“The U.S. has a strategic petroleum reserve. It has strategic military assets. Where are the strategic meltblown assets?”
This was the question with which Forbes investment specialist William Baldwin closed a column on April 3rd, immediately after U.S. President Donald Trump had issued a blistering attack on 3M during a press briefing in Washington.
3M had at that point been under intense public pressure from Trump for continuing to supply facemasks to other countries, and on Thursday April 2nd, he invoked the Federal Production Act – last used in the Korean War – giving his administration the right to use “any and all authority” to procure the protective equipment it needs.
3M, which is headquartered in Maplewood, Minnesota, with global manufacturing sites, responded that cutting off the supplies of protective equipment to Canada and Latin America at that stage could cause a humanitarian crisis.
These events capped an extraordinary few weeks in which shortages of disposable face masks and other items of PPE, such as medical drapes and gowns, pushed the production of meltblown nonwoven fabrics – usually employed in hygienic disposables as well as a wide range of filtration applications – to the top of the global political agenda in response to Covid-19.
French initiative
Earlier that week, on Tuesday March 31st, French President Emmanuel Macron had toured the facemask manufacturing plant Kolmi-Hopen, in Saint-Barthelemy-d’Anjou near Angers, to reassure French citizens that his government was investing and working to increase output.
The following day, French and German officials were accusing the U.S. of using “wild west tactics” and a policy of “modern piracy” in a dispute over a facemask shipment from China.
As politicians blustered, manufacturing industries across the U.S. and Europe were mobilizing and coming together to provide concrete solutions.
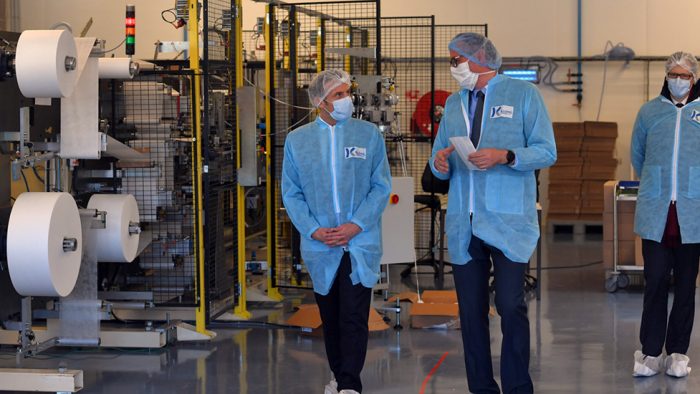
3M expansion
Even prior to COVID-19, 3M already produced around 1.1 billion face masks at its global sites annually – specifically the highly effective N95 respirator-type masks
At the end of March, however, the company put into motion additional investments to enable it to increase its capacity once again, to 2 billion globally within 12 months – with some of that additional capacity beginning to come online in 60-90 days.
In the U.S., 3M said it expected to be producing N95 respirators at a rate of 50 million per month by June – a 40% increase from levels in March.
The company is prioritizing and shipping products to serve the most urgent needs in the COVID-19 pandemic. In the U.S., more than 90% of 3M N95 respirators are going to healthcare and public health, with the remaining deployed to other critical industries such as energy, food, and pharmaceuticals.
Of 3M’s U.S. supply directed toward healthcare and public health, roughly 80% is reported to be flowing rapidly through healthcare distributors – primarily consisting of six large and well-known companies with huge logistical capabilities – as the quickest and most effective method of getting those supplies into the hands of workers.
Cummins
3M has also partnered with filtration leader Cummins to utilize labor and equipment typically used for producing diesel engine filters to manufacture high-efficiency particulate filters for powered air purifying respirators (PAPRs). PAPRs use a battery-powered blower that sends filtered air into a hood or head top and can provide increased levels of respiratory protection.
Cummins is using existing manpower and equipment at its Neillsville, Wisconsin facility to pleat the media, assemble it into cartridge housings and do final testing before shipping the filters to Valley, Nebraska, where 3M’s PAPRs are manufactured.
Cummins’ NanoNet and NanoForce filter media employing DuPont’s Hybrid Membrane Technology (HMT) are also being employed in new N95 respirator masks developed at the University of Minnesota.
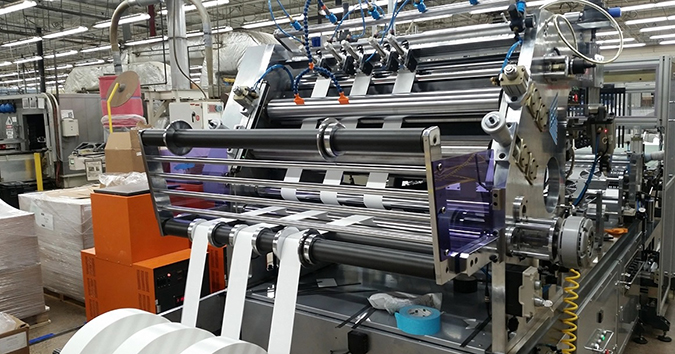
Ford PAPRs
Mann+Hummel is meanwhile collaborating with Ford on the production of PAPRs, shipping around 3,500 HEPA micro-glass fiber filter elements per day from manufacturing sites in the U.S. and Germany, as the automotive manufacturer targets the manufacture of 100,000 respirators in a two-month period.
As part of its Apollo Project COVID-19 response, Ford is also manufacturing both facemasks and respirators in close collaboration with 3M and assisting its supplier Joyson Safety Systems to manufacture reusable gowns from airbag materials.
Honeywell expansion
Honeywell, headquartered in Charlotte, North Carolina, is the other major U.S. manufacturer of N95 masks and announced at the end of March that it was expanding operations at its plants in Smithfield, Rhode Island and at Honeywell Aerospace in Phoenix, Arizona. It said it would hire at least 500 new workers at both expanded sites.
“We’re doing something that normally takes nine months in a matter of six to eight weeks,” said Will Lange, president and general manager of Honeywell Personal Protective Equipment.
Honeywell explains that with N95 masks, the N is a Respirator Rating Letter Class that stands for “non-oil,” meaning that if no oil-based particulates are present, it can be used in the work environment. Other masks ratings are R (resistant to oil for oil hours) and P (oil proof).
Masks ending in a 95, have a 95% efficiency, which means they filter out contaminants like dusts, mists, and fumes. The minimum size of 0.3 microns of particulates and large droplets will not pass through the barrier, according to the U.S. Centers for Disease Control and Prevention (CDC.) The filtration material of the mask is an electrostatic polypropylene meltblown and some disposable N95 masks come with an optional exhalation valve, which makes it easier for wearers to breathe, according to the CDC.
Rapid response
China wasted no time in responding to its own facemask shortage and by mid-March was reported to be manufacturing 200 million a day – more than 20 times the amount it made at the start of February – with factories that previously made shoes, iPhones and cars being retooled to the task.
In a press release issued on March 13th, Shenzen-headquartered BYD, one of China’s largest privately-held companies, which is backed by U.S. entrepreneur Warren Buffet, announced that it had rapidly created the world’s largest mass-produced nonwoven facemasks plant.
The plant is now running at full capacity and by mid-March was producing five million masks a day, in addition to 300,000 bottles of disinfectant, in response to the severe shortages that have affected hospitals and agencies across China.
It was only in late January that a special task force was established consisting of leaders from different BYD business divisions and more than 3,000 engineers involved in research and development, design, processing, and other roles.
By February 8th, newly built production lines in one of BYD’s industrial parks in Shenzhen began to produce the facemasks, with hundreds of staff working day and night shifts on machines operating around the clock.
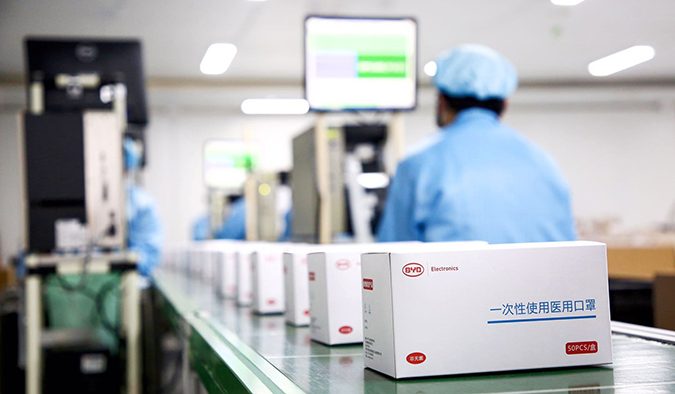
Meltblown
Of nonwoven media manufacturers, PFNonwoven is adding a new meltblown line in the U.S. and Berry Global is adding one at an unspecified location in Europe. Berry has also expanded its proprietary Meltex platform to add meltblown capacity in Waynesboro, Virginia. This capacity was quickly converted from a pilot line into one that provides full commercial output.
In further initiatives from nonwoven filter media manufacturers and their customers:
- On April 23rd, Ahlstrom-Munksjö announced a deal to supply equipment for the French government’s Resilience project, under which it will produce material equivalent to 100 million face masks for the police, prison administration and social workers as well as companies active in essential sectors e.g. food, energy, water and waste. In accordance to the newly implemented guidelines issued in France, the company’s Reliance range of fabrics – typically used for the manufacturing of sterilization wraps for surgical instruments –have been declared compatible for this purpose, with Reliance SMS 200 and Reliance SMS 300 grades also meeting N95 standard. Ahlstrom-Munksjö has expanded capacity at its plant in Turin, Italy, where it is now making enough material for a monthly 60 million face masks.
- In Austria, Lenzing AG and Palmers Textil have founded a new company called Hygiene Austria which started producing and selling protective masks in May. The new company plans to build up capacity to over 25 million face masks per month.
- As the sole manufacturer of medical spunbond and meltblown nonwovens in the UK, Don and Low has allocated all its resources to support local manufacturers of face masks, medical protective apparel and medical wipes. It has also dedicated 100% of its disposable gown material to the NHS and is supplying it with five million meters of medical wipes material. In April, the company received an order from the UK government to make 7.4 million meters of disposable gown materials by May, to be sewn and welded into 3.5 million gowns at other sites, including leading fashion brands such as Barbour and Burberry.
- Sandler Group has invested in a new line to produce face mask fabrics in Germany. Once up and running, the new line will increase Sandler’s annual production capacity of nonwovens for up to 800 million masks. Start up for the line is scheduled for the middle of the third quarter of 2020.
- The Johns Manville plant in Richland, Mississippi, which normally supplies its polypropylene and polyester meltblown nonwovens for various air and liquid filtration applications, has pivoted to making face mask materials.
- DuPont has launched the #TyvekTogether program to increase the overall availability of Tyvek personal protective garments. At full capacity, it could deliver six million additional non-surgical isolation gowns per month.
- Leading automotive Tier 1 Bosch has converted machines in Germany, India and Mexico to manufacture more than 500,000 face masks per day for the protection of its 400,000+ global employees.

Technology
Two of the biggest manufacturers of spunmelt nonwovens technology, Reifenhäuser Reicofil and Oerlikon Nonwoven, have both announced shortened delivery times for meltblown technology.
They have turned over their own testing lines to the production of emergency meltblown supplies for face masks and are operating four-shift production. Reicofil’s two pilot lines in Germany have a combined capacity for making enough fabric for one million face masks a day. Currently, the company is restricting this supply to German customers. Reicofil is also supplying the new meltblown line to Berry Global.
Oerlikon is currently working to supply a leading Asian large-scale manufacturer of manmade fibers with a new two-beam meltblown system with a nominal capacity of up to 1,200 tons.
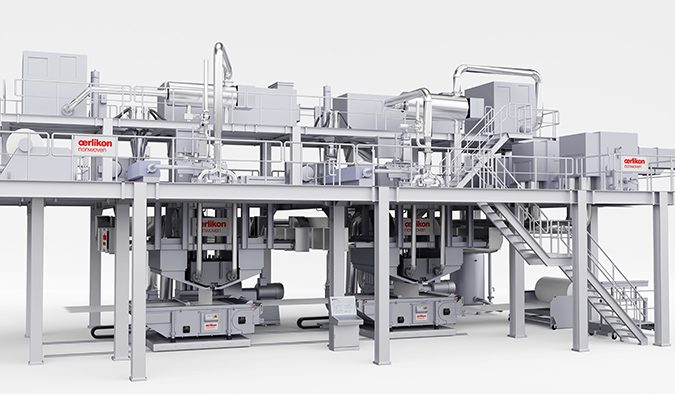
Bicomponent alternative
The Nonwovens Institute (NWI) at North Carolina State University has meanwhile created a new bicomponent spunbond material that can serve as an effective filter without the need for a meltblown filtration layer.
“We took the spunbond technology and created a new generation of unique filters that have excellent filtering capability and can potentially be reused after cleaning with peroxide, or potentially alcohol solution,” said executive director Benham Pourdeyhimi. “Because these materials are strong, unlike classical meltblown filters, they can also be cut and sewn by traditional techniques.”
“Typically, one meter of spunbond material provides enough for about 20 to 25 masks when using the current designs. One of the NWI’s production lines started producing 2,000 meters of spunbond material per hour, with the potential to create some 20,000 meters in a day.”
Ingeo
The new nonwoven fabric can be based on bicomponents of Ingeo biopolymer (PLA) and polypropylene (PP), and on April 22nd NatureWorks reported that it was donating enough Ingeo to produce as many as two million reusable N95 masks per week to the NWI.
Ingeo is said to improve the productivity of the spunbond process by at least 30%.
NWI currently has an agreement to provide large amounts of spunbond nonwoven material to several key partners, which will make masks at their manufacturing facilities. NC State is also awaiting machines that will allow it to make surgical masks on campus.
NWI’s other production line is a state-of-the-art meltblowing pilot line and is making the classical meltblown material for N95 masks and surgical masks.
The meltblown material takes a bit more time to produce – Pourdeyhimi estimates that this line can make about 12,000 meters of the material a day.
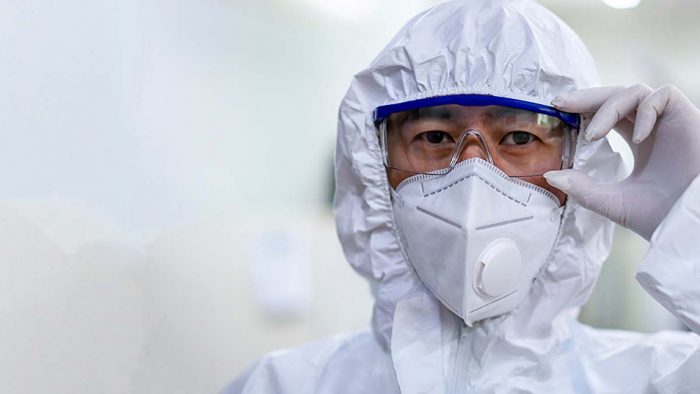
Synergex ONE
In what may or may not be a related development – the company declined to either confirm or deny it, or supply any further details – Berry Global is rushing out a new fabric in Europe it says has the potential to relieve the severe bottleneck that the need for meltblown layers in N95 standard facemasks is causing.
Synergex ONE is described as “a multilayer nonwoven composite product in a single sheet” and has been initially developed to meet the new facemask categories for the general population. The aim, however, is to quickly bring the media up to N95 standard for surgical masks.
Tip of the iceberg
The activities reported in this article doubtless represent the tip of the iceberg in respect of all the industrial work that’s going on, but the national shortages in PPE experienced in the U.S. and across Europe in recent months have served a larger purpose.
With 80% of these essential materials supplied from China prior to the outset of Covid-19, the issue has contributed to exposing a major fault in the globalized world order that existed before it and is now being forensically scrutinized for the future.
The question is, once the emergency is over will this be an issue that American and European governments seek to learn from and act on, or will it just be conveniently swept under the carpet with China back to full production?