The Importance of a Quality Assurance/Quality Control Program When Purchasing Fabric Filters
The value of fabric and bag Quality Assurance/Quality Control program, bag installation oversight, and bag monitoring program increases as the code requirements become more stringent. The intrinsic value of the QA/QC program is driven by the fact that the failure of even one bag can cause dust contamination on the clean side of the baghouse. This, in turn, leads to widespread premature bag failure and/or pressure drop increases. Recent new fabric and bag QA/QC programs have detected membrane failures, out of spec strength and permeability, fabric shrinkage concerns, bag punctures and significant dimensional and construction issues.
The following are a brief description of the test methods currently employed in a QA/QC program.
Air Permeability
The air permeability is used to determine the amount of air that can flow through a given cloth area. Permeability is defined in ASTM Standard D737 as the rate of air flow passing perpendicularly through a known area of fabric which is adjusted to obtain a prescribed air pressure differential between the two fabric surfaces.
The failure of even one bag can cause dust contamination on the clean side of the baghouse.
Mullen Burst
The Mullen burst strength test, described in ASTM Standard D3786, is designed to show the relative total strength of fabrics to withstand severe pulsing or pressure. Fabric strength is determined by measuring the pressure required to rupture the specimen from inflation of an expandable diaphragm.
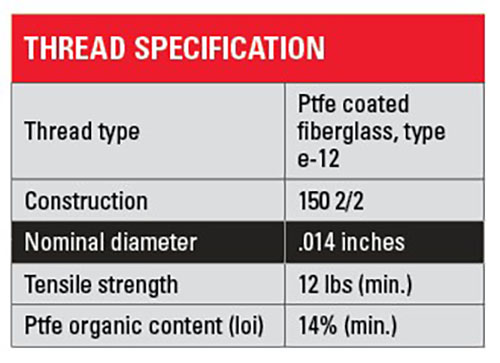
Tensile Strength
The tensile strength test provides data on fabric strength and elongation. The ASTM Standard D5055 provides raveled strip (woven fabrics) and cut strip test procedures (nonwoven and felted fabrics) for determining the breaking force and elongation of most textile fabrics.
M.I.T. Flex Endurance Test
The M.I.T. flex endurance test primarily measures the relative value of fabric to withstand self-abrasion from flexing by measuring the number of flex cycles necessary to break a fabric sample. The test method is described in ASTM Standard D2176 which is the standard method for testing the folding endurance of paper. The fabric samples are tested in both the warp and fill directions.
The M.I.T flex test has traditionally been used to help determine the rate of deterioration of woven fiberglass bags used in the coal-fired utility boilers due to the inherent abrasiveness of glass fibers. ETS has also found the M.I.T. flex test to be very useful in the evaluation of many felts and their ability to withstand flexing against a wire cage during pulse cleaning cycles. For nearly all filter bag fabric types, this test can be a leading indicator that the fabric is nearing the end of its useful service life.
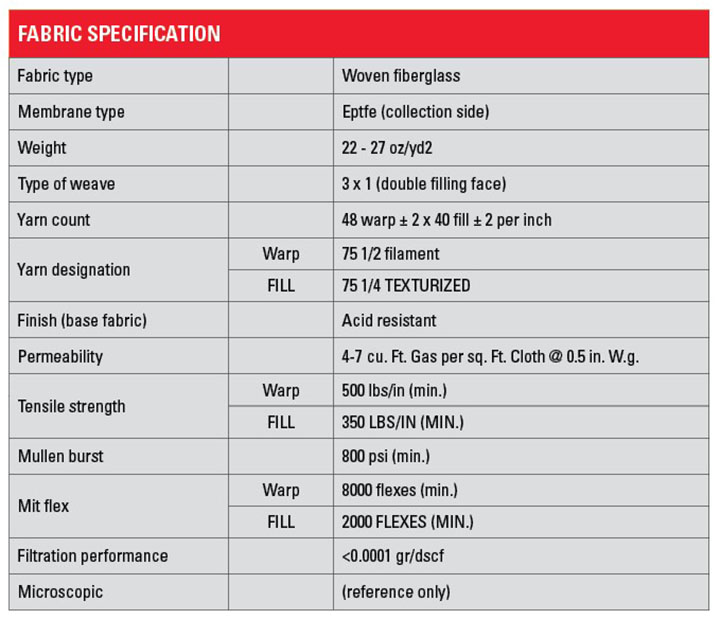
Filtration Performance
The filtration performance test apparatus developed in Germany measures filter media performance under defined conditions with regard to filtration velocity, particle size distribution, and cleaning requirements, simulating actual baghouse conditions.
Fourier Transform Infrared Spectroscopy (FTIR)
FTIR is a technique that uses infrared light to observe properties of solid, liquid, or gas. In infrared spectroscopy, IR radiation is passed through (transmitted). The resulting spectrum represents the molecular absorption and transmission, creating a molecular fingerprint of the sample. FTIR analysis results are generally utilized for identification of materials of construction (e.g., fiber type, thread type) of filter bags and/or evaluation of contaminants.
Comprehensive Monitoring Programs
Long-term monitoring programs compliment QA/QC programs. All the strength and flow tests should be done in conjunction with each other periodically in order to develop the loss of strength and flow trend lines over time. The testing program can identify when the bags are approaching end of life and higher risk of failure, but cannot predict the exact timing of the end of life of the bag set. Permeability measurements of used bags can, by varying the amount of vacuuming, help to determine if the bags are gradually blinding (losing permeability). Used bag test values are compared with the original clean fabric test values to show rate and level of deterioration.
Conclusion
Today the primary reasons for conducting fabric and bag QA/QC include:
- Minimize baghouse and production downtime by ensuring that the specification is met and related bag failure precluded.
- Protect the user in the event of warranty issues by providing baseline data.
- Provide an unbiased third-party assessment of faulty fabric and finished filter bags.