Founded in 1961, Porex is a global leader in developing custom-engineered porous polymer solutions that become high-value functional components for a range of products. The company’s material solutions leverage a variety of porous polymer technologies, including sintered plastics, bonded fiber, open-cell foam, and microporous membranes. By combining material science expertise in filtration, absorption, diffusion, wicking and venting with its global manufacturing capability, Porex helps manufacturers in life sciences, electronics, consumer and industrial industries turn their product ideas into reality.
In 1961, Bob Dickey, a research scientist, started a small business making sheet material out of various polymers to be used in a caustic fluid separation process. The team applied their new technology to the first porous plastic nibs for writing instruments, a market which Porex continues to serve today. The unique properties of porous plastics combined with Porex’s design and engineering expertise fostered continued growth that spurred the company’s entrance into global markets and led to key acquisitions, including the purchase of Essentra Porous Technologies in 2017.
Due to the rise in infectious disease testing resulting from the COVID-19 pandemic, we have seen increased demand for our pipette tip filters that protect samples from aerosols and cross-contamination to ensure safe and accurate testing outcomes. Porous polymer tubes are also used in bioprocessing applications to filter cells during vaccine development.
In 2013, Porex became a member company of the Filtration Group. Filtration Group began in 2009 and has rapidly grown to become a global leader in the filtration industry. Serving the life sciences, industrial, fluid and indoor air quality markets, Filtration Group is consistently recognized as one of the fastest growing filtration businesses in the world.
In this edition of the IFN Executive Q&A, we speak with Robert Carpio, president of Porex Corporation.
Ed Gregor: Has Porex been successful in growing the top line sales in filtration over the years? Any examples of recent successes?
Robert Carpio: The short answer is yes. We have seen consistent growth across various markets due to our unique collaborative innovation process with our customers and our ability to customize our technology to fit their specific needs.
Due to the rise in infectious disease testing resulting from the COVID-19 pandemic, we have seen increased demand for our pipette tip filters that protect samples from aerosols and cross-contamination to ensure safe and accurate testing outcomes. Porous polymer tubes are also used in bioprocessing applications to filter cells during vaccine development.
Beyond the life sciences, we’ve seen an increase in porous polymer filtration media used in water purification for the development of beverages such as beer and coffee, as well as consumer water bottles.
Ed Gregor: Historically, what has been the company’s most successful filtration product or technology? What end markets seem to benefit the most from porous filtration media?
Robert Carpio: Porex’s most successful filtration production technology continues to be our pipette tip filters. Invented by Porex over 25 years ago and now the industry standard, these filters continue to play a critical role in increasing the accuracy of laboratory test results and enhancing safety for lab personnel.
As a 2019 winner of the Edison Award, our FORTRESS pipette tip filter technology is the industry’s first certified liquid and aerosol barrier filter, setting the bar for sample protection and accurate test results in analytical, clinical and blood transfusion laboratories.
In the life sciences markets, our porous filtration media are used to filter out many types of particulates that can contaminate samples and medical devices. This same particulate filtration concept can be used in a wide range of markets, from industrial sensors to water purification. We work closely with our customers to develop the filtration media to meet the specifications needed for their products.
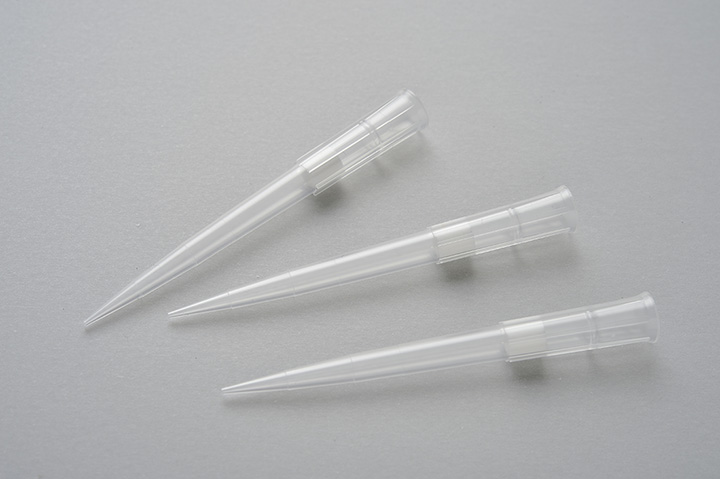
Ed Gregor: Why did Porex join the Filtration Group and what have been the benefits?
Robert Carpio: Seeing the company’s track record for driving innovation and developing unparalleled filtration solutions across a broad spectrum of applications, Porex joined Filtration Group in 2013 in their mission to help customers create products that make the world safer, healthier and more productive. As part of a large global entity, Porex has access to more resources, which allows us to focus on growth with and innovation for our customers.
Ed Gregor: How does the porous filtration technology from your sister company, Oxyphen, compare to Porex’s filtration media?
Robert Carpio: With Filtration Group’s acquisition of Oxyphen in 2020, we’ve added track-etched membrane technology to our portfolio of porous polymer solutions. Track-etched membranes (TEM) have a more precise and controlled pore density and volume than typical microporous membranes on the market, making them ideal for high-precision filtration applications. While Porex’s porous technologies use depth filtration to filter out particles, TEM technology uses surface filtration, which means that particles are captured on the surface of the membrane. TEM technology can also be used in sterile filtration applications, such as cell culture inserts used in tissue engineering.
Ed Gregor: In your opinion, which of your many technologies is under-utilized by the filtration market?
Robert Carpio: Because of the custom nature of porous plastic media, the filtration component can be engineered to do more than just filter in the customer’s end product. The filtration media can remove steps in the manufacturing process by eliminating the need for multiple components or can add capabilities via additives or treatments. I’m most optimistic about the many ways we will be able to solve more problems for our customers by leveraging the full breadth of our products’ capabilities.
Ed Gregor: If you had a magic wand, are there any new technologies you would like added to Porex filtration capabilities?
Robert Carpio: A collaborative partner, Porex is always keeping up with the market and working with our customers to create innovative solutions. As a part of that process, we constantly explore avenues for advancing our technologies and anticipating market needs. In the filtration arena, we look for ways to achieve smaller pore size, greater filtration efficiency, lower pressure drops, and greater flow.
Ed Gregor: Any filtration products you care to mention?
Robert Carpio: I’m very excited about our recent announcement of the Porex Life Sciences Institute, a new innovation center designed to accelerate progress in the life sciences through more integrated solutions. As its inaugural product, the Saletto saliva collection device goes beyond collection to filtering out impurities and ultimately generating a test-ready saliva sample in seconds for all types of saliva-based diagnostic assays, including COVID-19.
In addition, we recently launched an innovative automotive filter technology to help manufacturers meet more stringent global vehicle emissions requirements and optimize engine performance. Our filtration media for closed crankcase ventilation (CCV) systems effectively removes oil mist and particulates from crankcase blow-by gases, prevents clogging and allows for lower pressure drops to improve vehicle efficiency.
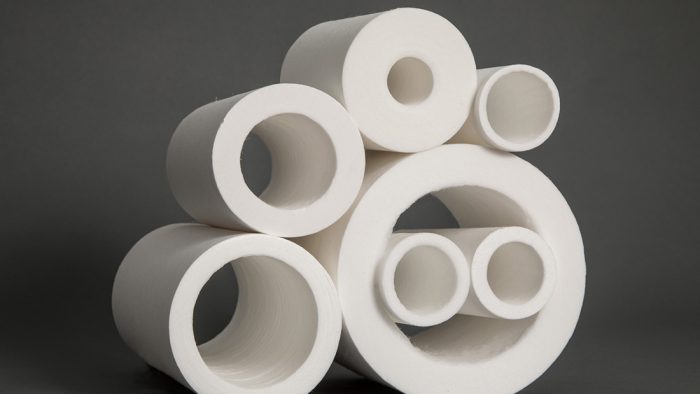
Ed Gregor: What future trends do you foresee in filtration for porous plastics?
Robert Carpio: As the industry continues to demand more sustainable solutions, the use of post-industrial and post-consumer recycled materials will become more common. As part of our mission to help make the world safer, healthier and more productive, we recently announced sustainable design capabilities across all of our porous technology platforms so that customers are able to work with us to reduce the use of virgin plastics in their products.