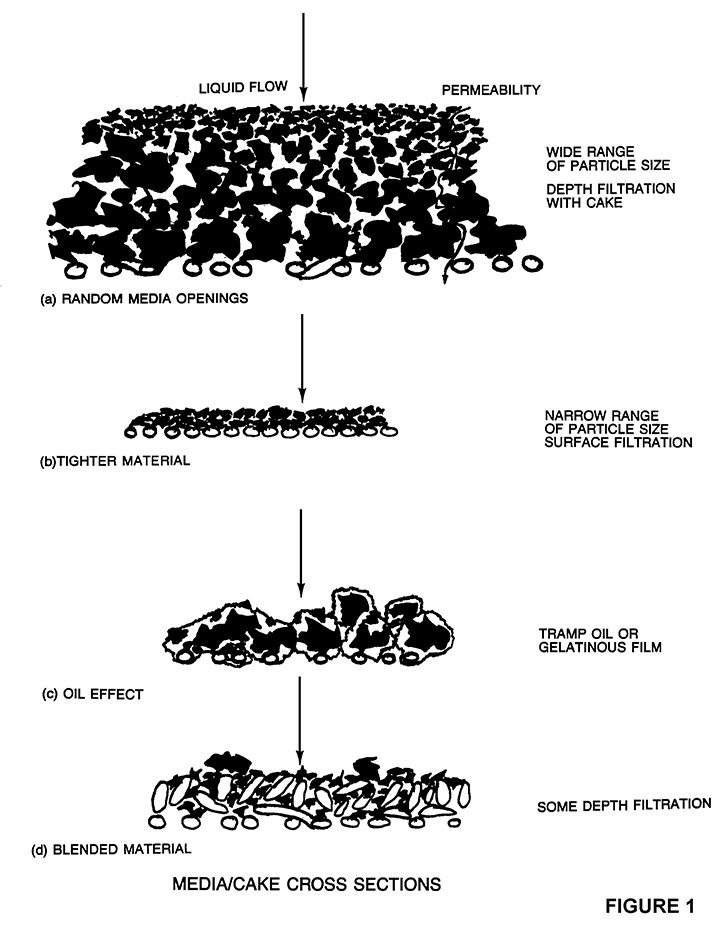
The history of coolant filtration
Up until the 1930s, there was little concern for fluid cleaning in coolant systems. Over time, the need to manage contaminant levels has become a more important application requirement.
Late 1930s and early 1940s
- As production demands increased, settling retention tanks were introduced to clean the coolant and give it a longer life. Dual switchover tanks were used when downtime for manual cleaning was a factor.
- With productivity increasing, more effective cleaning options were introduced; including self-cleaning conveyorized settling tanks, magnetics, flotation clarifiers, centrifuges and hydrocyclones. Technically these are “separators” because they use techniques other than a barrier to separate the particles from the liquid. However they were still called “filters” as the industry jargon for any device which cleaned coolants.
- Many operations with oils had precoat pressure filters (tubes or screens) with filter aids to achieve the desired clarity.
- Other than the precoat filters on oil, the clarity of the fluid was not exceptional but was bearable at that time. Manufacturing tolerances were wider than they are now. The quality of finished parts mating smoothly during assembly was not as critical. This was in the era when new cars were driven at low speeds for a while to “break in.”
- The goal for better quality components forced the need for improvements in coolant cleaning concepts.
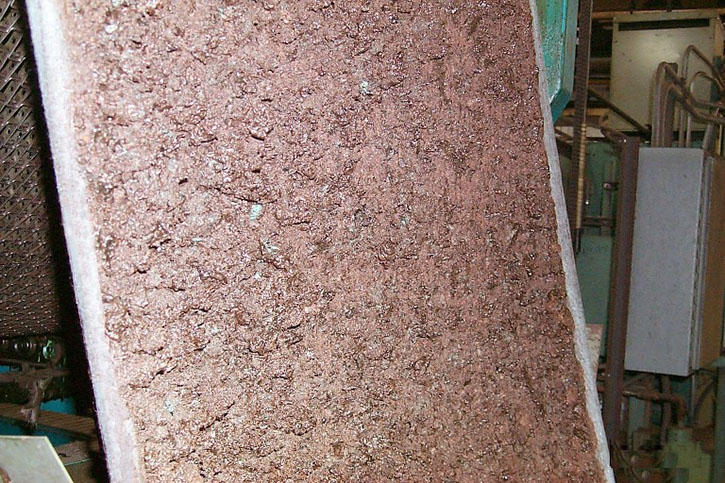
contaminants from a copper wire production line. Photo courtesy of James J. Joseph
Between the late 1950s and mid 1960s
- Disposable roll media filters were becoming an option for filtration systems. The term “positive filtration” was used to differentiate them from the family of separators.
- Initially, the use of disposable media was greeted with distain. Plant management did not want to pay for the disposable material or handle the extra waste when other devices had no consumable cost. The spent cloth was dubbed “glorified toilet paper.”
- It took some convincing before the industry recognized advantages of “positive filtration” to cope with the variables found in more sophisticated metalworking operations.
- At that time there was only one type of material – woven unbleached cotton (tobacco) cloth similar to what is shown on Figure 2.
- There were just four choices of tightness based on thread counts per inch:
• 28×24 most open
• 32×28
• 44×36
• 60×48 tightest weave - 1-inch wide media became the standard because that was what the mill produced after trimming the edges. Narrower widths were slit from the 51-inch material. Equipment manufacturers began to design filters for that width.
- There were a few concerns for some of the coolants reacting with the thread coatings of the fabric.
Typical nonwoven fabrics for metal working coolant filtration
- Polyester
- Polypropylene
- Nylon
- Blended Polyster/Cellulose
- Rayon
These are manufactured in many different processes, as well as blends. There are also other fabrics employed in select, less-common application scenarios.
Early 1970s
- The commodity price of cotton skyrocketed and unbleached cotton for filter media became too expensive.
- This opened up a huge potential for nonwoven fabric manufacturers who felt the disposable aspect with repeat business was appealing. They ushered in fabrics of polyester, polypropylene, rayon and nylon.
- Later blends of cellulose, long/short fibers, multi-layer fabrics were engineered to meet many application needs.
- Many new oil installations did not need the elaborate precoat pressure filters.
- Fiber binding techniques were improved to virtually remove the concern for chemical reactions between the fabric and coolants.
- The evolution of these fabrics went through many learning curves, not only for media manufacturers, but also coolant blenders, filter companies and users. It did not come easy, as each facet of the industry continually made advances balancing performance, design and costs.
- Fabric strength in both the cross and machine directions were addressed since the material has to survive the rigors of being pulled or dragged though the bed of the filters. Filters which carry the fabric on belts are not as vulnerable.
- Equipment manufacturers were able to build wider filters to enhance the filter’s performance and offered more flexibility.
- At first, the copper wire drawing manufacturers could not use media filtration. Their coolants were unstable soap/fat compounds, which were easily stripped as the liquid was forced through a tight barrier. Once the coolant blenders developed more homogenous fluids, then the wire producers began to seriously look at media filters.
- Now, the full range of fabrics provided many possibilities for conventional filters to be used on installations, which were heretofore beyond their capability from the perspective of clarity or cost of operation.
- The newer media selections allow older filters to reach higher levels of performance, so they did not have to be replaced.
1980s and 1990s
- High loft fabrics were moved into applications where more depth filtration was an advantage over surface filtration.
- The previous primary selection parameter of “weight per yard” had to be supported with the air permeability specification. Air permeability has a better correlation to the liquid flow characteristics as the media intercepts the solids. Loftier materials drove this since the weights could not be used alone anymore.
- Micron ratings became more noticeable as other filter manufacturers used them as their key parameter. However, the ratings are not as significant here, and they are used differently. When an application has a wide range of particle sizes, micron ratings are more helpful when the selection is close to the largest particle. If the micron rating was selected to match the smallest particle, the media will blind prematurely. Of course there are also many sensitive applications with a narrow range of particle sizes, which use micron ratings the conventional way.
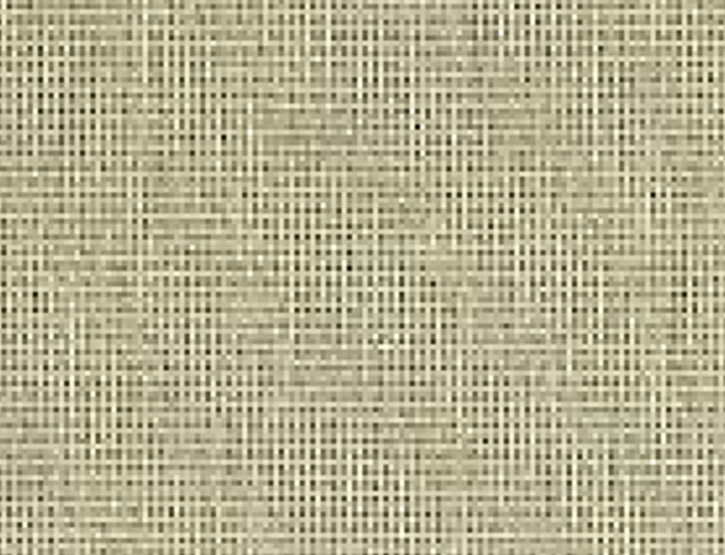
1990s and 2000s
- This era brings in new challenges and new promises related to the use of nonwovens.
- Environmental issues are increasing the pressure on many plants to consider using reusable (permanent) media to meet the solid waste disposal limits they face. The use of permanent media is not practical on many applications and not economical on some present filter equipment designs.
- There are some efforts to develop ways to wash disposable nonwoven media right on the filter so it can be reused a number of times before it has to be discarded.
- The growing technology of producing more sophisticated fabrics offers users the ability to address other problems which have not been possible in the past. One case which still is in the early stages is a coated material to assist in dealing with tramp oil.
There is a much more to be considered between the lines of this brief history, but this should provide a sense for how we got to the current era of coolant filtration. If you have questions or would like added perspective, please feel free to contact me at the information provided below.